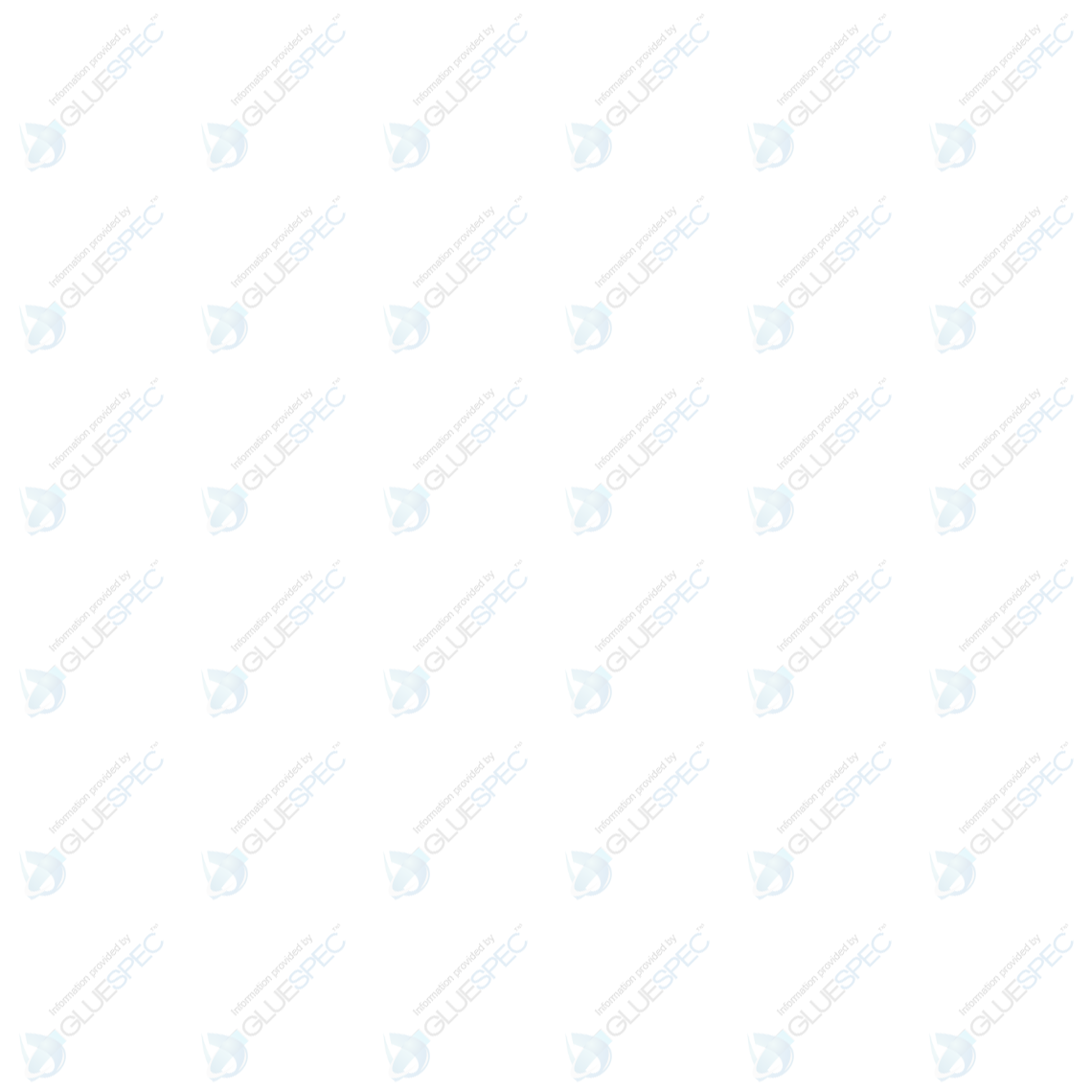
- Contributions by industrial experts with engineers in mind
- Focused on specialty-chemical material applications and selection
Knowledge Center
Electrically Conductive Adhesives Q&A
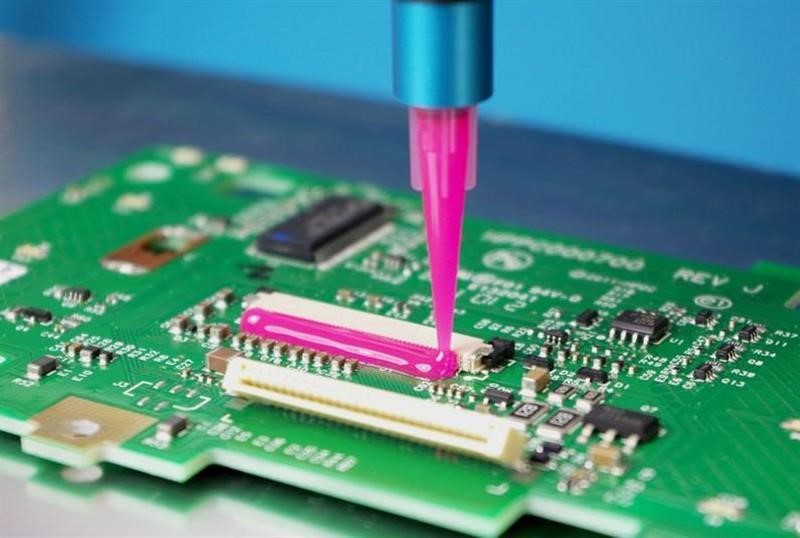
Electrically Conductive Adhesives Q&A Intro
Electrically conductive adhesives bond electronic components to substrates and permit the flow of electrical current. Unlike most adhesive products, they are not electrically insulating. Typically, electrically conductive adhesives are used with printed circuit boards (PCBs), dies, and temperature-sensitive substrates such as displays and panels. For design engineers who need help with electrically conductive adhesives, this Q&A from Gluespec® provides answers to frequently asked questions (FAQs).
Q: I’m designing a PCB that requires an electrically conductive adhesive. What do I need to consider during product selection – and how does this differ from other types of adhesives?
With any type of adhesive, it’s important to determine whether the product is compatible with the substrate and can withstand service conditions such as operating temperature, humidity levels, and exposure to chemicals. The adhesive’s thermal conductivity, flexibility, and application and curing methods are also selection requirements. With electrically conductive adhesives, the amount of electrical conductivity is a major concern. Applications that conduct device current require adhesives with greater electrical conductivity. For applications such as basic protection against electrostatic discharge (ESD), a product with a lower level of electrical conductivity may be appropriate.
Q: How is electrical conductivity measured in electrically conductive adhesives?
Typically, the unit of measure is ohms centimeters (ohm-cm), the inherent resistance of a material to the flow of electrical current. The lower the ohm-cm (resistance), the more electrically conductive the adhesive. The higher the ohm-cm, the less electrically conductive the adhesive.
Q: Within the adhesive, how is electrical conductivity achieved?
Adhesive formulators add electrically conductive fillers to a base material, or chemistry. Generally, silver filler is used to achieve high levels of conductivity. Metals such as nickel or materials such as carbon may be used in conjunction with silver, or by themselves, to achieve the specific amount of electrical conductivity needed for a device design. When lower electrical conductivity is required, such as in some ESD protection applications, carbon filler may be used.
Q: I’ve heard about adhesives that are electrically conductive in only one direction. What are they?
They’re called anisotropic conductive adhesives. They conduct current in one only dimension, such as in the Z-axis but not in the X-axis and the Y-axis. Typically, anisotropic adhesives are used in chip packaging, liquid crystal displays (LCDs), flat panel displays, smart cards, and mobile phones. These specialized adhesives are formulated with conductive fillers and other fill materials that impart the ability to conduct electricity in only one direction.
Q: What are the available chemistries for electrically conductive adhesives?
Although it is possible to make most adhesive chemistries electrically conductive, the majority of liquid adhesives that are electrically conductive use epoxy or silicone chemistries.
Q: What are the advantages of these different chemistries?
Epoxy adhesives can be loaded with conductive particles to achieve high levels of electrical conductivity. These products are available in higher-durometer formulations that are more rigid, but they can also be modified to impart some degree of flexibility. Epoxy exhibits strong adhesion to many substrates and has good resistance to moisture, weather, and chemicals. Electrically conductive adhesives with epoxy chemistries can be used in high-temperature applications, often 150°C or higher.
Silicone adhesives can also be loaded with conductive particles that impart high electrical conductivity. Silicone is less rigid than epoxy, however, and is a good choice for applications where some movement and shock absorption is required. Electrically conductive adhesives with silicone chemistries adhere well to many of the substrates used in electronic assembly, and these silicone formulations also resist exposure to weather and chemicals. Electrically conductive silicone adhesives are used in high-temperature applications up to 260°C and may be able to withstand somewhat higher temperature conditions.
Q: Are electrically conductive adhesive tapes available?
Yes, electrically conductive adhesive tapes are available. These are often used in grounding applications that provide shielding against electromagnetic interference (EMI) or radio frequency interference (RFI). With electrically conductive adhesive tapes, acrylic is the most common chemistry. The advantages of electrically conductive adhesive tapes are that these products are convenient to use, employ fast pressure-sensitive bonds, exhibit good adhesion to a variety of substrates, and can be formulated for high electrical conductivity. They can be used in moderate temperature applications up to about 85°C in continuous service and up to about 120°C for short periods of times