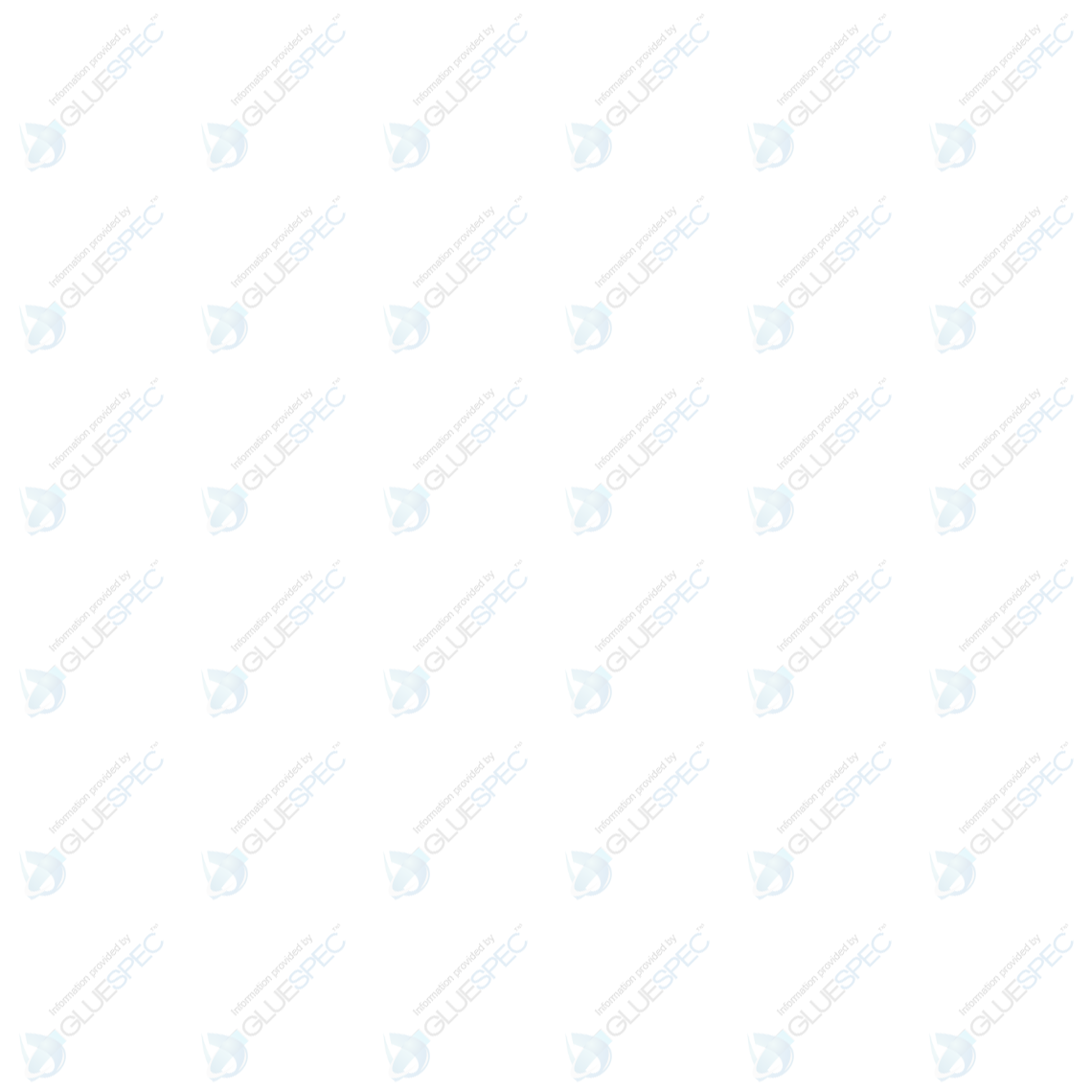
- Contributions by industrial experts with engineers in mind
- Focused on specialty-chemical material applications and selection
Knowledge Center
Case Study: Creating reliable, corrosion-free bonds with LORD® 406 acrylic adhesive
LORD 406-19GB Two-Part Acrylic Adhesive for Wheel well Bonding
In heavy manufacturing, when it comes time to bond two metal substrates, welding is the common default of method. If adhesives are overlooked, however, opportunities may be missed to improve the performance of the finished equipment.
The challenge
A manufacturer of utility vehicles — boom trucks for industrial buyers — determined that the welding process used for bonding two cold-rolled steel parts in wheel wells was not up to its standards. Not only was it time-consuming to weld the parts together, the weld spots showed signs of corrosion as the trucks aged. The company decided to seek out alternatives to welding, in the hopes of both smoothing its assembly line processes and improving the quality of its vehicles.
The solution
To find a process that could compete directly with welding, the manufacturer needed to test out a strong industrial adhesive capable of bonding two metal substrates. In this case, that meant the LORD® 406-19GB two-part acrylic adhesive.
The choice of 406-19GB reflects the requirements of the job. This series of LORD® adhesives is organized by cure time. While 403's 2-4 minute work time before curing gave workers too little time to finish assembling the wheel well, the 20-45 minutes of the 410 was too much. This led them to the 406, which allowed a 6-10 minute work time. The 19GB accelerator contains glass beads, creating an even application and uniform thickness, important for creating a reliable bond.
The LORD® acrylic adhesive series is capable of bonding dissimilar metals, though in this case, both parts are made of the same cold-rolled steel material. Furthermore, it is possible to create an acceptably strong bond even without wiping the substrates down with isopropyl alcohol, preventing the process from slowing down, even in a greasy factory setting.
These acrylic adhesives can also bond to painted parts, though with a caveat. The bond between the adhesive and the paint will be strong and not fail under normal conditions. It is the bond between the paint and the underlying substrate that manufacturers need to worry about. If the paint peels away, problems will result.
The adhesive methodology was put through its paces, with the wheel wells' bonds tested in the factory for strength using a lab shear test. These inspections are designed to make sure the joint can hold up to shock and vibration as well as the welds. Wheel wells built with the new approach were then disassembled and inspected after a year in the field to make sure the corrosion problems that afflicted the welded parts did not also affect the ones assembled with adhesive.
The results
The LORD® 406-19GB product held up admirably, passing the tests and not just equaling the performance of welding but surpassing it. The manufacturers observed numerous results that convinced them the new process was worth keeping.
For example, the adhesive provided equal or better structural integrity in wheel wells when compared to the welded versions. The trucks were also less noisy to operate, because the adhesive acted as a buffer and did not cause the metal-on-metal sounds that can occur when parts are welded. The glass beads, creating an even level of thickness, ensured the bond area was smooth and uniform. In lab tests from vibration to shock resistance, the adhesive outperformed welding.
In addition to the strength of the acrylic, it also took away the other main drawback of welding: the corrosion that would occur at the joints after the utility trucks had served in the field. Corrosion can be a major impediment for long-term reliable use of vehicles, exacerbated by factors including road salt and atmospheric moisture. Counteracting corrosion is therefore a way to increase the enduring value of industrial vehicles.
Adhesives don't just provide performance advantages compared to welding — they are also less time-consuming and labor intensive on the assembly line. Applying acrylic adhesive requires less time and effort than welding, which reduces the labor outlay on a given vehicle. In the end, the manufacturer achieved all of its goals by changing the bonding process.
Other potential applications for LORD 406-19GB Two-Part Acrylic Adhesive
The LORD® 400 series of adhesives can function outside of the automotive field. Large metal products that require solid bonds are good use cases, from trailers to vending machines. Manufacturers like working with LORD® because the producer provides high-quality customer service. LORD® is even capable of performing in-house testing to determine whether a particular adhesive is truly the right option for a customer's products.
If your current manufacturing processes need an improvement, or if you are preparing to begin a new project, it pays to consider your options for industrial adhesives and encapsulants. Gluespec is your resource for discussing these challenging applications.