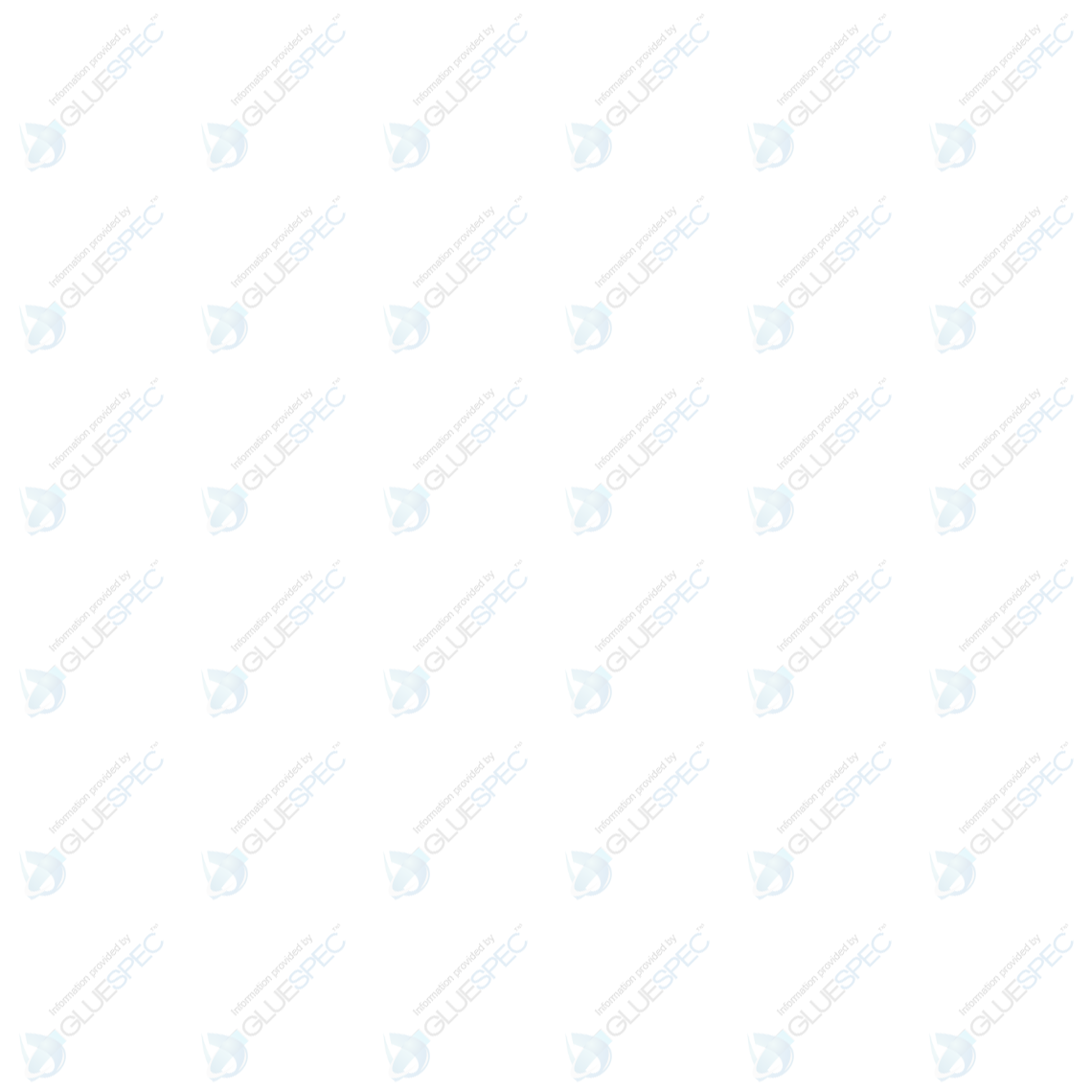
- Contributions by industrial experts with engineers in mind
- Focused on specialty-chemical material applications and selection
Knowledge Center
Converting Services Q&A
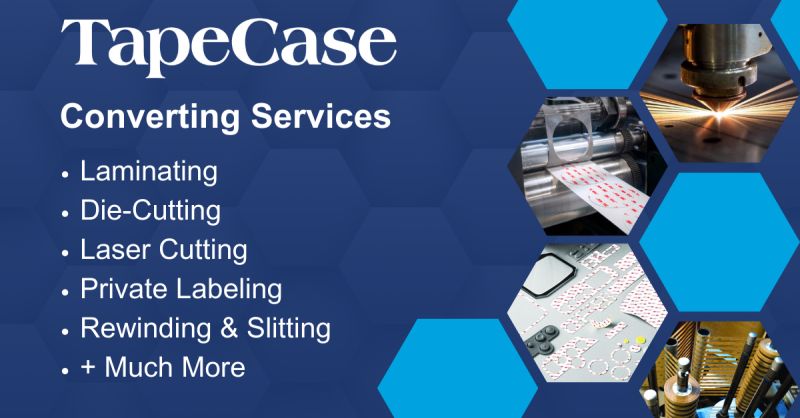
TapeCase of Elk Grove Village, Illinois converts tapes, films, foils, foams, rubber, thermal management materials and other flexible materials into highly engineered products. The company was founded in 1972 and acquired by Ellsworth Corporation in 2022. Brett Hirsh, Senior Sales Engineering/Business Develop Manager, recently spoke with us about how TapeCase solves product design and development challenges.
Q: TapeCase converts many 3M™ materials. How do you add value to them?
Here’s one example. 3M™ Safety-Walk is a slip-resistant tape with a vinyl surface and pressure-sensitive adhesive (PSA). A supplier to the staircase industry wanted to keep using this product but was having problems with adhesion. Vinyl contains a lot of plasticizers, and these substances can affect a tape’s adhesive bond.
TapeCase suggested applying a plasticized vinyl resistant adhesive to the anti-slip material. This improved the tape’s adhesion and immensely streamlined production. This provided our customer with a significant labor savings while improving the product’s performance.
Q: What’s an example of how adhesive tape can replace fasteners?
TapeCase has a customer that makes air purification systems for residential HVAC installations. These systems attach directly to HVAC units, but drilling holes and installing fasteners can be dangerous. The customer didn’t think an adhesive tape would be strong enough, but we explained that it takes just four square-inches of tape to hold a pound.
The solution we recommended, a 3M™ VHB tape, needed to pass rigorous testing. First, our customer shared samples with its raw material supplier to ensure that this tape would stick to a powder-coated, painted substrate. TapeCase then tested samples for tensile strength, peel, and shear. We quantified the results and shared them with our customer.
Q: Do you ever combine design assistance with support for automated production?
Yes. A customer who makes a law enforcement device came to us with a design that uses foil tape. This design was so complex that it was difficult to automate production. After three years of product development, their lead engineer visited TapeCase. Based on what this engineer learned from us in a day, the company modified its design.
A TapeCase process engineer then visited both our customer and the supplier of our customer’s automation equipment. They discussed the equipment’s capabilities, including its limitations and tolerances. Today, this highly engineered part is optimized for automation. TapeCase solved tough design challenges and went the extra mile to help automate production.
Q: TapeCase also converts Gore-Tex materials. How have you added value to them?
A customer needed to attach vents made of Gore-Tex, a breathable and waterproof fabric membrane, to a plastic substrate. The volumes were low, and the vents were highly customized. Because the application was for LED lighting, the vents needed to dissipate heat and emit moisure. The customer didn’t think there was an adhesive that would work, but we found a solution.
TapeCase analyzed the airflow rate, temperature, and Ingress Protection (IP) rating. Then we identified a material that would meet these specifications and adhere to curved surfaces. We zone-coated the adhesive to the venting material. Our solution involved applying adhesive to the perimeter and a cold bond along the plastic surface near the opening.
Q: Have you helped customers in the rubber industry?
We have. A rubber extruder wanted to apply tape but wasn’t sure what would work or the best way to apply it. Because of rubber’s surface energy, it’s tough to get double-coated tape to stick. TapeCase explained how corona treatment would change the rubber’s surface energy. We even recommended an equipment supplier. This was for an automotive application, so adhesion needs to be extremely reliable.
The rubber extruder also needed a solution to support continuous in-line production. Our tape supplier only provided rolls in standard lengths, but TapeCase spooled rolls together. This allowed our customer to run its extrusion process without stopping to change rolls. The rubber extruder didn’t know all its options, but we provided a complete solution.
Q: Do you ever work with plastic injection molders?
We do. Overmolding can join parts together, but we recently worked with a molder who needed to take a different approach. There was a part that attached a display. It was a foam gasket that sealed out moisture and water. Our customer wanted to attach this gasket without screws or fasteners, so we recommended the right adhesive for the job.
TapeCase has also provided plastic injection molders with thermal interface materials (TIMs), gap pads, and heat spreaders. They’re all installed inside molded parts. Other materials that we’ve provided include brightness-enhancing films and polycarbonate. Because many medical manufacturers outsource their work to plastic injection molders, we’ve also supported customers in this growing industry.
Q: The EV market is growing, too. Does TapeCase solve challenges there?
Yes. EV battery manufacturers need to build products that are lightweight and heat-resistant. They also want flame-resistant materials that prevent thermal runaway through anti-propagation: the containment of a battery fire to a single cell within a module. TapeCase works with battery manufacturers to stop thermal runaway in the incident of extreme heat issues. These precision cut parts can help keep heat issues isolated to just that small region.
Some of these materials are referred to as intumescent materials, which can be installed between battery cells. These flame-resistant materials are supplied as sheets or rolls and expand when they’re heated for high-temperature insulation. TapeCase also converts silicone foams for cushioning and supplies cut or molded rubber gaskets for enclosure sealing on the battery casing.
Q: Are there any other converting services you’d like to highlight?
Electromagnetic interference (EMI) is a growing challenge, and TapeCase converts fabric-over-foam conductive gaskets from materials made by Parker Chomerics and Schlegel. We also convert foil tapes that fit the small spaces within electronic devices. Along these lines, our solutions have included bonding a 1” diameter part for an electronic motor. The designer engineers didn’t know tape would work here.
Finally, there was a speaker manufacturer who chose us over another converter that was too expensive and not responsive enough. The other converter suggested only one or two material suppliers, but we shared our full catalog. The speaker manufacturer was surprised we could access so many materials. Check out TapeCase and Gluespec’s wide range of tape and flexible materials.