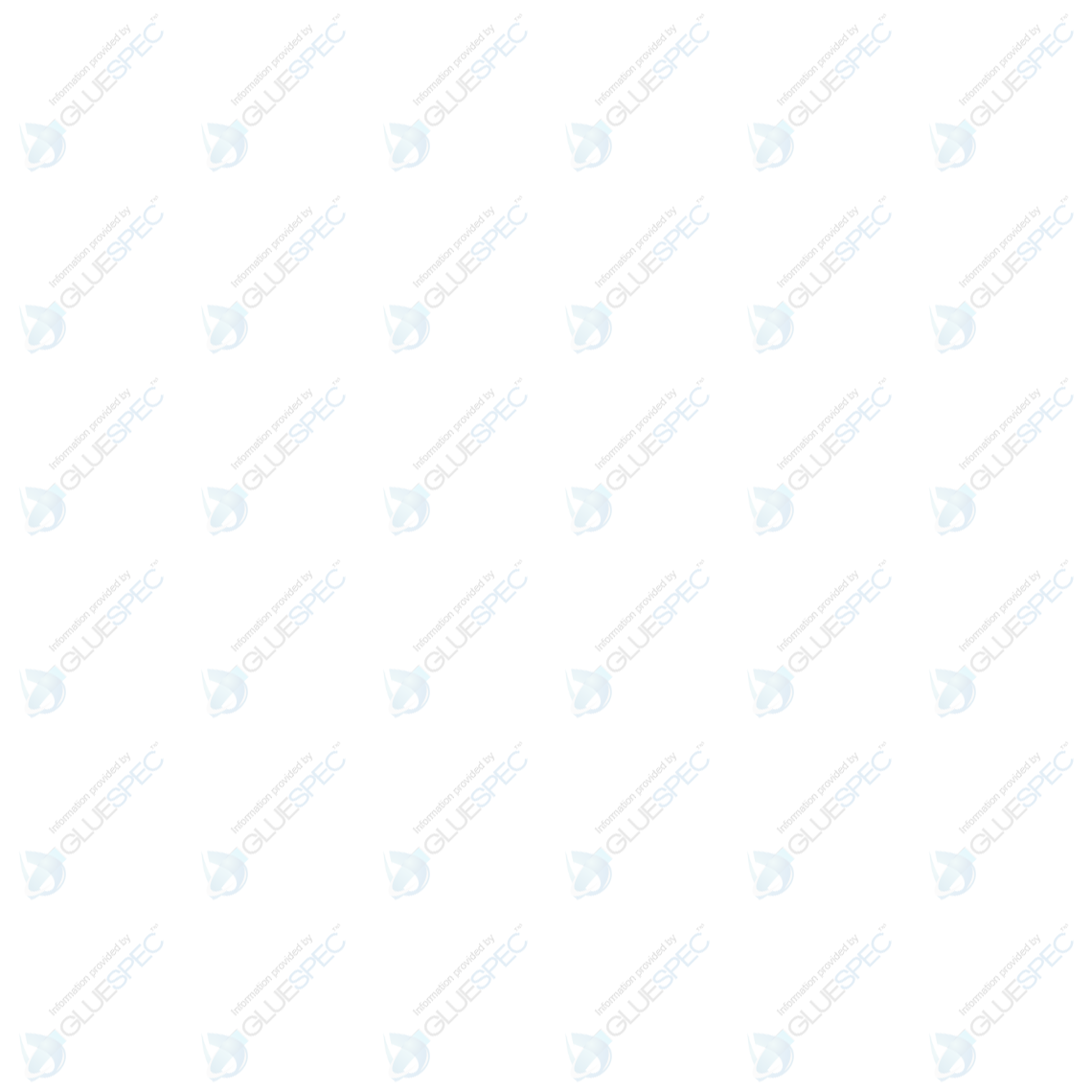
- Contributions by industrial experts with engineers in mind
- Focused on specialty-chemical material applications and selection
Knowledge Center
Contact Adhesives
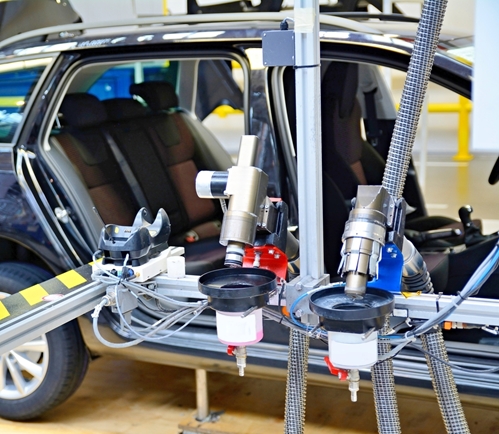
Contact Adhesives
Contact adhesives or contact cements form a unique subsection of the adhesives market, and are ideally suited to some applications where other materials are inadequate. These glues are called "contact" adhesives because they form a near-instant bond when two coated surfaces come in contact. The material itself is made out of synthetic or natural rubber compounds dissolved in solvents or water which can then be applied to surfaces by brushing, spraying or other methods.
Strong, instant bonds
The instant-bond effect of contact adhesives is achieved by applying adhesive to two surfaces, and then allowing the adhesive to dry. Once the adhesive has dried and is no longer tacky to the touch, surfaces can be pressed together. While the glue is not particularly adhesive to other surfaces once dry, it's extremely adherent to itself, forming strong bonds on the order of seconds with minimal pressure. The time needed before joining is usually 15-20 minutes after application, though specific formulations may need a longer time, or be able to be wet-glued.
Once bonded, contact adhesives exhibit good peel and shear strengths. The adhesive is also flexible, and can bond to a wide range of materials. Contact adhesives offer good resistance to water, and retain their strength at temperatures between -30F and 75F. Bonding strength decreases somewhat at higher temperatures.
"Contact adhesives offer good resistance to water, and retain their strength at temperatures between -30F and 75F."
Ideal applications for contact adhesives
Their unique bonding profile makes contact adhesives ideal for use in certain fields and applications. Because unlike most solvent or water-based glues, contact adhesives dry before the surfaces are joined, they can be used in applications where drying is otherwise difficult. Bonding non-porous or semi-porous surfaces like stone or laminate countertops, plywood and flooring, are all areas where contact adhesives excel. Another advantage of contact adhesives is that they can remain unbonded for long periods of time, from hours up to days. This allows them to be used in applications where the large surfaces need to be coated without worry about open-times.
In applications where large areas need to be adhered, but it would be inefficient or cumbersome to do so immediately, contact adhesives can be a solution. Applications like adhering large panels for signs, automotive and truck body or interiors are all places where contact adhesives are regularly used. Finally, because contact adhesives form bonds immediately upon contact, no clamping is necessary in most applications. This can be particularly useful for objects which would be difficult to clamp otherwise, like fabrics or other flexible materials used in footwear or very large pieces.
There are a few inherent disadvantages to contact adhesives. Because their initial tack is so strong, positioning and the joining of two coated surfaces needs to be conducted carefully, since repositioning of pieces can be difficult or impossible. VOCs can be a concern with traditional contact adhesives, since the solvents used evaporate into the air during drying, however, modern water-based or low-VOC formulations are available that meet regulations where applicable.