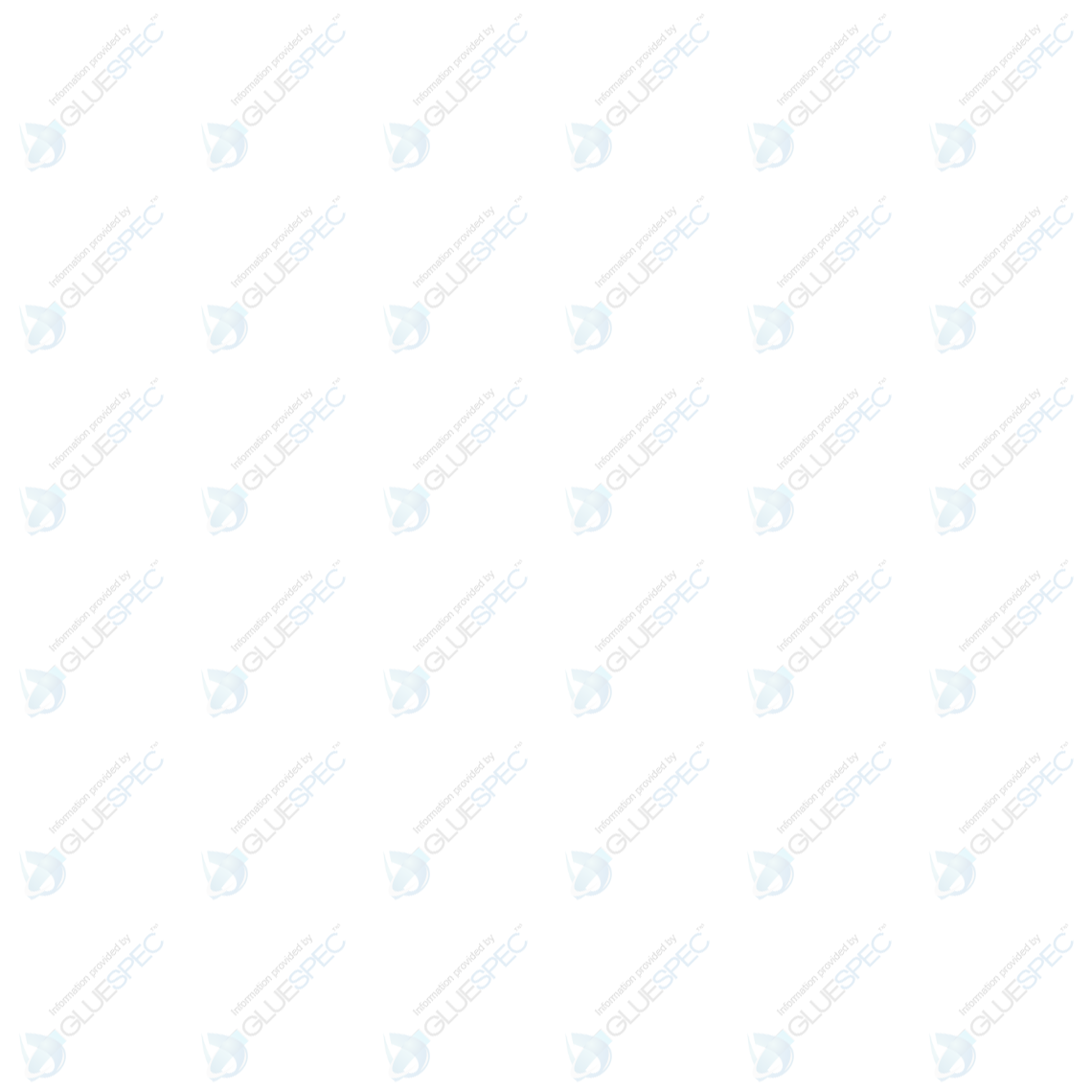
- Contributions by industrial experts with engineers in mind
- Focused on specialty-chemical material applications and selection
Knowledge Center
Cyanoacrylate 202
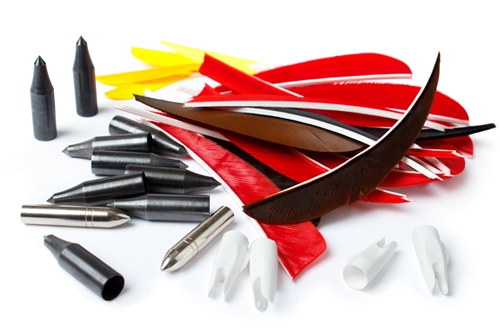
Cyanoacrylate Adhesives (CA Adhesives)
Cyanoacrylate (CA) adhesives provide some of the easiest to use, highest strength, quickest setting bonding in the industry. They're also among the most diverse, with formulations to suit needs from industrial manufacturing to fine woodworking. Subtle changes in chemistry, formulations and activators can suit CA adhesives to nearly any application.
There are a number of ways CA adhesives can be altered to fit different specifications. Chemically, cyanoacrylates can be altered by adding different alkyl groups to the base. Ethyl-, Methyl- and Butyl- 2-Cyanoacrylates are some of the more common, but others are possible. In addition to chemical changes of the base molecule, other additions can be made, such as vinyl aromatic compounds, plasticizers and rubber compounds that alter adhesion, bond strength and flexibility on different surfaces. Viscosity can also be altered by the addition of different compounds to help fill gaps or in other situations where a thin liquid is undesirable.
"With UV-curing technology, CAs can be cured in thicknesses up to .25 inches."
UV Cure meets Cyanoacrylate
CA adhesives can also be made in light-curing formulations. These offer the advantages of both UV-cure adhesives, namely quick cure times, as well as the high bond strength of CAs. These single-part adhesives can be an effective solution to difficulties in manufacturing some medical devices, or any application where cure time is paramount. UVCAs also offer a solution where CAs would be ideal, but a larger than normal gap exists between the pieces to be bonded. With UV-curing technology, CAs can be cured in thicknesses up to .25 inches. This allows for CA glues to be used as a potting compound in some instances. Secondary cure in shadowed parts via moisture is also relatively quick, as with all CAs.
The right glue for the right job
The addition of various compounds can increase adhesion on specific surfaces, or under specific circumstances. Rubber and plastics are generally bonded well by CAs, but formulations specifically for bonding these substances can provide even faster fixture times and stronger bonds. High heat and high impact CAs are available when those conditions are expected in the working life of the bond.
For applications that require flexibility such as weather stripping or bonding urethanes, CAs are available that fit the job. Additionally, CAs have proven effective when used in ballistics, munitions and for attaching fletchings. Mechanical shock and vibration resistant CAs have also been developed for applications where impact resistance is needed, like car assembly and machinery.
A drawback of typical CA glues is that they must be applied thinly for optimal adhesion (less than 1mm). One-part formulations that increase the minimum gap to more than 2mm have been developed as well. These generally take the form of a gel-type adhesive. Two-part CAs that can fill gaps up to 5mm are also manufactured.
"Blooming occurs when vaporized CA contacts moisture in the air and hardens."
The medical use of CA adhesives has been in practice since the 1970s. Cyanoacrylate bonds very well to skin and tissue, making it a quick and effective way to close some wounds. While some CA glues can be irritating to skin, a number of formulations have been approved for medical use. CAs can be used to stop vascular bleeding in some cases and have the advantage of being bacteriostatic.
Battling bloom and blush
One problem with traditional Cyanoacrylates is so-called "bloom," or "blush." This effect occurs when vaporized CA contacts moisture in the air and hardens – falling to the bonding surface and forming a "blooming" effect. This can leave an undesirable residue on the surface residue on the surface. One way to combat this problem is by using a "low bloom" formulated product that is less volatile. These formulations can also be used in situations where concerns about inhalation are paramount.
Surface Primers and Accelerators
CA adhesives cure in the presence of a weak base (like the OH- ions from water). Because of this, their drying time can be inhibited on acidic surfaces. Environments with particularly low humidity can also be problematic for curing. Surface primers can be used to increase adhesion on surfaces that would otherwise be difficult to bond with CA adhesives. These include materials like low-surface energy plastics, and also porous surfaces like ceramics and wood. Primers can be used to increase adhesion on dry or acidic surfaces or surfaces with other contaminants. Surface primers provide ideal conditions for curing and also increase the speed of curing on all surfaces. CA glues can be made in "surface insensitive" formulations, which neutralize those components that would inhibit adhesion without the need for primer application. Accelerators can be used on any surface before or after application to decrease curing times or cure unbonded portions of glue. The choice of accelerator and carrying solvent is usually determined by the substrate so the activator doesn't adversely affect it.