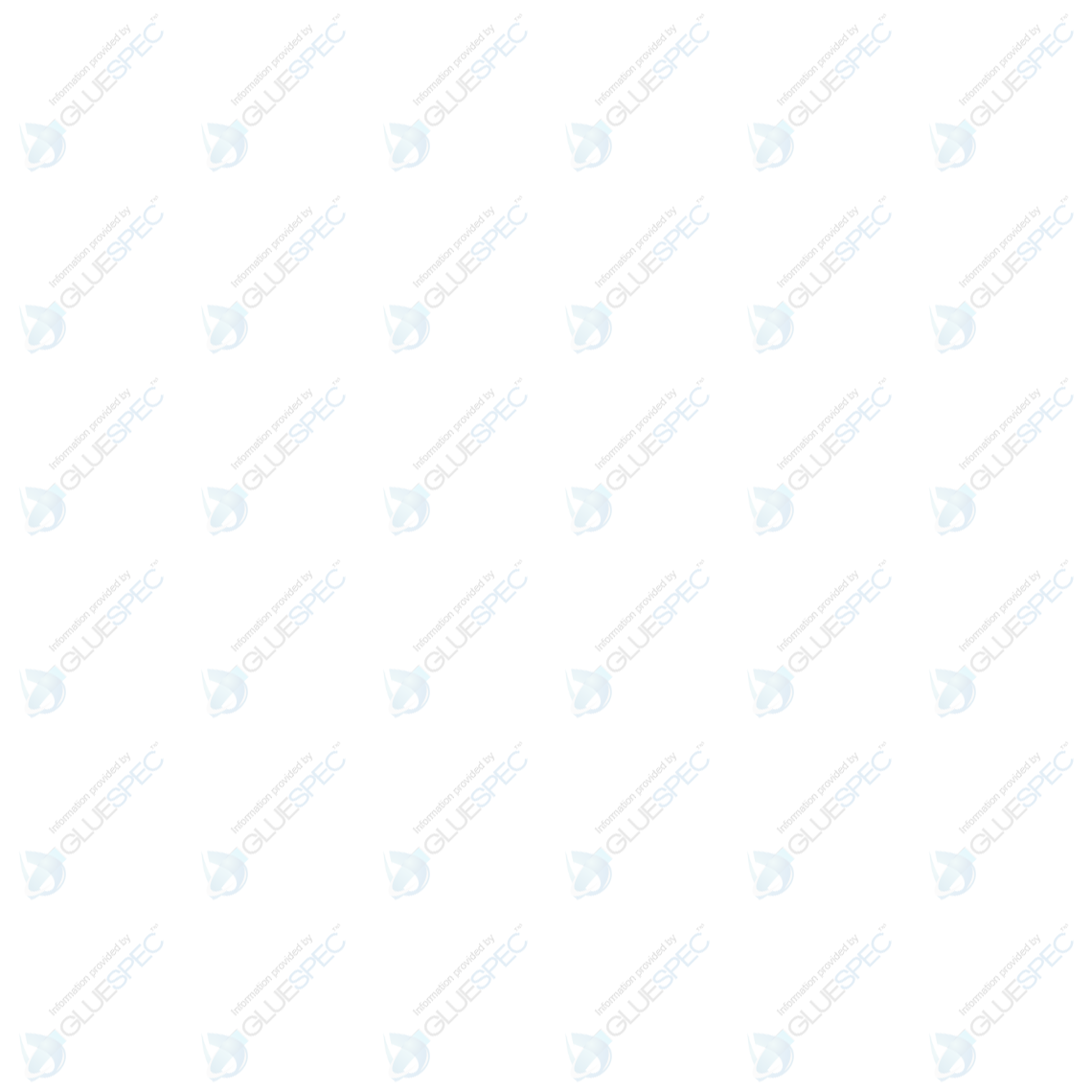
- Contributions by industrial experts with engineers in mind
- Focused on specialty-chemical material applications and selection
Knowledge Center
Electrically Conductive Adhesives Guide
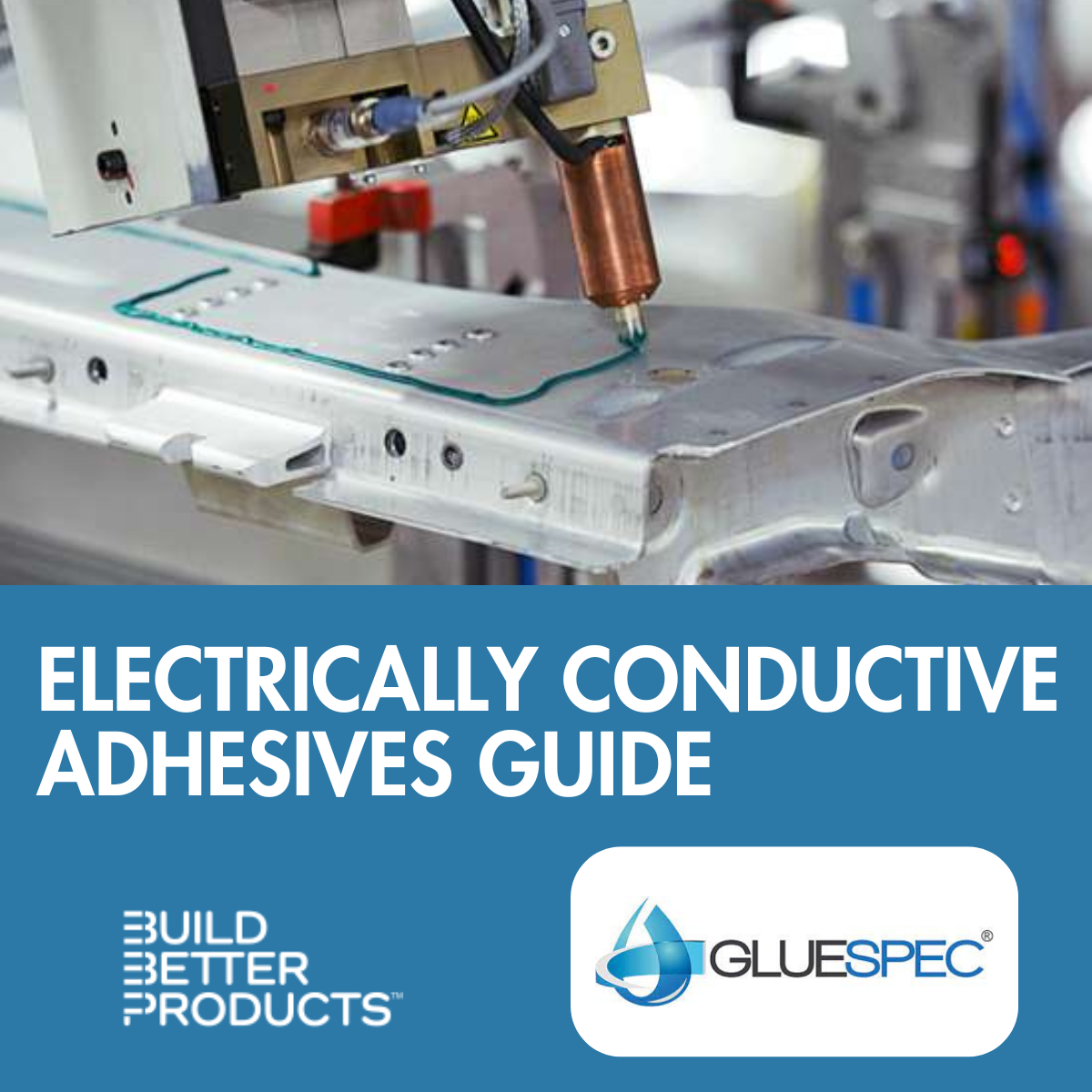
Listen to This Article
Electrically conductive adhesives combine strong, reliable adhesion with electrical conductivity. They consist of a polymer that is filled with metal, metallic, or metal-coated particles.
This guide explains what design engineers need to know about selecting electrically conductive adhesives, a category of products you'll find on Gluespec.
Gluespec’s comprehensive and quality-tested database of 35,000 adhesive materials includes the electrically conductive adhesives that design engineers need.
Along with technical data and key specifications, you’ll find best practices and comparable materials. You can also view test method information on dozens of material properties and data points.
Table of Contents
Types of Electrically Conductive Adhesives
Introduction
Adhesives are made of polymers, materials that are normally electrically insulating. By adding specialized fillers, however, an adhesive can become electrically conductive instead. Different types of fills are used.
Silver fills provide the greatest electrical conductivity; however, silver is relatively expensive. Nickel fills cost less, and nickel still provides good conductivity. Graphite is used for applications where a lower level of electrical conductivity is needed.
Electrically conductive adhesives can also provide shielding against electromagnetic interference (EMI) and radio frequency interference (RFI), or protection against electrostatic discharge (ESD). Silver-filled adhesives provide the highest levels of shielding, followed by nickel-filled products. Graphite fills provide the least EMI/RFI shielding, but they're also used for protection against ESD.
Applications for electrically conductive adhesives include electronics manufacturing for the defense, aerospace, medical, automotive, renewable energy, and consumer electronics industries. Often, these adhesive products are used at the printed circuit board (PCB) level. Some electrically conductive adhesives also container fillers that provide thermal conductivity for heat dissipation.
In these and other applications, the electrical connections and electronic enclosures sometimes use electrically conductive glues and tapes. You can also find these materials on Gluespec. Compared to tapes, glues provide higher structural strength.
Types of Electrically Conductive Adhesives
Gluespec divides electrically conductive adhesives into four categories and makes it easy to search for products online. These categories reflect the base material, the type of cure system, and/or the number of components.
Within each category, you can search for elecrically conductive adhesives based on specifications such as material form, supported substrates, and the amount of electrical conductivity.
The following sections describe the four categories of electrically conductive adhesives. They also provide information about material properties and performance, curing, and general advantages and disadvantages. You’ll also find links to technical resources with additional information, either in the Gluespec Knowledge Center or from other trusted resources.
Epoxy Electrically Conductive Adhesives
Epoxy elecrrically conductive adhesives form tough, high-strength bonds and combine good chemical resistance with excellent environmental resistance. They bond well to similar substrates and can be used with the metal, plastic, glass, and ceramic materials used in electronics.
Epoxies also have good void-filling capabilities and can resist creep under sustained loads. They usually cure at room temperature or with the addition of heat and are available in formulations with a range of cure times.
Unless they are modified, however, epoxy electrically conductive adhesives are hard and brittle after curing. Under stress, this can result in cracking.
One-part epoxies generally require heat to cure. Two-part epoxies began curing after the two materials (A+B) are mixed together. With the latter, optimal curing requires proper mix ratios for best results.
Epoxies that cure at room temperature won’t work well at operating temperatures over 120°C. Therefore, a heat-cured epoxy may be required within an electronic enclosure.
When searching for epoxy electrically conductive adhesives, design engineers can choose pastes or liquids, including solvent-free formulations and thixotropic materials. Consider all of the application conditions and, in the case of a high-temperature environment, the specific temperature range.
Today, 5G electronics are putting more numerous and higher-powered components into smaller spaces. Therefore, high-temperature resistance is becoming increasingly important. Epoxy adhesives have their advantages, but silicones may be needed for these and other high-temperature applications.
Applications
Applications for epoxy electrically conductive adhesives include:
-
Electrical connectors
-
Electronic modules
-
Radar and guidance systems
-
Satellite communications
-
Environments with harsh chemicals
Products
These are some of the epoxy elecrical conductive adhesives you'll find on Gluespec.
![]() |
Loctite Ablestik 56C w/ Cat 11 is a two-part, silver-filled epoxy paste that cures with heat and adheres to aluminum, ceramics, glass, metals, and plastic. |
![]() |
FE7004A+B from H.B. Fuller is a two-part, liquid, electrically conductive epoxy that bonds to most metals and rigid plastics. It features high shear strength. |
![]() |
SEC1233 from Resinlab is a silver-filled, two-part electrically conductive epoxy paste that cures at room temperature and is designed for electronics applications. |
Tech Specs
Here are some of the technical specifications for epoxy electrically conductive adhesives.
Type |
Spec |
Definition |
Cure |
Cure Time (min)
|
The length of time needed for something to fully cure. |
Bond Strength |
General Bond Strength
|
The amount of adhesion between the bonded substrates. It is usually measured in pounds per square inch. |
Hardness |
Elongation % |
The process of becoming or making something become longer and, often, thinner. |
Conductivity |
Electrical Conductivity (mhos/cm) |
A property of materials that determines how well a given material will conduct electricity. |
Resources
Here are some additional resources about epoxy electrically conductive adhesives.
Silicone Electrically Conductive Adhesives
Silicone electrically conductive adhesives resist higher temperatures than epoxy adhesives and provide long-lasting heat resistance without a significant loss in properties.
With their low modulus of elasticity, silicones can also absorb some of the stress that results from the material expansion and contraction that occurs at different rates when electronic substrates (such as glass and plastic) have different coefficients of thermal expansion (CTE). By contrast, epoxies have a higher modulus of elasticity and are less stress-relieving.
Electronics can fail for a variety of reasons, but moisture is one of the most common causes. Silicone adhesives have excellent hydrolytic stability and allow water vapor to pass through, which can help to limit corrosion.
Despite these advantages, silicone adhesives demonstrate poor adhesion to a variety of substrates. They are also less resistant to aggressive fluids than epoxy adhesives and cannot be painted or coated because of their low surface energy.
Silicone electrically conductive adhesives come in one- or two-part formulations and support the use of various curing methods. Evaporative drying occurs at room temperature and does not require the use of ovens; however, it can be time-consuming. Moisture curing uses the moisture in the air to initiate curing. Heat curing applies thermal energy to initiate or accelerate cross-linking. Ultraviolet curing requires irradiation at a specific wavelength and energy intensity. Instead of liquids, pastes, or gels, designers can choose tapes.
Applications
Applications for silicone electrically conductive adhesives include:
- PCB grounding
- Electronic devices
- Electrical connections
- E-mobility solutions
- Microelectronics
Products
These are some of the silicone electrically conductive adhesives you'll find on Gluespec.
![]() |
Dowsil EC-6601 Electrically Conductive Adhesive from Dow is a one-part, liquid silicone adhesive for PCB grounding, electronic devices, and electrical connections. |
![]() |
1535 from H.B. Fuller is a one-part, silicone adhesive sealant that cures with moisture and provides both electrical and thermal conductivity. |
![]() |
Cho-Bond 1077 from Parker Chomerics is a one-part, silicone paste filled with nickel-aluminum particles that provides EMI shielding. |
Tech Specs
Here are some of the technical specifications for silicone electrically conductive adhesives.
Type |
Spec |
Definition |
Cure |
Viscosity (cPs) |
A measure of a fluid’s resistance to flow. |
Bond Strength |
Shear Strength (psi) |
A material’s ability to resist forces that cause the material’s internal structure to slide against itself. |
Hardness |
Flexibility |
The ability to bend easily without breaking |
Conductivity |
Volume Resistivity (ohms-cm) |
The ratio of electrical resistance through a cross-section divided by length through which current flows. |
Resources
Here are some additional resources about silicone electrically conductive adhesives.
- What are Silicone Adhesives and Sealants?
- Why Use a Silicone Adhesive?
- Electronics: Silicone Adhesives and Sealants
- Conductive Silicones: Electrically Conductive vs. Thermally Conductive
Heat Cure Adhesives
Heat cure adhesives use applied heat, typically from an oven, to initiate or accelerate the chemical crosslinking of the polymer. Because heat curing requires the entire assembly to reach the prescribed cure temperature before the cure time starts, significant time and energy are required.
Cure temperatures and durations vary, but some heat cure adhesives now offer rapid curing at higher temperatures for faster throughputs. There are also dual cure adhesives where heat curing is optional.
The benefits of heat curing include greater bond strength and toughness. Heat curing also increases hardness, rigidity, impact resistance, and chemical resistance.
Although heat curing improves wetting and lowers viscosity, it is important to consider that high temperatures can damage some electronic components. Heat curing may be used alone or in conjunction with another curing mechanism to accelerate curing.
Electrically conductive heat cure adhesives have epoxy or silicone chemistries and can be solvent-free or solvent-based. There are also halogen-free formulations and products that contain volatile content.
Both one-part and two-part products are available. During adhesive selection, design engineers can specify both the cure time and the cure temperature, as well as properties such as bond strength and material resistance.
Applications
Applications for heat cure adhesives include:
- Radar systems
- Satellite communications
- Guidance systems
- Electrical connections
- Electronics equipment
Products
These are some of the heat cure adhesives you'll find on Gluespec.
![]() |
Loctite Ablestik CT 5047-2 from Henkel is a two-part, liquid epoxy that is filled with silver and cures with heat. It bonds well to aluminum. |
![]() |
9703 from 3M is an electrically conductive adhesive transfer tape with acrylic chemistry that cures with heat. It bonds well to many common PCB substrates. |
![]() |
TF E2213F from Resin Designs is a one-part, B-staged epoxy film that is filled with silver particles. It provides EMI/RFI shielding and had good heat resistance. |
Tech Specs
Here are some of the technical specifications for heat cure adhesives.
Type |
Spec |
Definition |
Cure |
Work / Pot Time |
Pot life is the length of time in which multiple part coatings or paints can be applied to a surface |
Thixotrophic |
A thixotrophic fluid is one that takes a fixed time to return to its equilibrium viscosity when subjected to abrupt changes in shear rate |
|
Other Properties
|
General Bond Strength |
The amount of adhesion between the bonded substrates. It is usually measured in pounds per square inch. |
Outgassing |
Outgassing, sometimes called offgassing, is the emission of occluded gases from a material by vacuum, heat, or pressure. |
Resources
Here are some additional resources about heat cure adhesives.
- Heat Cure Adhesives, Sealants, and Coatings
- Adhesive Academy: Heat Curing 101
- Heat Cure Epoxy: Making Sure the Adhesive is Properly Cured
Two-Component Adhesives
For many electronic applications, two-component (A/B) adhesives are used. Often, they are used for high-stress applications where there are significant temperature changes, vibrations, or mechanical shock. This makes them a good choice for electronic devices.
With two-component adhesives, a resin and a hardener are mixed together. The hardener triggers polymerization, the joining of monomer molecules to create polymer chains. In turn, this bonding reaction increases the adhesive’s strength.
Although two-component adhesives support mechanical and dosing and mixing, they can also be applied using double-chamber or side-by-side cartridges. There is a specific mixing ratio, such as 1:1 or 10:1, that must be followed.
Unlike one-part adhesives, two-component products cure when they are combined. In other words, they generally do not require moisture, heat, or light.
Among their advanages, two-part adhesives provide high bond strength andthe ability to adhere to a wide variety of substrates.
Unlike one-component adhesives, two-component systems can’t be used straight from the drum, pail, or tube. They require careful metering and mixing, and sometimes a catalyst is needed to speed the reaction between the resin and the hardener.
Two-component systems may also require degassing, the removal of a gas from a solid or a liquid. Despite their disadvantages, two-component adhesives remain an attractive option because they tend to impart better physical properties.
Applications
Applications for two-component adhesives include:
- Conductive plastics
- Radar and satellites
- Guidance systems
- Sporting equipment
- Military electronics
Products
These are some of the products you'll find on Gluespec.
![]() |
Loctite Ablestik 56C w/ Cat 11 is a two-part, silver-filled epoxy paste that cures with heat and adheres to aluminum, ceramics, glass, metals, and plastic. |
![]() |
FE7004A+B from H.B. Fuller is a two-part, liquid, electrically conductive epoxy that bonds to most metals and rigid plastics. It features high shear strength and resists water. |
![]() |
SEC1233 from Resinlab is a silver-filled, two-part electrically conductive epoxy paste that cures at room temperature and is designed for electronics applications. |
Tech Specs
Here are some the technical specifications for two-component adhesives.
Type |
Spec |
Definition |
Cure |
Linear Shrinkage (%) |
Escape of volatile substances or chemical changes that result in volume decrease or contraction of a material. The amount of dimensional change during the cure process. |
Work/Pot Time (min) |
The length of time in which multiple part coatings or paints can be applied to a surface. |
|
Bond Strength |
Peel Strength (piw) |
A measure of the adhesive strength of two or more materials that have been bonded together. The ability to resist that cause the material’s |
Other Properties |
Specific Gravity |
The ratio of the density of a substance to the density of some substance (such as pure water) taken as a standard when both densities are obtained by weighing in air. |
Resources
Here are some additional resources about two-component adhesives.
- Curing Two Part Silicones? These Tips are for You
- Electrically Conductive Adhesives Q&A
- Electrically Conductive Adhesives
Gluespec is Your Source for Electrically Conductive Adhesives
Gluespec’s comprehensive and quality-tested database of 35,000 adhesive materials includes the electrically conductive adhesives that design engineers need. The materials and manufacturers in our database are not limited to specific suppliers, and data is quality-checked and updated as needed whenever new data sheets or product specifications are released.
If you need deep data on electrically conductive adhesives or other materials, you’ll find what you’re looking for in our proprietary adhesives database. Along with technical data and key specifications, you’ll find best practices and comparable materials. Design engineers can also view test method information on dozens of material properties and data points.
Finally, Gluespec’s Advanced Search provides the tools you need to conduct deep filtering among all material properties. The result is a customized grid that contains materials and data points that are specific to your project. Save custom grids for quick access and share them, along with this Electrically Conductive Adhesives Guide, with your colleagues.