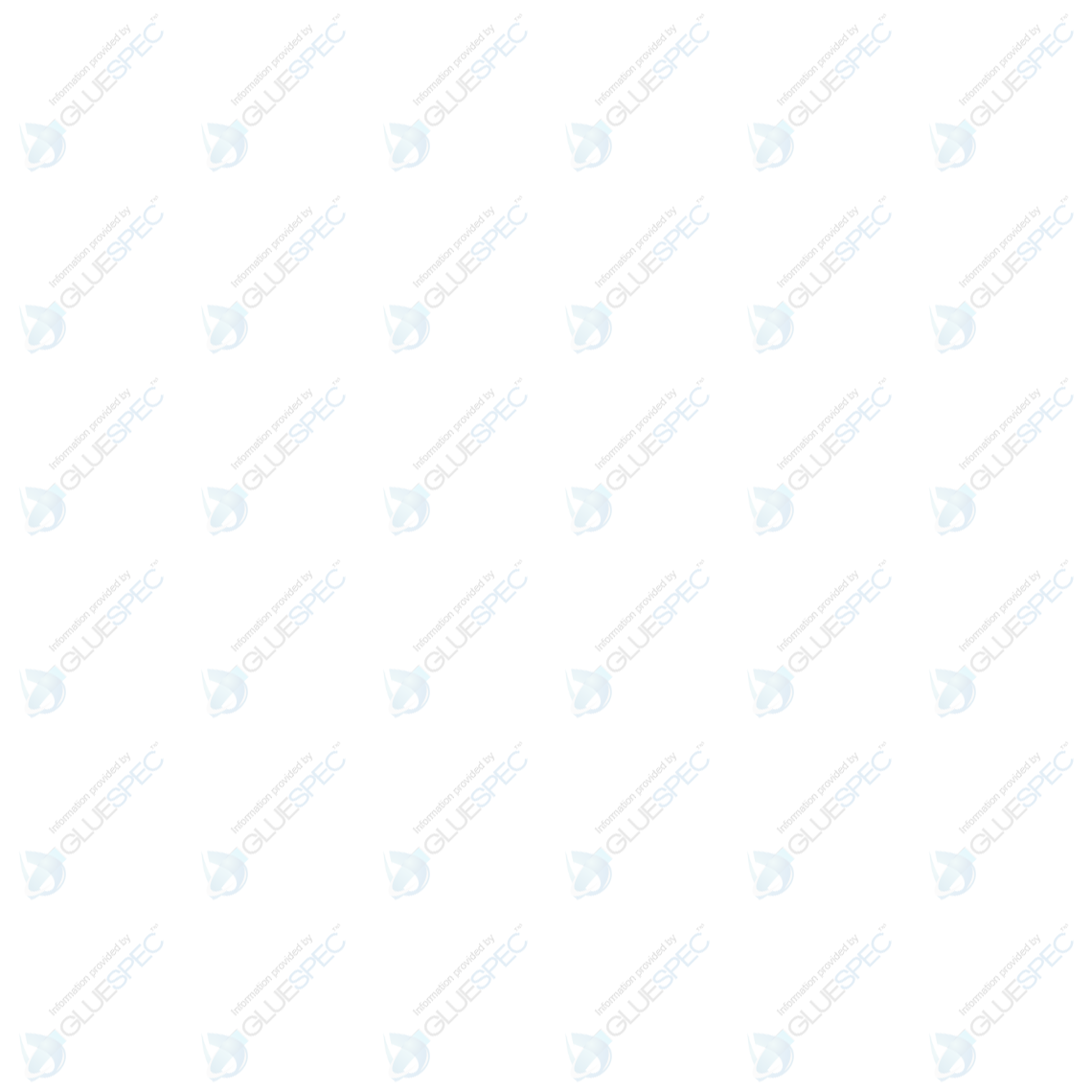
- Contributions by industrial experts with engineers in mind
- Focused on specialty-chemical material applications and selection
Knowledge Center
Electronic Component Adhesives Guide
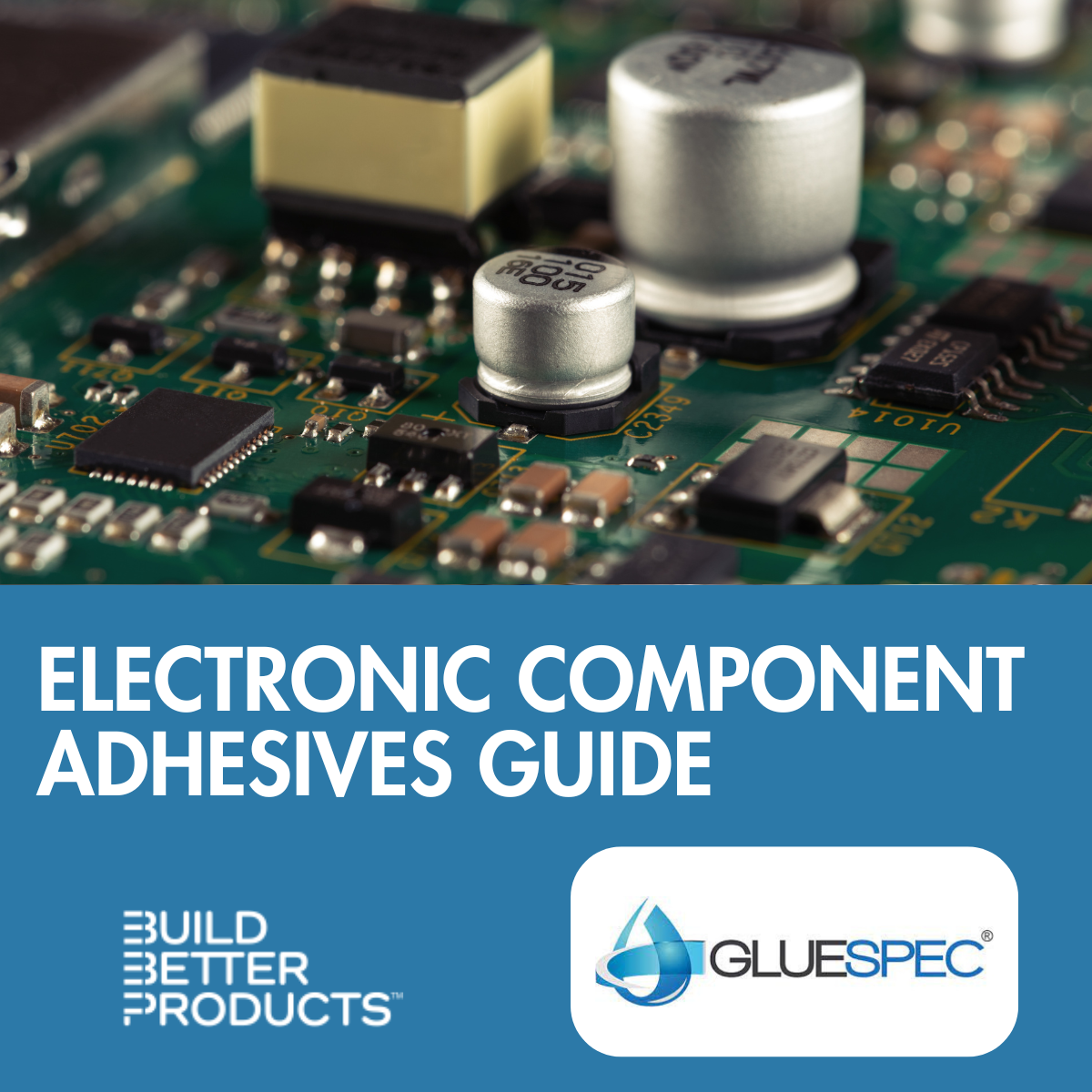
Listen to This Article
Electronic component adhesives bond discrete devices to substrates. Typically, they are used for surface-mounting parts to printed circuit boards (PCBs). Yet they’re also used for potting and encapsulation, substrate assembly, and electronic repairs.
This guide explains what design engineers need to know about selecting electronic component adhesives, a category of products you'll find on Gluespec.
Gluespec’s comprehensive and quality-tested database of 35,000 adhesive materials includes the electronic component adhesives that design engineers need. Along with technical data and key specifications, you’ll find best practices and comparable materials. You can also view test method information on dozens of material properties and data points.
Table of Contents
Types of Electronic Component Adhesives
Printed Circuit Board (PCB) Adhesives
Introduction
Electronic component adhesives are used in place of soldering or in conjunction with it. Regardless, they must bond parts securely. Some electronic component adhesives are electrically insulating and others are electrically conductive. Similarly, some products are thermally insulating while others are thermally conductive.
In addition to thermal and electrical performance, design engineers need to consider the materials to bond, the environmental conditions, and any application-specific requirements. For example, electronic component adhesives that are used outdoors may need to resist sunlight.
Adhesive chemistry plays an important role in product selection. Epoxies offer excellent bond strength and chemical resistance. Silicones combine flexibility with excellent high-temperature resistance. Acrylics resist vibrations and thermal cycling. Polyurethanes provide strong and flexible bonds.
For each of these chemistries, one-part and two-part products are available. Curing can occur with light, heat, at room temperature, or in a dual curing process. Products that support automated metering and dispensing can be applied with greater speed and precision.
Types of Electronic Components Adhesives
Gluespec divides electronic component adhesives into eight categories and makes it easy to search for products online. These are the categories:
• Printed Circuit Boards (PCBs)
• Coils
• Sensors
Within each category, you can search for products based on technical specifications for curing, bond strength, material resistance, conductivity, and other properties. The following sections describe each category of electronic component adhesives in detail. You’ll also find links to technical resources with additional information, either in the Gluespec Knowledge Center or from other trusted resources.
Printed Circuit Board (PCB) Adhesives
PCB adhesives are used in the assembly of printed circuit boards. They bond surface-mounted components such as resistors, capacitors, and integrated circuits (ICs) to PCBs, which are made of materials such as metal, plastics, ceramics, or glass. Often, PCB adhesives need to bond dissimilar materials together. For example, an adhesive may need to bond an aluminum electrolytic capacitor to a polyimide or FR-4 substrate.
Some PCB adhesives are filled with metal or metal-coated particles that provide electrical conductivity and EMI shielding. For high-temperature applications, design engineers can choose thermally-conductive PCB adhesives that dissipate heat instead. There are also PCB adhesives that are both thermally and electrically conductive.
Other products include staking adhesives that support component leads and withstand vibrations. They can replace mechanical attachments such as fasteners and support lightweighting initiatives.
Applications
Applications for PCB adhesives include:
• Bonding surface-mounted devices (SMDs) to PCBs
• Staking component leads
• Replacing solder or mechanical fasteners
• Electrical conductivity
• Thermal management
Products
These are some of the PCB adhesives you'll find on Gluespec.
![]() |
Loctite Ablestick 56C w/ Cat 11 from Henkel is a two-part, silver-filled epoxy paste that cures with heat. |
![]() |
TF E2213F from Resin Designs is a one-part, electrically conductive epoxy that cures with heat and is provided as a B-staged film. |
![]() |
FE7004A+B from H.B. Fuller is two-part, liquid epoxy that cures at room temperature but supports accelerate heat curing. |
Tech Specs
Here are some of the technical specifications for PCB adhesives.
Type |
Spec |
Definition |
Cure |
Viscosity (cPs)
|
A measure of a fluid’s resistance to flow. |
Bond Strength |
Shear Strength (psi)
|
The ability of a material to resist forces that cause the material’s internal structure to slide against itself. |
Conductivity |
Dissipation Factor |
A measure of loss-rate of energy of a mode of oscillation (mechanical, electrical, or electromechanical) in a dissipative system |
Other Properties |
Specific Gravity |
The ratio of the density of a substance to the density of some substance (such as pure water) taken as a standard when both densities are obtained by weighing in air |
Resources
Here are some additional resources about PCB adhesives.
- PCB Protection Q&A
- Printed Circuit Board Assembly Materials
- How to Stake Electronic Components Using Adhesives
Amplifier Adhesives
Amplifier adhesives bond various types amplifiers to printed circuit boards. For design engineers, it's important to determine which type of amplifier you need to bond. There are several main types.
Voltage amplifiers increase the output voltage of the signal.
Current amplifiers increase the amplitude of the input current compared to the input current waveform.
Power amplifiers include audio, radio frequency (RF) and direct current (DC) devices that carry Class A, B, AB, or C designations.
Operational amplifiers and instrumentation amplifiers also use electronic component adhesives during PCB assembly (PCBA).
Environmental resistance is also a key specification. Amplifier adhesives can withstand specific temperature ranges and may resist dust and moisture. Some products are electrically insulating and have UL 94 flame ratings. Chemistries, cure methods, and colors vary. Products come in one-part or two-part (A/B) forms and include solvent-free formulations for greater environmental sustainability.
Applications
Applications for amplifier adhesives include:
- Bonding amplifiers to PCBs
- Providing electrical conductivity or insulation
- Protection against the application environment
Products
These are some of the amplifier adhesives you'll find on Gluespec.
![]() |
Sylgard 184 Silicone Elastomer from Dow is a two-part, liquid silicone that is solvent-free. It cures at room temperature or with accelerated heat curing. |
![]() |
Micro-Faze 3A4 from AOS Thermal Compounds is a thermal interface film that is formulated with a non-silicone thermal grease. It can be die cut into pads. |
![]() |
Electro-Wash PX from Chemtronics (ITW) is a one-part product that is available as either an aerosol or as a liquid. It's clear, colorless, and free of CFCs and HFCs. |
Tech Specs
Here are some of the technical specifications for amplifier adhesives.
Type |
Spec |
Definition |
Cure |
Linear Shrinkage (%)
|
Escape of volatile substances or chemical changes that result in volume decrease or contraction of a material. The amount of dimensional change during the cure process. |
Material Resistance |
Ozone Resistance
|
The ability of a material to resist the deteriorating effects of ozone exposure |
Conductivity |
Dielectric Strength (V/mil) |
The electrical strength of an insulating material |
Other Properties |
Light Refractive Index (RI) |
A value calculated from the ratio of the speed of light in a vacuum to that in a second medium of greater density |
Resources
Here are some additional resources about amplifier adhesives.
Chip on Board Adhesives
Chip on board (COB) adhesives bond ICs such as microprocessors directly to PCBs. By eliminating the individual packaging of semiconductor devices, COB technology supports smaller, less expensive, and lighter weight footprints.
When selecting chip on board adhesives, design engineers need to consider both the substrate and component materials. Some adhesives support dissimilar substrates made of polyimide (Kapton®), glass, metal, ceramic, epoxy board, or PET plastic.
Glob-top, a conformal coating variant that’s used in COB assembly, deposits a specially-formulated epoxy or a resin over a semiconductor chip and its wire bonds, providing mechanical support and excluding contaminants such as dust and moisture.
Although epoxy chemistries are common in glob-top products, acrylated urethane is also used. For chip on flex (COF) applications with flexible circuits, design engineers may need adhesives that are softer and can resist cracking.
Applications
Applications for chip on board adhesives include:
- Bonding ICs directly to PCBs
- Eliminating individual packaging of semiconductor devices
- Greater flexibility for flex circuits
Products
These are some of the COB adhesives you'll find on Gluespec.
![]() |
E-Max 10024 from Dymax is a one-part liquid encapsulant with a modified urethane chemistry. It's clear in color and cures with UV/visible light. |
![]() |
EO1059R from Henkel is a one-part liquid epoxy that is designed to cure in less than five minutes at 140°C. It bonds well to plastic substrates. |
![]() |
KER-6150 A/B from Shinetsu is a two-part liquid encapsulant with a phenyl-based silicone chemistry. It supports heat curing and additional curing. |
Tech Specs
Here are some of the technical specifications for chip on board adhesives.
Type |
Spec |
Definition |
Cure |
Cure Time (min)
|
The length of time needed for something to fully cure |
Material Resistance |
Moisture Resistance
|
The ability of a material to resist the deteriorating effects of moisture |
Conductivity |
Dielectric Constant |
The ratio of an insulator’s capacitance to that of dry air. A dielectric constant of 10 means the insulator will absorb 10x more electrical energy than air |
Other Properties |
Flash Point (°F) |
The lowest temperature at which vapors above a volatile combustible substance ignite in air when exposed to flame. |
Resources
Here are some additional resources about chip on board adhesives.
- Chip-on-Board (COB)
- Chip-on-Flex (COF)
- The Influence of Adhesive Materials on Chip-on-Board Packaging of MEMS Devices
Coil Adhesives
Coil adhesives bond and secure electric or electromagnetic coils to substrates. Coils are electronic components that can store and transfer electrical energy or create electromagnetic fields for solenoids.
Because most coils are made of solid copper wire, design engineers may need adhesives that provide strain relief to prevent connections from breaking. Silicone adhesives applied to the backs of connector shells can improve reliability and are non-corrosive.
Coil adhesives support a variety of dispensing methods and can be applied by machine or by hand. They cure quickly for shorter cycle times and are generally free of solvents for reduced levels of volatile organic compounds (VOCs).
In addition, coil adhesives can adhere to a variety of PCB substrates. Hot melt adhesives, or hot glues, are supplied as a solid and liquefy when heated to a temperature above their softening point. Gel adhesives are also available.
Applications
Applications for coil adhesives include:
- Bonding electric coils for power supplies and inverters
- Bonding electromagnetic coils for electric motors or generators
- Providing strain relief
Products
These are some of the products you'll find on Gluespec.
![]() |
3748 from 3M is a hot melt adhesive that bonds polyolefins and is non-corrosive to copper. It is off-white in color and has good thermal shock resistance. |
![]() |
Loctite 382 from Henkel is a fast-curing gel that for tacking electronic components. It has a cyanoacrylate chemistry and cures with the humidity in the air. |
![]() |
320/322 from Parker Lord is a two-part, non-flammable epoxy adhesive that is solvent-free. It supports room temperature curing and oven curing. |
Tech Specs
Here are some the technical specifications for coil adhesives like 3M 3748.
Type |
Spec |
Definition |
Cure |
Application Temperature (°F)
|
The temperature at the point the adhesive is applied |
Bond Strength |
Peel Strength (piw)
|
A measure of the adhesive strength of two or more materials that have been bonded together |
Conductivity |
Volume Resistivity (O) |
The ratio of electrical resistance through a cross-section divided by length through which current flows (ohms-cm) |
Other Properties |
% Solids (%) |
The percentage by weight of the nonvolatile matter in an adhesive |
Resources
Here are some additional resources about coil adhesives.
- Adhesives for Electric Motors and Coils
- High-Temperature Epoxy Adhesive for Coils
- Assembling EV Motors with Adhesive
Connector Adhesives
Connector adhesives provide a supplemental bond between PCB connectors and printed circuit boards. Male PCB connectors, or pin headers, attach to PCBs with pins. Female connectors, or sockets, have leads instead.
Electronics manufacturers can solder pins and leads in place, but these connections sometimes fail during shipping or while in use. Connector adhesives provide another means of attachment to the PCB and can encapsulate the interconnect to provide protection against contaminants and vibrations.
To encapsulate the PCB interconnect, a large dot or drop of adhesive is poured over the connector and flows downward, covering the connector and bonding it to the printed circuit board. Design engineers need to consider the size of the dot to apply, the number of dots per board, the maximum temperature for the application, and the materials of construction for both the printed circuit and the PCB connector.
Hot melt adhesives can be used, but epoxy resins and polyurethane potting compounds can provide medium to low viscosity and penetrate tight spaces on crowded boards.
Applications
Applications for connector adhesives include:
- Bonding male connectors (pin headers)
- Bonding female connectors (sockets)
- Encapsulating PCB interconnects
Products
These are some of the products you'll find on Gluespec.
![]() |
EN-4 w/ EN-7 from Elantas is a two-part liquid polyurethane that cures at room or elevated temperature. It provides arc, fungus, and thermal shock resistance. |
![]() |
GT-1600 Sealing Strip from Resin Designs is a one-part, pre-cured silicone gel that forms an environmental barrier in hot or cold temperatures. It's flame-resistant. |
![]() |
Sylgard 170 Silicone Elastomer from Dow is a two-part liquid silicone with good flowability, a long working time, and flame resistance. It's solvent-free. |
Tech Specs
Here are some the technical specifications for connector adhesives like Elantas (Altana) EN-4 w/ EN-7.
Type |
Spec |
Definition |
Cure |
Work / Pot Time (min) |
The length of time in which multiple part coatings or paints can be applied to a surface |
Bond Strength |
General Bond Strength (psi) |
The amount of adhesion between the bonded substrates usually measured in pounds pers square inch |
Material Resistance |
Fungus Resistance |
Fungus resistance tests are used to determine the reaction of adhesives to several species of fungi under high humidity and a warm environment in the presence of inorganic salts |
Conductivity |
Surface Resistivity (O) |
The resistance experienced by the leakage of current along the surface of the coat/insulating material |
Resources
Here are some additional resources about connector adhesives.
- Switch and Connector Potting and Encapsulating Resins
- Electrical Connector Potting or Overmolding with Hot Melt
- Find the Right Chemistry to Protect PCB Components
Ruggedizing Adhesives
Ruggedizing adhesives combine strong, reliable bonds with protection against exposure to tough conditions such as temperature extremes, salt spray, water, thermal shock, mechanical shock, vibrations, abrasion, and drop testing. For example, military electronics such as radios may need to withstand desert heat, arctic cold, marine environments, and rough handling and storage. 5G and power electronics are subjected to high heat and thermal cycling.
When selecting ruggedizing adhesives, design engineers must also consider factors such as excess heat, airflow, electromagnetic interference (EMI), and electrostatic discharge (ESD). With liquid crystal displays (LCDs) and light emitting diodes (LEDs), ruggedizing adhesives that are clear, transparent, or optically clear may be needed. For outdoor applications, non-yellowing adhesives that provide resistance to ultraviolet light (UV) can support long life. Often, ruggedizing adhesives are used as encapsulants.
Applications
Applications for ruggedizing adhesives include:
- Ruggedizing LCD displays
- Encapsulating LED diodes
- Protecting PCB substrates
Products
These are some of the ruggedizing adhesives you'll find on Gluespec.
![]() |
9641-LV from Dymax is a one-part acrylated urethane liquid that cures with UV/visible light and forms invisible bonds. It resists yellowing and is solvent-free. |
![]() |
KE-109E A/B from Shinetsu is a two-part, optically clear, liquid silicone that supports heat or addition curing. It's durable and self-leveling. |
![]() |
React 767 from Hernon is a one-part liquid acrylic for securing ceramic permanent magnet segments in motor magnet bonding. It has good gap filling properties. |
Tech Specs
Here are some the technical specifications for ruggedizing adhesives.
Type |
Spec |
Definition |
Cure Specs |
Mix Ratio |
The ratio between the resin and the catalyst needed to achieve the listed properties for the adhesive |
Hardness |
Durability |
The ability of a physical product to remain functional, without requiring excessive maintenance or repair, when faced with the challenges of normal operation over its design lifetime |
Elongation (%) |
The process of becoming or making something become longer, and often thinner |
|
Flexibility |
The ability to bend easily without breaking |
Resources
Here are some additional resources about ruggedizing adhesives.
- Ruggedization of Portable Electronics
- Ruggedizing Electronics Requires Special Attention
- Ruggedization Design for Mil Applications
- Staking Materials and Properties
Sensor Adhesives
Sensor adhesives are used in applications ranging from automotive electronics to medical wearables. They provide durable connections to substrates, support efficient assembly, and resist environmental degradation.
Because sensors measure physical quantities such as temperature and pressure or dynamic characteristics such as acceleration and rotation, sensor adhesives need to support accurate measurements. For example, a temperature sensor that is near a heat-generating processor may require a thermally conductive adhesive to dissipate heat that could affect external temperature readings.
Many sensor adhesives use epoxy or silicone chemistries. Glob tops and potting compounds can encapsulate sensors and provide protection against chemicals, corrosions, and contaminants.
Although most sensor adhesives are used with printed circuit boards, sensors are also used with non-conventional substrates such as woven textiles. Biocompatible adhesives that provide a protective interface between instruments and tissues may be required for medical applications.
Applications
Applications for sensor adhesives include:
- Bonding sensors to PCBs
- Bonding sensors to non-conventional substrates
- Dissipating heat and providing environmental protection
Products
These are some of the products you'll find on Gluespec.
![]() |
Loctite Stycast 5954 from Henkel is a two-part, heat-cured silicone that's used for potting and encapsulation. It resist high temperatures up to 500°F. |
![]() |
Slygard 160 Silicone Elastomer from Dow is a two-part, liquid silicone that supports deep section curing. It is flexible, repairable, and free of solvents. |
![]() |
DP270 from 3M is a two-part, low viscosity epoxy resin that is clear or black in color. It has good thermal shock resistance. |
Tech Specs
Here are some the technical specifications for sensor adhesives like Henkel Loctite Stycast A 316-48.
Type |
Spec |
Definition |
Cure |
Cure Temperature (°F) |
The temperature to which an adhesive must be subject in order to ensure that it will cure satisfactorily |
Conductivity |
Non-conductive |
A substance that does not conduct heat, sound, or electricity |
Other Properties |
Glass Transition Temp (Tg) (°F) |
The temperature at which an amorphous polymer changes from a hard/glassy state to a soft/leathery state, or vice versa |
Coefficient of Thermal Expansion (CTE) |
A material property that is indicative of the extent to which a material expands upon heating |
Resources
Here are some additional resources about sensor adhesives.
- Simplifying Sensor Fabrication with Adhesive Compounds
- Guide to Adhesively Mounting Accelerometers
- Adhesives for Sensor Applications
Wire Tacking Adhesives
Wire tacking adhesives are used to secure metal wires to PCB surfaces, typically when vibration is an issue. By holding electrical connections in place, wire-tacking adhesives prevent wires from moving or becoming damaged during the operation or transportation of electronic devices.
In addition to supporting proper wire management, wire tacking glues, as they are sometimes called, help to prevent problems such as wire fatigue and short circuits, both of which can reduce device life.
Wire tacking adhesives can also be used if a wire-related design flaw is discovered during testing, and the engineer can simply address the issue with the use of an adhesive product. In addition, wire tacking adhesives can be used to fix damaged boards and to address the consequences of improper PCB assembly.
Acrylic, cyanoacrylate, and epoxy adhesives are used commonly to attach wires to PCBs; however, cyanoacrylates are especially popular for electronic repairs because they are quick-setting.
Applications
Applications for wire tracking adhesives include:
- PCB repair
- Wire management
- Vibration control
Products
These are some of the wire tacking adhesives you'll find on Gluespec.
![]() |
Light Weld 912-A from Dymax is a one-part, liquid urethane that cures with UV light. It fully complies with RoHS 2015/863/EU. |
![]() |
Loctite 382 from Henkel is a one-part cyanoacrylate gel that has a high viscosity and cures quickly with humidity. |
![]() |
200 from Permabond is a one-part, liquid cyanoacrylate with high viscosity and good flow control. It resists motor oil. |
Tech Specs
Here are some the technical specifications for wire tacking adhesives like Dymax Multi-Cure 9-911-REV-B.
Type |
Spec |
Definition |
Cure Specs |
Fluorescent |
A surface, substance, or color has a very bright appearance when light is directed onto it, as if it is actually shining itself |
Bond Strength |
Tensile Strength |
The maximum stress that a material can withstand while being stretched or pulled before breaking |
Hardness |
Shore D Hardness |
The hardness of hard rubbers, semi-rigid plastics, and hard plastics according to the Shore D Hardness test |
Other Properties |
Density |
Density is the adhesive’s mass per unit of volume. Low density formulations provide increased hardness and stiffness. |
Resources
Here are some additional resources about wire tacking adhesives.
Gluespec is Your Source for Electronic Component Adhesives
Gluespec’s comprehensive and quality-tested database of 35,000 adhesive materials includes the electronic component adhesives that design engineers need. The materials and manufacturers in our database are not limited to specific suppliers, and data is quality-checked and updated as needed whenever new data sheets or product specifications are released.
If you need deep data on electronic component adhesives or other materials, you’ll find what you’re looking for in our proprietary adhesives database. Along with technical data and key specifications, you’ll find best practices and comparable materials. Design engineers can also view test method information on dozens of material properties and data points.
Finally, Gluespec’s Advanced Search provides the tools you need to conduct deep filtering among all material properties. The result is a customized grid that contains materials and data points that are specific to your project. Save custom grids for quick access and share them, along with this Electronic Component Adhesives Guide, with your colleagues.