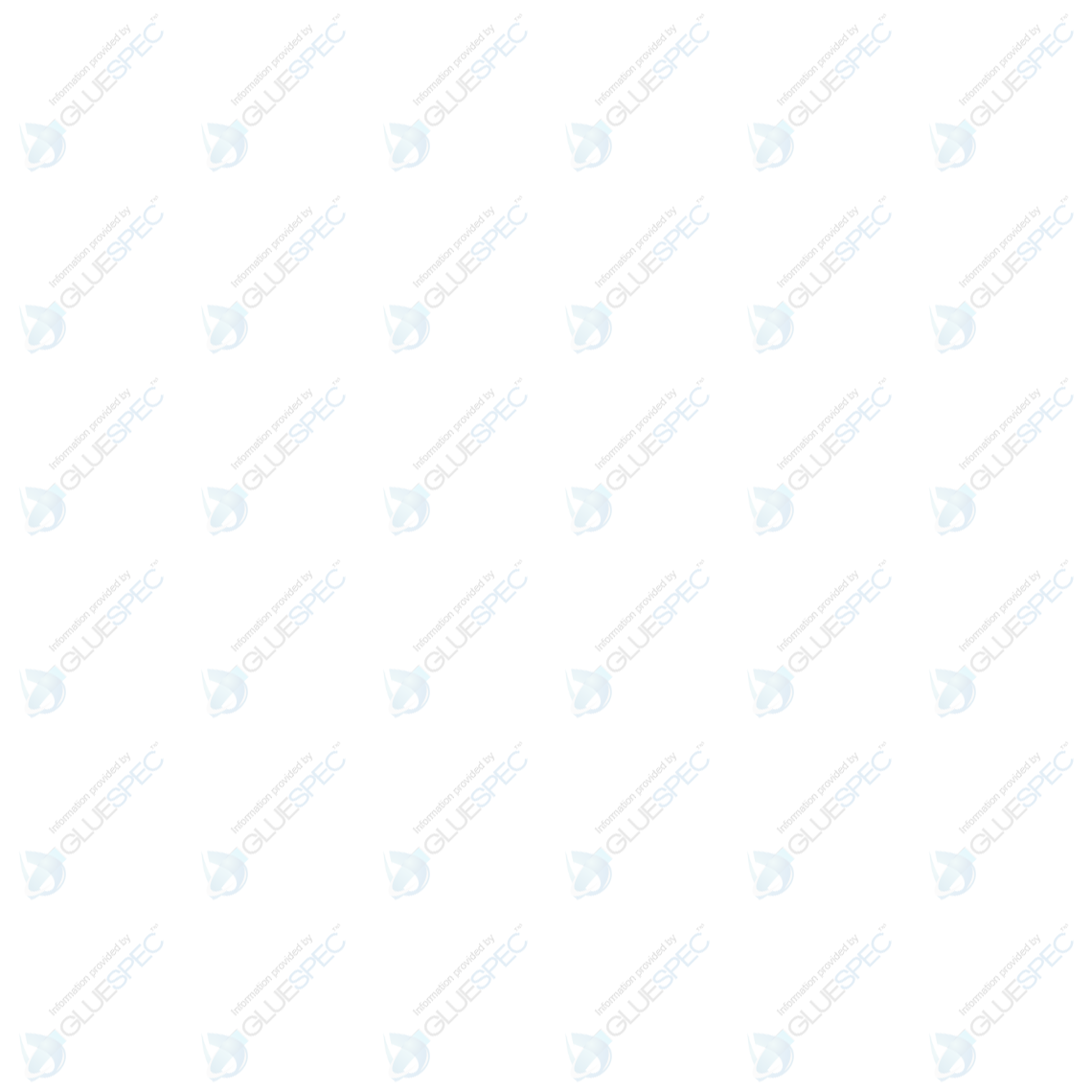
- Contributions by industrial experts with engineers in mind
- Focused on specialty-chemical material applications and selection
Knowledge Center
Fireproofing EV Batteries
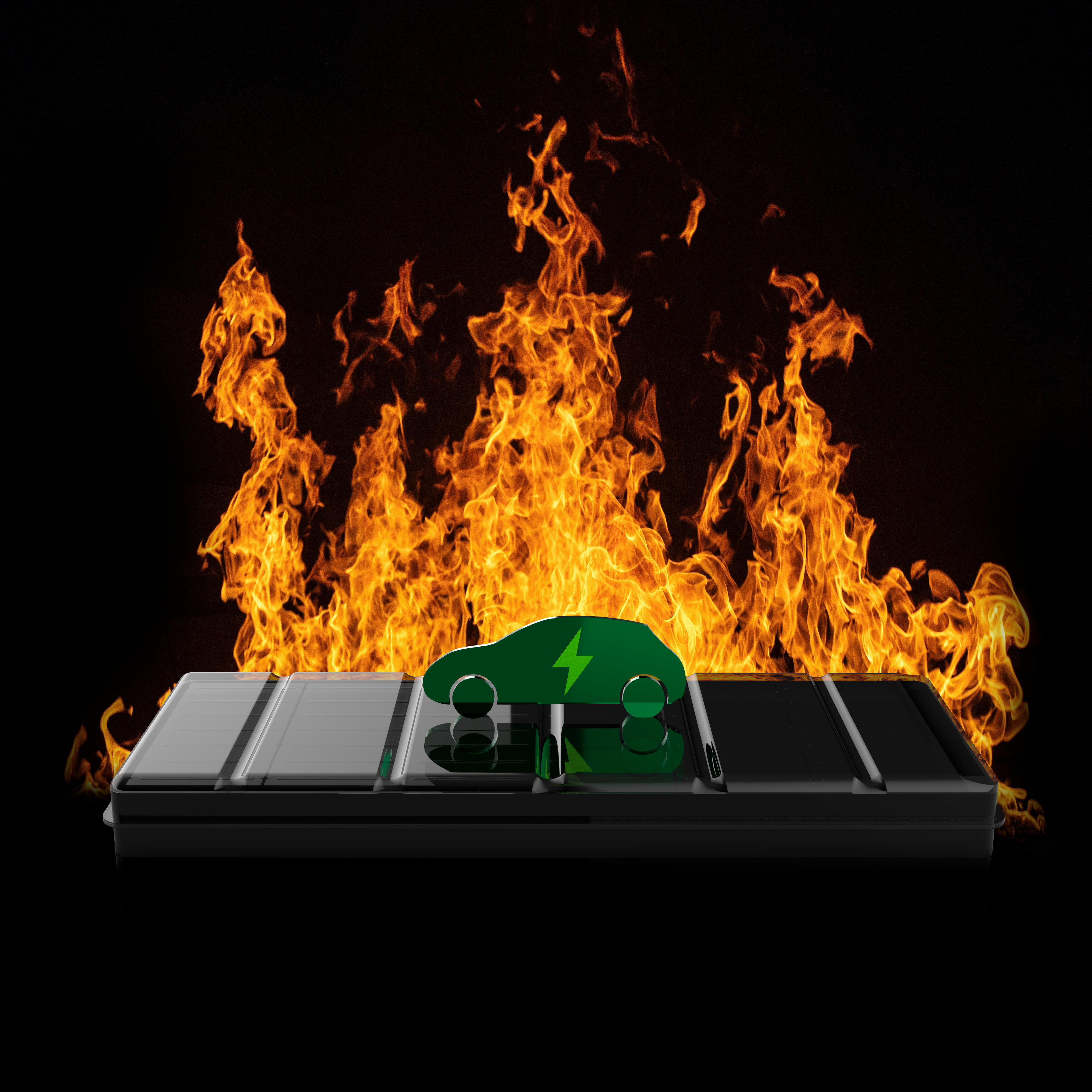
EV batteries need to be lightweight, high-performing, and safe. Although EV battery fires are relatively rare, they are difficult to extinguish. That’s part of the reason why fire remains a safety concern not just for EV owners, but for the design engineers who work for EV battery manufacturers. Then there’s the fact that finding the right materials isn’t always so easy. According to a Gluespec poll, 86% of respondents reported that sourcing fireproofing materials is an important but challenging part of EV design.
Part of what makes material selection challenging is that engineers need to find a variety of sealing, bonding, insulation, and thermal management solutions. For example, in a typical lithium-ion EV battery, an engineer may need to source materials for cell-to-carrier bonding, foam encapsulation, and gap filling. Fireproof coatings and dielectric coatings are also used. This article examines the type of materials for fireproofing EV batteries that you can find on Gluespec, an online technical resource for design engineers.
Cell-to-Carrier Bonding
Battery cells are the basic units of an EV battery. They’re made by inserting a cathode, anode, separator, and electrolyte into an aluminum case that’s usually pouch-shaped, cylindrical, or prismatic with an explosion-proof lid. To keep these high-voltage battery cells in position, their cases are bonded to an electrically-insulating plastic carrier. Often, these cell carriers are made from low surface energy (LSE) plastic. LSE plastics are lightweight, but their surface characteristics can complicate bonding.
Acrylic adhesives are a good choice for cell-to-carrier bonding because they can join metal with plastic, including low-LSE materials. For EV batteries, two main types of acrylic adhesives are used: UV-cure and dual-cure. UV-cure adhesives bond quickly with ultraviolet (UV) light, but bonding won’t occur if there are “shadow areas” where UV light can’t reach. Dual-cure acrylic adhesives take longer to cure but address this challenge. By helping to stabilize battery cells, both types of products help to reduce the risk of fire caused by damaged components.
Foam Encapsulation
Battery cells are assembled into battery packs, and battery packs are assembled into battery modules. Within packs and modules, individual battery cells are surrounded and separated by polymeric foams that provide physical protection against shock. These encapsulating foams add structure and rigidity, and this extra stability improves thermal insulation, which reduces heat transfer. Foam encapsulation also helps to prevent thermal runaway, a dangerous condition where a battery cell enters an uncontrollable, self-heating state that can cause a fire.
Battery encapsulation is typically achieved with silicone, epoxy, or polyurethane foams that resist shock and provide various levels of bond strength and thermal protection. There are advantages, disadvantages, and tradeoffs to each type of material. Silicones resist higher temperatures but have lower adhesion strength. Epoxies have higher bond strength but can’t match silicones in terms of thermal stability, a material’s ability to resist heat’s effects on its properties. Polyurethanes are usually softer than epoxies but tend to suffer property degradation above 125°C.
Gap Filling
Gap filling is a thermal management approach that dissipates heat so that electrical and electronic components work properly and won’t combust. As their name suggests, they fill spaces that would otherwise be filled by air, a poor conductor of heat. In electric vehicles, gap fillers surround or encapsulate battery packs and battery modules. These thermal interface materials (TIMs) move heat away from the EV battery, improving battery speed and longevity while decreasing the likelihood of thermal events.
Typically, the gap fillers for EV batteries are applied through pumping. Because these TIMs are highly abrasive, however, they can cause dispensing equipment to wear prematurely. Their low viscosity can also result in uneven distribution across non-planar surfaces. Today, gap-filling solutions include two-part thixotropic fluids where silicone is mixed with special thermally-conductive ceramics. Because these fluids are thixotropic, they improve coverage and can have higher adhesive bond-line thickness.
Fireproof Coatings
Fireproof coatings for EV batteries include passive fire protection (PFP) materials that are sprayed onto battery pack surfaces and expand when a certain temperature is reached. These lightweight intumescent coatings insulate the EV battery and prevent thermal events from reaching the passenger compartment. Intumescent coatings were used originally in building and construction, but are finding increasing application in the automotive industry, in part because of the increasing popularity of electric vehicles.
For EV batteries, intumescent coatings include two-part epoxy-based materials that cure rapidly to a tough and resistant finish. For best results, it’s important to maintain these materials at the correct temperature during mixing and to dispense them at a continuous flow. Products that cure at ambient temperatures promote energy efficiency. Inorganic formulations that do not contain any hazardous chemicals and that will not produce smoke or fumes are also used as fireproof coatings.
Dielectric Coatings
Dielectric coatings in EV batteries mitigate the risk of thermal propagation, the sequential occurrence of thermal runaway among neighboring cells. When electric vehicles are involved in serious accidents, surfaces with dielectric coatings help to reduce the potential for fire. Specifically, dielectric coatings help to prevent arcing so that electricity won’t jump from one connection to another. They also help to prevent breakdown voltage, the minimum voltage required for an insulator to become electrically conductive.
Although some EV batteries use dielectric powder coatings, Parylene can be applied as a conformal thin film. When compared to epoxy, silicone, and urethane coatings, Parylene has a higher dielectric strength, the maximum voltage that is required to produce a dielectric breakdown through a material. In addition to withstanding intensive electrical activity, Parylene coatings can withstand corrosive liquids. The breakdown voltage of Parylene is determined by the coating’s thickness.
How to Find Fireproofing EV Battery Materials
Gluespec’s comprehensive, quality-tested database of 20,000 adhesive materials is the smart way to find solutions for fireproofing EV batteries. Plus, Gluespec’s Advanced Search provides the tools you need to conduct deep filtering among all material properties. The result is a customized grid that contains materials and data points that are specific to your project. Save custom grids for quick access and share them with your colleagues. To get started, create a free registration and login.