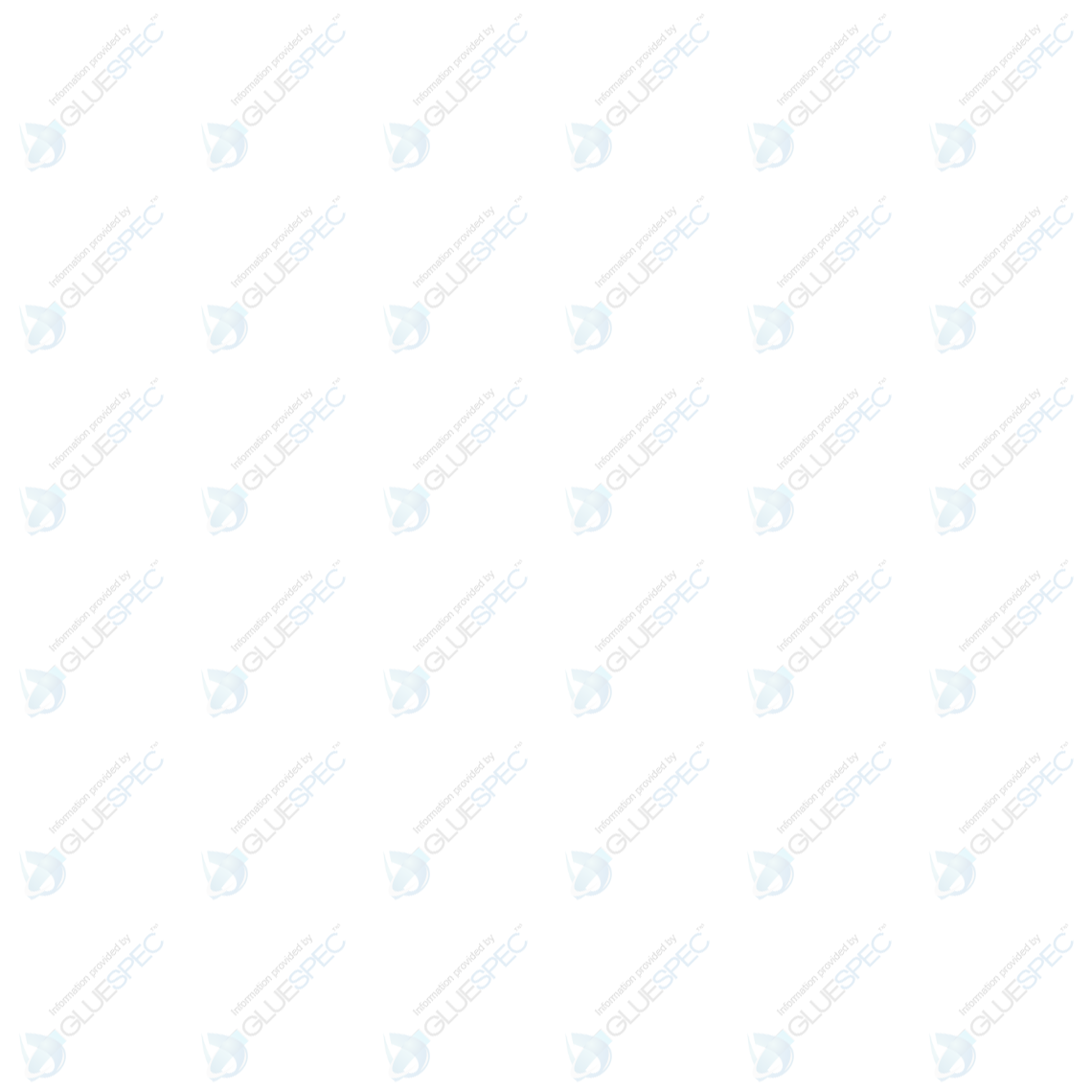
- Contributions by industrial experts with engineers in mind
- Focused on specialty-chemical material applications and selection
Knowledge Center
Primers and Surface Preparation for Proper Adhesive Wetting & Bonding - Q&A
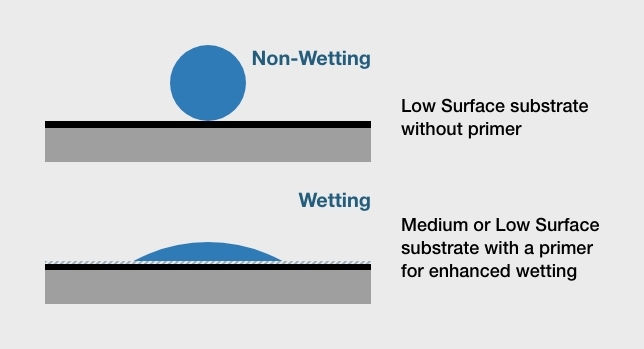
Adhesive primers are coatings that are applied directly to a substrate to improve adhesive bonding, the process of joining two surfaces together by chemical rather than mechanical means. Adhesive promoters also enhance surface bonding but are added to the adhesive formulation itself. Both types of products help to prepare surfaces for bonding, but surface roughening, etching, and plasma, flame, and corona surface treatments are also used. For design engineers who are looking for the right solution, this Q&A from Gluespec® provides answers to frequently asked questions.
Q: How do adhesive primers and adhesive promoters work?
Adhesive primers modify the surface of a substrate so that an adhesive will more readily stick to it. At a molecular level, primers form chemical bonds and are adsorbed onto the substrate, forming a thin layer. Adhesive promoters also form chemical bonds at the interface of the adhesive and the substrate. These functional additives can also improve joint strength and help to prevent adhesive delamination, a mode of failure in which the adhesive fractures into layers.
Q: How are adhesive primers supplied and applied?
Depending on the quantity that is purchased, primers are usually supplied in cans, pails or drums. These liquid materials are then applied by spraying, brushing or dipping. Brushing is a manual process but spraying and dipping can use either manual or automated equipment. No matter which method is used, primers need to be applied as thin coatings because using too much primer can be as detrimental to adhesive bonding as failing to use any primer at all. For best results, surfaces need to be clean.
Q: After priming, can adhesives be applied right away?
Not typically. Many adhesive primers contain a solvent so that the adhesive resin is more easily dispersed and the primer can more completely cover the entire bond area. In most cases, suppliers recommend allowing the solvent to evaporate before applying the adhesive. Solvents typically contain volatile organic compounds (VOCs), so proper ventilation is required. Because solvent evaporation reduces coating thickness, the thickness of an applied primer typically ranges from 0.005 mm to 0.010 mm once evaporation is complete.
Q: Is solvent-based evaporation the only curing mechanism for adhesive primers?
No. Anerobic thread lockers, retaining compounds, gasketing materials, and thread sealants cure in the absence of air and in the presence of metal ions. Before applying these products to metal surfaces, however, it is important to consider whether the metal is active or inactive.
- Active metals such as iron, steel, copper, brass, bronze, and some alloys do not require a primer.
- Inactive metals like anodized aluminum, pure aluminum, stainless steel, galvanized steel, nickel, black oxide, silver, gold, and zinc require a primer, or activator, which contains metal ions.
Primers/activators are also used to facilitate curing with cold metal parts, or with large gaps. Note, however, that primers/activators decrease ultimate bond strength when they are applied to metals before anerobic thread lockers, retaining compounds, gasketing materials, and thread sealants. Therefore, the use of primers/activators is recommended only when needed.
Q: What is wet out – and why does it matter?
Adhesives that “wet” or “wet out” flow readily across the surface of the substrate. This increases the contact area for adhesive bonding and strengthens the attractive forces between the adhesive and the substrate material. If an adhesive does not completely wet out the substrate’s surface, maximum bond strength won’t be achieved and adhesive failure could result. Adhesive primers and adhesion promoters help to wet out the surface, but substrates with low surface energy are hard to bond.
Q: What is the relationship between wet out, surface energy, and adhesive bonding?
A substrate’s surface energy determines how easily an adhesive will wet out the surface. As a rule, substrates with a higher surface energy support greater wet out. Conversely, substrates with a lower surface energy have reduced wet out. The threshold for a low surface energy material is 36 dynes. Typically, dyne pens are used to test dyne levels. In general, most metals have high surface energy and most plastics have low surface energy. However, engineering plastics and natural materials such as concrete have medium surface energy instead.
Q: How do plasma, flame, and corona surface treatments work?
Plasma, flame, and corona surface treatments increase the surface energy of hard-to-bond substrates. Plasma treatment ionizes a gas in a vacuum chamber, flame treatment uses a blend of natural gas and air, and corona treatment uses high voltage and high frequency to create a corona discharge. Because each of these methods requires specialized equipment, they are used typically with higher production volumes and in critical areas where a bond failure may be catastrophic.
Q: How does surface roughening promote adhesion?
Surface roughening promotes adhesion by increasing the available surface area for bonding. It also reduces crack propagation by creating mechanical interlocks. A substrate’s surface may look smooth, but a process like sanding creates additional pores into which an adhesive can flow. Grinding and wire brushes can also be used for surface roughening, which can support manual processing and typically does not require specialized equipment as with plasma, flame, or corona surface treatment.
Q: How do etching agents enhance adhesion?
Like surface roughening, etching creates tiny pores into which an adhesive can flow. However, etching is a chemical process rather than a mechanical one since it involves a reaction between an etching agent and the substrate. To promote adhesive bonding, etching agents are applied to polytetrafluoroethylene (PTFE), a synthetic polymer that is better known by its tradename of Teflon®. Two etchants from Acton Technologies, FluoroEtch® and Tetra-Etch®, are widely used to make hard-to-bond fluorocarbons bondable.
Q: What are some applications for primers and surface preparation?
Primers, adhesion promoters, and other surface preparation methods are used in many different applications. Examples include headlamp bonding in the automotive industry and panel bonding for building and construction. Primers and activators are also used in electronics assembly, and to improve the overall adhesion of tapes or films. For structural bonding, such as in automotive body shops, pigmented primers are available.