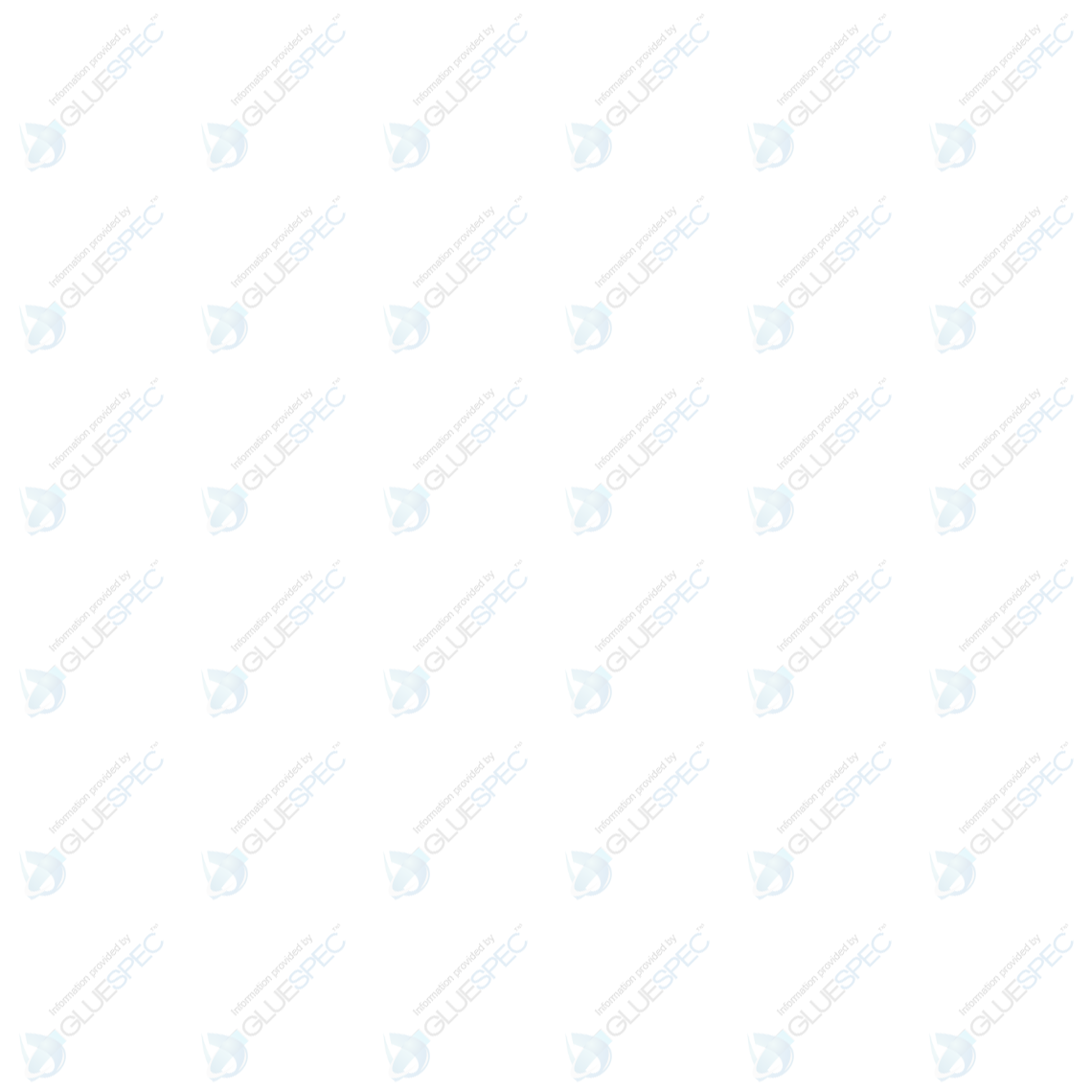
- Contributions by industrial experts with engineers in mind
- Focused on specialty-chemical material applications and selection
Knowledge Center
Battery Construction Issues and Specialty Material Solutions
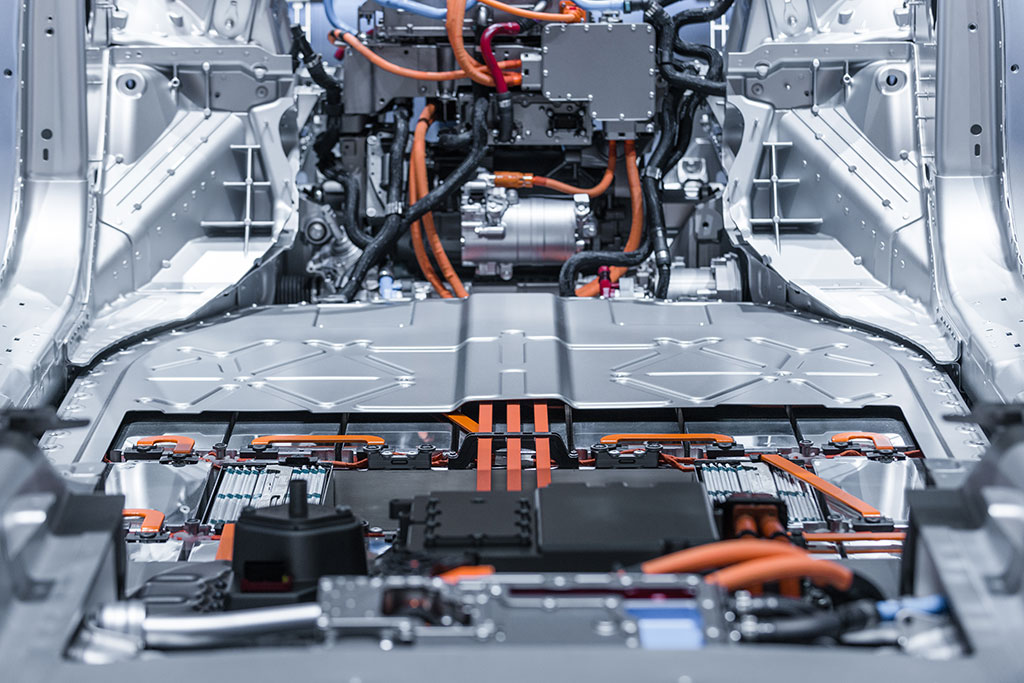
Specialty Battery Materials
Today’s demand for energy usage in a wide range of applications has necessitated the creation of more powerful and compact energy storage solutions. This, in turn, has led to increased complexity both in the chemistries and methods of storage used, as well as more complex methods for regulating and maintaining and protecting those systems. Modern design of batteries and battery packs requires accurately determining the challenges that will be faced and choosing the right materials to combat those problems.
Battery Construction Issues
One of the major issues facing battery engineering is heat. Heat has enormous effects on all aspects of battery operation - charging, discharging, battery life, and safety. Each battery chemistry and construction has ideal operating temperatures, under which relatively even performance and safety can be expected. Operation outside of those temperatures can have a range of unwanted effects, from decreased performance to destructive failure.
Batteries that are too cold are generally safe but experience a slowdown of the chemical processes resulting in decreased performance, sometimes dramatically. There are specific cold-related issues with some batteries. Lithium-ion batteries can experience lithium planting while charging in cold temperatures, leading to a host of other problems.
Batteries that are too hot face more dangerous malfunction. Thermal runaway, where the increased temperatures increases the reaction rate and forms a feedback loop, can lead to permanent damage, physical deformation, or even explosion.
Depending on the battery, and the environment in which it will be operating, systems and engineering designs must be put in place to handle both heating and cooling. These systems are often a combination of active measures like fans and heating elements, and passive factors like heat-sinks and thermally conductive materials.
In addition to heat, batteries face a number of other environmental and situational factors the require specific design solutions. As batteries are being used in more varied and exposed applications, they need greater protection. Electric and hybrid vehicles rely on advanced battery technology, particularly the advantages lithium-ion can provide. But these sensitive batteries and battery packs need protection from moisture and other exposure common in automotive use. Care must be taken also in protecting sometimes-delicate constructions from vibration or shock that can disrupt internal mechanisms. Both of these factors are important in portable electronic device manufacture as well. Likewise, outdoor installations used in renewable and home applications need similar protections from weather and particulates that can interfere with sensitive electronics.
In batteries that require internal controls, solutions are needed to keep control boards safe and secure. These types of control boards are common where battery packs are used, often with lithium-ion chemistries, as they require further management of charging and discharging. Issues with those control mechanisms can be as dangerous as faults with actual battery construction.
There are also a range of electrical protections needed in battery systems, to isolate current and for electromagnetic field insulation, which can disrupt sensitive systems.
Specialty Material Solutions
There are a number of solutions to the many issues involved with battery design - and the best solutions can take care of multiple factors at the same time. Adhesive resins can provide structural solidity that combats shock and vibration, while improving thermal conductivity and dielectric strength. Specific resins and adhesives are suited to different environments and design elements within batteries and battery packs. These compounds can be selected both for their cured properties, and design considerations around construction (length of cure, one- or two-part, materials being joined, etc.)
Gap Fillers
Gap fillers can refer both to compounds used to surround cells in a pack (here described under potting and encapsulation) and also specific pad-like fillers that connect heatsinks and other components. These pads are usually made from flexible silicone materials and also include polyimide-based phase-change materials that are perfect solutions where high dielectric strength and temperature management is needed.
Potting and Encapsulation
Particularly in sensitive lithium-ion battery packs, gaps between and around cells are filled with some kind of resin. These are usually thermally conductive compounds (resins that have been filled with conductive materials) that allow for heat created during operation to dissipate more easily. The type of resin depends on a number of factors - how much heat needs to dissipate, level of ruggedization, and resistance to environmental factors. Some materials - like silicone, cure to a gel-like substance which provides vibration resistance and flexibility without putting stress on internal components. Materials like epoxy and can provide greater environmental resistance and structural strength. Many chemistries can be varied to meet specific needs, including UL94 flammability standards.
This potting also provides dielectric strength to the battery pack - particularly important in high-discharge applications where the flow of energy must be contained along intended pathways or protected in case of damage.
Potting is also used for protecting circuit boards other battery components to protect them from the same kind of environmental and internal factors facing battery cells.
Conformal Coatings
Where control modules are needed, conformal coatings are often used to help protect them since they are so critical to advanced battery operation, particularly in demanding environments. A variety of epoxy, acrylic, and urethane-based solutions are used depending on specific design needs.
Sealing
There is a broad range of sealing applications in battery packs, including sealing the battery module itself, as well as individual components inside modules. These solutions include things like form-in-place or liquid gaskets (often silicone-based), as well as specialized adhesives for EMI shielding, and more conventional adhesives that must adhere well to the advanced materials used in battery-pack construction. Options are available for constructions which need to be opened for service and resealed as well.
Low-pressure Molding
Another option is low-pressure molding some assemblies in the battery module, which can encase individual components or entire assemblies in thermoplastic materials. This provides a high degree of protection to units and can solve a number of issues at the same time including where dielectric insulation is needed and meeting IP69K ratings.
Conductive Coatings
Particularly in lithium-ion construction, coatings are sometimes used on the electrical contacts to improve performance.
Adhesive Chemistries for Specialty Battery Materials
Various base chemistries are available to choose from when designing a battery module or pack. Each of the chemistries likewise have various formulations which can be selected to meet the specific design goals.
Epoxy
Epoxies feature excellent chemical resistance as well as a high level of ruggedization. They make a good choice for environments where chemical exposure is expected including environmental factors, as well as in constructions that expect heavy use or physical shock.
Silicone
Silicone-based adhesives can withstand high-temperature exposure and are flexible even when cured. This allows their use in environments with extreme conditions and can be a good choice where other adhesive would put too much stress on components, or where vibration resistance is needed.
Urethane
Urethanes can be formulated with various-hardness cures while providing excellent adhesion in constructions where those considerations are paramount.
Polyamide
Polyamides are a go-to choice for molding operations and are a low-cost option, making them attractive for a wide range of applications.