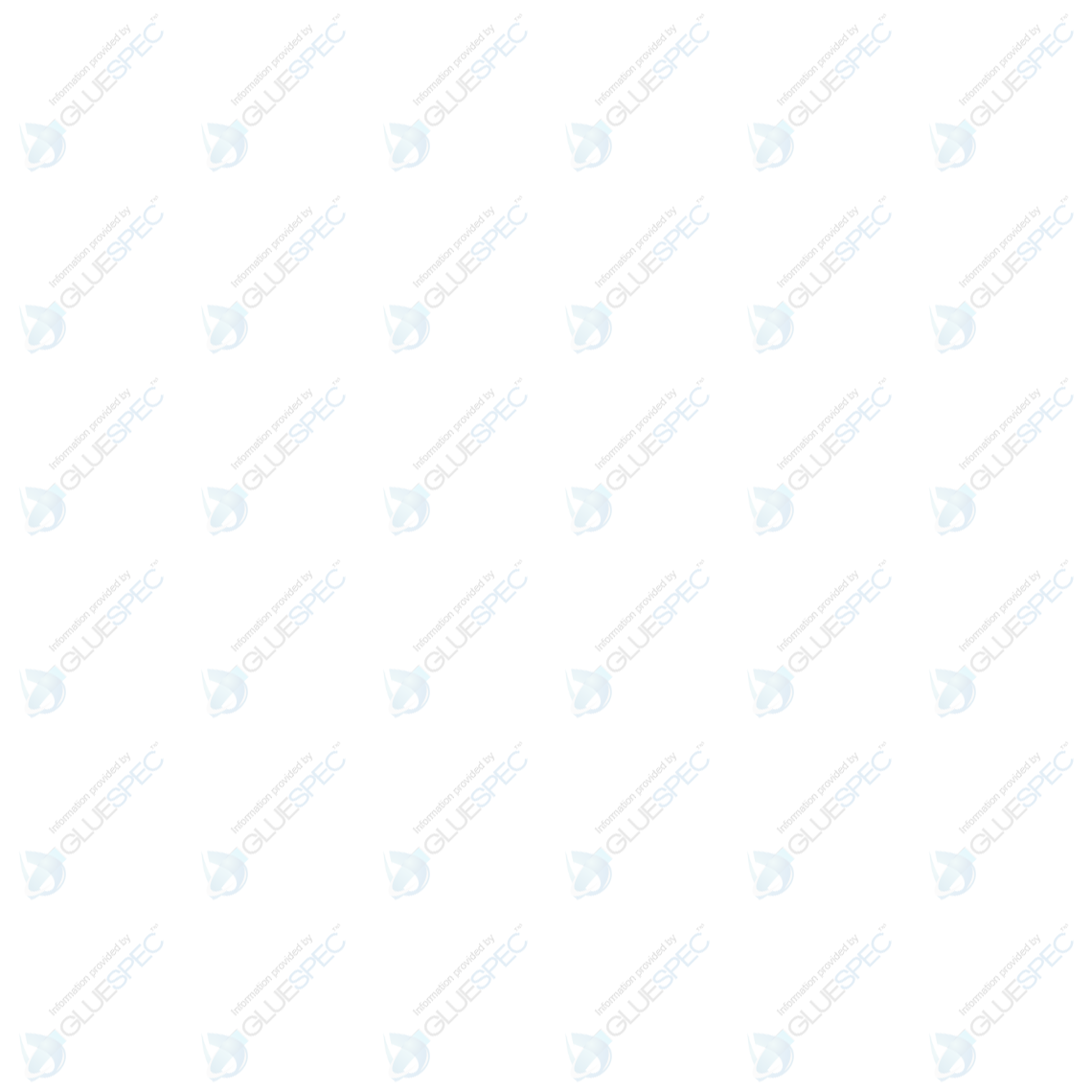
- Contributions by industrial experts with engineers in mind
- Focused on specialty-chemical material applications and selection
Knowledge Center
PSAs in the Sign, Printing and Graphics Industry
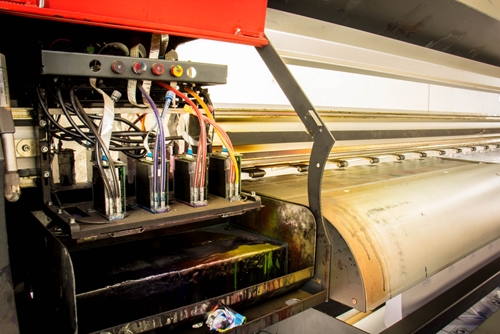
PSAs in the Sign, Printing and Graphics Industry
PSAs in the sign, printing and graphics industry provide a way to directly adhere graphics to surfaces. They are the go-to solution for vinyl decals.
The sign, printing and graphics industry is one that involves constant innovation and requires solutions to unique challenges. Due to the reduction in cost of large scale printers, signage, banners and graphical printing are now commonplace in nearly every environment, and are applied to a growing number of surfaces and modern materials. Adhesives are playing an increasingly important role in the industry as they provide ways to adhere modern materials, allow improved aesthetics and reduce the cost of mechanical fasteners. Pressure-sensitive adhesives (PSA) in particular provide a way to directly adhere graphics to surfaces and have been the go-to for use in vinyl decals.
What are pressure-sensitive adhesives?
Pressure-sensitive adhesives bond upon the application of pressure, rather than through chemical hardening or evaporation. These adhesives can be applied to a backing, as is the case with decals or tapes, which allows them to be adhered by hand or machine at a later time. A release liner is also usually applied, which keeps the PSA from bonding before its final application. PSAs can be formulated with different chemistries that fit an application precisely. PSAs are available for permanent, semi-permanent or temporary adhesion. They bond a wide variety of surfaces and can withstand an array of environments.
There are a number of attributes that can be altered and should be considered when choosing a PSA. The base-chemistry will depend on the surfaces being adhered and the necessary resistance to moisture and chemical attack. Physical properties can also be altered, from initial tack to peel and shear strengths. These will depend on how permanent the application needs to be and the expected operating environment and life span.
"PSAs bond a wide variety of surfaces and can withstand an array of environments."
How are PSAs used in the sign, printing and graphics industry?
In the sign, printing and graphics industry, PSAs have a special purpose - they are generally pre-applied to surfaces like vinyl, polyester or polyethylene which will later be printed on and then adhered to windows, Sometimes the adhesive is applied to a differential release liner, then laminated to the printed film of the sign, this reduces the thickness variation in the printing process. .walls, floors or other displays. The use of a PSA, rather than a separate adhesive added at the point of application, allows extremely high versatility and ease of use. Being integrated into the final product also allows the adhesive to be tailored to the application. Other types of PSA, like glue dots or double-sided tapes, have utility in adhering signage without an adhesive backing. While not as seamless, these types of PSA still have the advantage of creating an improved aesthetic appearance without the need for mixing or cleanup involved with other adhesive solutions.
How to select pressure-sensitive adhesives
Modern PSAs can be tailored to the specific application in which they will be used. A number of attributes can be altered and should be considered when determining what type of PSA to use.
- Chemistry - PSAs can have different base chemistries. The three major categories are acrylic, rubber and silicone. Acrylic is the most common and is suited to a wide range of applications due to the ability to control tack level and its more inherent UV stability. Rubber-based PSAs can offer improved adhesion to certain surfaces, and silicones are often used for high-heat applications.
- Tack - is how quickly an adhesive "wets" and bonds to a surface. This will change depending on the surface adhered to and base-chemistry, but generally low-tack PSAs are useful in situations where graphics will need to be repositioned at the time of adhesion. Tack is different from long-term adhesion, but higher tack PSAs may be necessary in high-speed and other instant-adhesion applications. Most signage adhesives are more "cohesive" than adhesive, meaning upon removal the adhesive will remain on the sign, instead of the substrate.
- Peel Adhesion - Adhesion is the actual strength of the bond formed between the PSA and the substrate it is being adhered to. This will vary depending on application method, temperature and surfaces being adhered. Peel adhesion is important to consider when thinking about removability of graphics.
- Cohesion/Shear - This is the "internal strength" of the adhesive and its ability to stick together under stresses like high heat and shear (parallel) forces. This can come into play when the surface a PSA is bonded to expands and contracts more than the adhesive itself, and needs to be taken into account when extreme environmental conditions are expected.
- Color - Color can play an important part in the overall appearance of adhesive graphics. Opaque adhesives cover up underlying surfaces, while transparent or translucent adhesives can create see-through or light effects in different applications.
When determining what type of pressure sensitive adhesive to use, a number of factors need to be considered, starting with the type of backing the graphic will have and what it will be adhered to. From there, environmental conditions and life span of the decal should be considered, as well as how it will be applied and whether it will be a temporary or permanent installation.