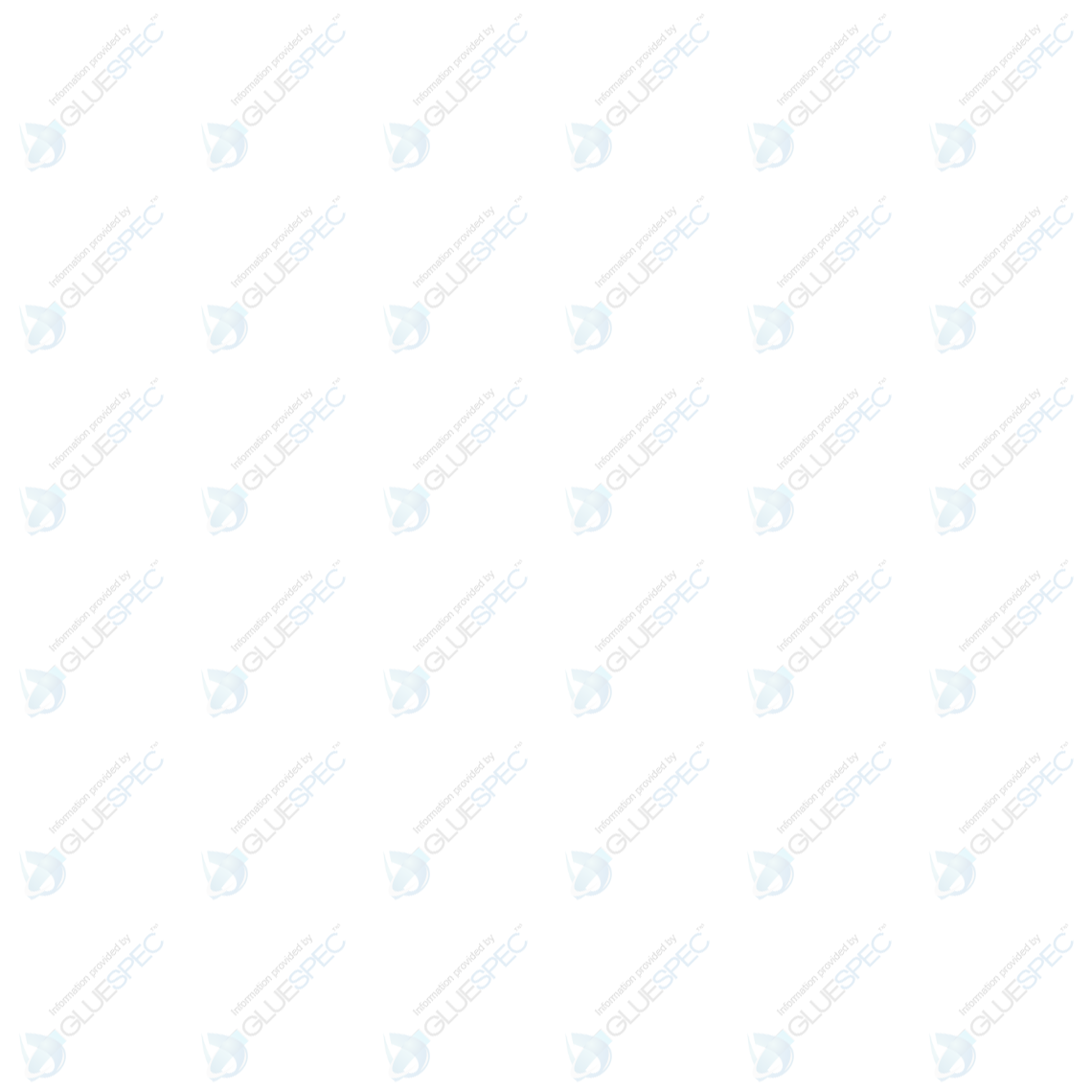
- Contributions by industrial experts with engineers in mind
- Focused on specialty-chemical material applications and selection
Knowledge Center
Thermoplastic Materials in 3-D Printing
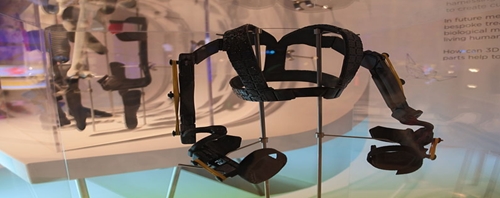
Thermoplastic Materials in 3D Printing
3-D printing, also known as additive manufacturing, has seen an enormous uptick in the past decade due to reduced entry costs and increased DIY interest, but it's actually a relatively old technology. Stereolithography methods developed in the early 1980s are still used today, and other methods like fused filament fabrication (FFF), powder bed binder jetting and sintering have also gained popularity. Advanced technology in design and materials has allowed 3-D printing to be not only a tool for hobbyists but also for an array of industrial applications, including prototyping, modeling and end-use production. Metal and organic matter can also be printed, but thermoplastic materials and methods continue to have the most widespread use and range of application.
Thermoplastic Materials
Thermoplastic materials make up a large portion of 3-D printed materials. These are materials that have been used in industrial modeling and production for years, often through the use of injection molding, but 3-D printing provides new ways to use these materials. Thermoplastics are polymers that melt at high temperature but become stable below their melting point. Depending on the formulation, thermoplastics can have a variety of advantageous properties and are generally quite durable between their melting point and glass transition temperature.
Thermoplastic Printing Methods
There are two main methods used to 3-D print thermoplastic materials. Extrusion (FDM or FFF) and Selective heat or laser sintering (SHS or SLS).
Extrusion
Fused filament fabrication, or fused deposition modeling, is an extrusion method of 3-D printing. Here, thermoplastic materials are pushed through heated tips, which flows like a liquid and then quickly cools into a solid as it's deposited. Objects are built up with each layer of added material. Support structures are used to keep unsupported overhangs from falling or warping - usually these are made out of a secondary material that dissolves in water for easy finishing.
Sintering
SHS or SLS are methods of 3-D printing that involve selectively heating a bed of powdered thermoplastic material. In this method, a layer of powder is rolled out over a bed and then heated by laser or other method to melt specific parts into a single object. After each layer is heated, the bed is moved down and a new layer of powder rolled out. Because unfused powder supports the entire structure, no additional support structures are needed.
Thermoplastic Printing Materials
There's a wide range of thermoplastic printing materials which all have different properties, including durability, finished feel, cost, resistance to heat or chemicals, and others. New thermoplastics for 3-D printing, such as PTFE, are areas of active research and being added to the number of printable materials as demand increases. Blends of these materials are also available that may allow finished products with the best of both worlds, depending on specifications.
ABS (acrylonitrile butadiene styrene)
ABS is one of the most widely used thermoplastics due to its durability and range of formulation. ABS that is electrostaticly dissipative can be 3-D printed for use with electronic or medical devices. Translucent ABS is also available, as well as biocompatible ABS that complies with ISO 10993.
Nylon (polyamide)
Nylon is even more durable than ABS as a thermoplastic material partly due to its ability to stretch slightly under stress. This makes it ideal for objects expected to experience high, repetitive use. Polyamide also offers exceptional chemical resistance. When combined with aluminum powder, the resulting alumide powered offers another compound with exceptional properties for 3-D printing.
PC (Polycarbonate)
PC may be the most-used thermoplastic in industrial 3-D printing. It is extremely durable, even under high heat and stress (above 130°C). It's used frequently in prototyping and tooling. Biocompatible formulations are also available.
ASA (acrylonitrile styrene acrylate) -
ASA is stronger than ABS, but is used most frequently when UV stability is needed. This property allows 3-D printed ASA parts to be used in outdoor prototyping applications, and others involving sporting goods, automotive parts and outdoor housings.
PEI (Ploytherimide)
PEI is another thermoplastic choice that fills a couple of specific niches. PEI thermoplastics can be formulated to meet fire, smoke and toxicity (FST) regulations used in aerospace manufacture, making them an excellent choice for that industry. They are also highly resistant to heat and chemical attack, which allows them to be sterilized in hospital or research settings.
PPSF/PPSU (Polyphenylsulfone)
Polyphenylsulfone offers exceptionally high heat resistance (over 180°C) and is resistance to oil and gas - making it a natural selection for under-the-hood automotive applications.