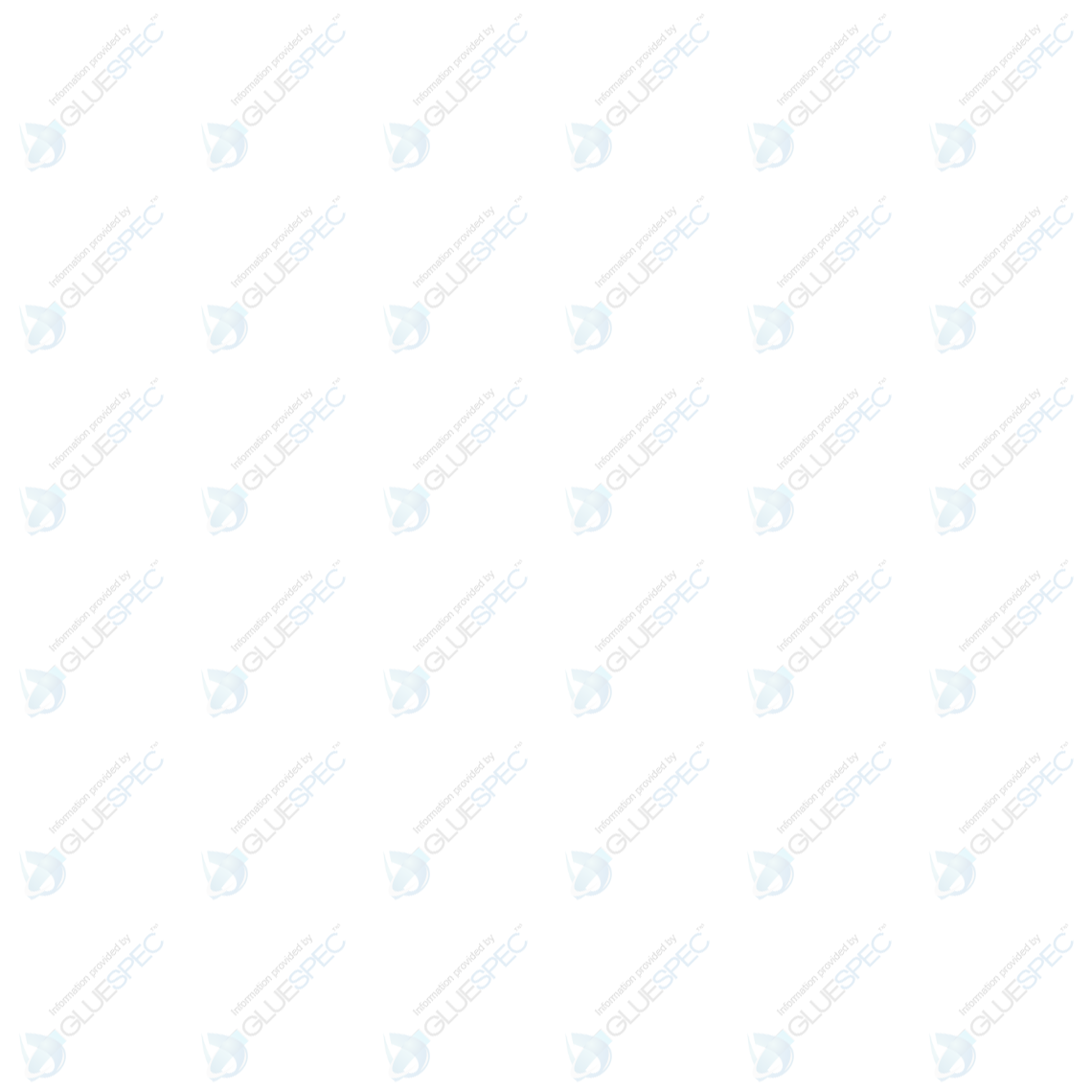
- Contributions by industrial experts with engineers in mind
- Focused on specialty-chemical material applications and selection
Knowledge Center
Pressure-sensitive Adhesives in Packaging
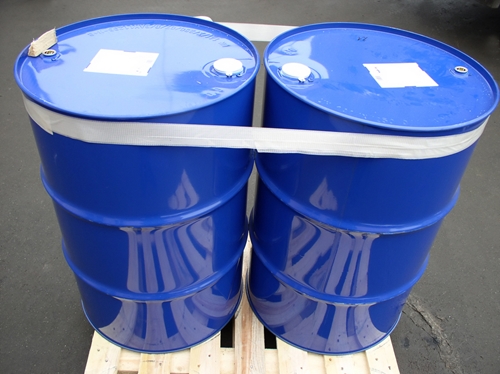
PSAs for Packaging
PSAs for packaging, often in the form of pressure-sensitive adhesive (PSA) tapes, are popular because they are easy and economical to apply.
The packaging industry covers a wide range of products and methods of production - including case and carton sealing, labeling, and working with low surface energy materials like polypropylene and polyethylene. All of these applications can be handled and improved with the use of adhesives. Pressure-sensitive adhesives (PSA), often in the forms of tapes, are widely used in the industry because they are simple and economical to apply, don't require expensive equipment and provide unique advantages over other bonding solutions.
What are PSAs?
Pressure-sensitive adhesives bond upon the application of pressure rather than through chemical hardening or evaporation. These adhesives are usually applied to some type of backing, as is the case in a tape or label, which allows them to be adhered by hand or machine at a later time. A release agent is also applied, which keeps the PSA from bonding before its final application. PSAs can be formulated with different chemistries that fit an application precisely. PSAs are available for permanent, semi-permanent or temporary adhesion. They bond a wide variety of surfaces and can withstand an array of environments.
"Pressure-sensitive adhesives have a number of advantages over other methods of adhering."
There are a number of attributes that can be altered and should be considered when choosing a PSA. The base-chemistry will depend on the surfaces being adhered and the necessary resistance to moisture and chemical attack, as well as FDA or other regulations. Physical properties can also be altered, from initial tack to peel, creep resistance at high temperatures and shear strengths. These will depend on how permanent the application needs to be and the expected operating environment and life span.
Types of PSA in Packaging Applications
- Tapes - A large segment of the PSA use in packaging comes in the form of tapes. Tapes come in a wide range of forms - both with different backings, or carriers, and different adhesive properties. Which combination of properties needed will depend on the exact application. These tapes can have a polypropylene or polyester backing, usually referred to as packing tapes. Fiberglass filaments can be added to these tapes, where they are often called "strapping tape", for increased strength and durability. Double-sided tapes are available that allow concealed placement for improved aesthetic appearance.
- Labels - PSAs can be applied as a backing on labels of all kinds, for either permanent semi-permanent or removable applications. Specific food-safe PSAs are available for direct or indirect food contact, as well as specialty adhesives designed for use in cold or frozen beverages and food.
- Dots – These are pre-formed PSA shapes mounted on a liner. They can be applied manually by a hand applicator or automated conveyor machine and bond directly to the surfaces without a backing. They can be used, like double-sided tapes, to provide excellent aesthetics with variable strengths. They are often used for temporarily adhering inserts or outserts like credit-cards or coupons, and can be used to seal openable packages.
PSAs can also be applied directly to packaging like cartons or bags to make them self-sealing. Release liners can be used to cover up the PSA for later adhesion either in production or by the consumer. Regular letter and shipping envelopes employ this for quick and easy sealing. Variable strengths are available for either permanent bonding or temporary sealing.
Unique Advantages
Pressure-sensitive adhesives have a number of advantages over other methods of adhering. Because the adhesive has already been applied to the backing, it simply needs to be placed on the end-product. Users don't need to invest in expensive equipment for mixing or application in the case of epoxies, nor in equipment for melting in the case of hot-melt adhesives. There are also no concerns about VOCs or other environmental hazards of application, and they can be applied manually anywhere (whereas glue guns require specialized training and electrical access).