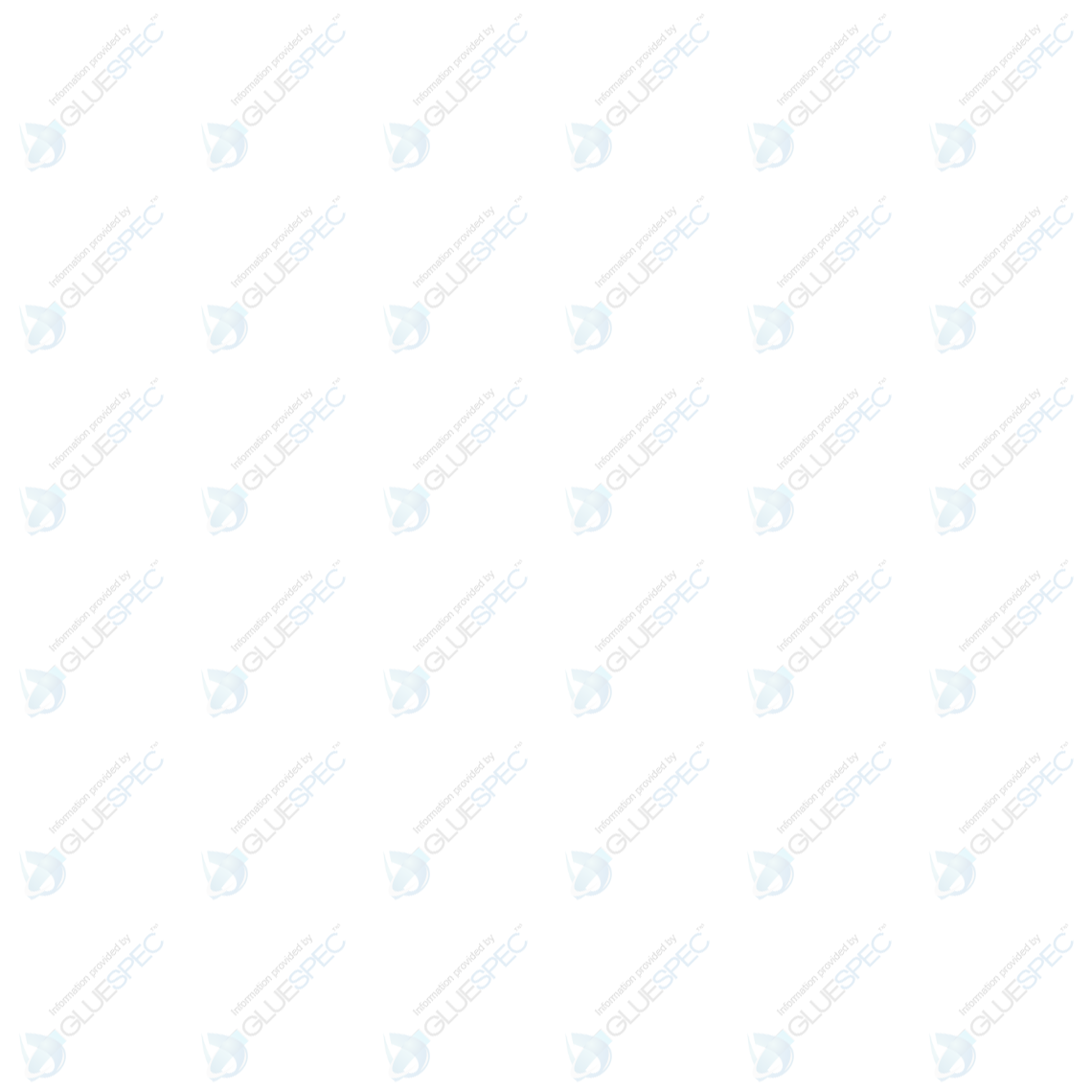
- Contributions by industrial experts with engineers in mind
- Focused on specialty-chemical material applications and selection
Knowledge Center
Epoxies in the Aerospace Industry
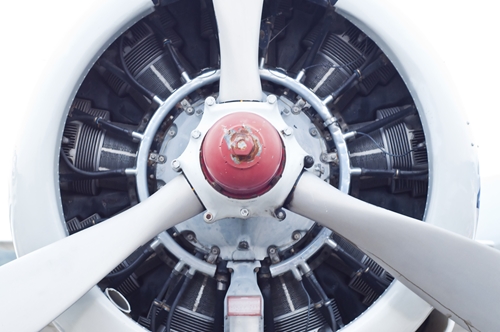
Epoxy Adhesives for Aerospace Assembly
Epoxy adhesives for aerospace assembly support lightweighting efforts and are used for edge bonding and void filling. They are often used in fuselages.
Epoxy finds a number of both interior and exterior uses in the aerospace industry. Because of the extreme and varied conditions, as well as stringent regulations, epoxy makes an excellent choice for adhering and a number of finishing applications.
A lightweight alternative to fasteners
Adhesives, and particularly epoxy, are prized in aerospace construction for their importance in lightweighting. Lightweighting decreases fuel costs and increases flexibility - epoxy can play an important role by replacing or supplementing heavier bonding methods like mechanical fasteners. With the advent of aluminum and carbon fiber for use in aerospace construction, epoxy has played a greater role in combining and finishing those parts. Epoxy is often used in conjunction with pin-bonding to improve strength and retention. Adhesives like epoxy can also reduce the number of pins needed when used to attach aerospace skin components. This reduces stress on components by allowing a more consistent bond line, rather than having stress concentrated on the pins or rivets. They make a natural choice when considering how to compose typical "sandwich" panels used in fuselage construction, since they offer excellent adhesion to a number of materials and resistance to stress, chemicals and moisture.
The right material for aerospace manufacturing
Epoxy is also frequently used in edge bonding and void filling. A number of components in aerospace manufacture are made with a honeycomb structure for strength - epoxy specially made to fill and reinforce the gaps in the honeycomb adds considerable strength without sacrificing flexibility. Epoxy can also be used to edge-fill, particularly for layered components with exposed edges. Because epoxy can be formulated with different viscosities it can easily be worked into voids. Once cured, a number of formulations are also able to be worked or sanded for further processing.
Fuselage interiors are another place where epoxies shine. Because they are so resistant to wear, and can meet flame smoke, toxicity (FST) regulations, they are used to adhere fabrics and other components. Epoxies can also be used as coatings for interior panels and parts that are both resistant and easily cleanable.
More advantages of epoxy adhesives for aerospace assembly
It's easy to see why epoxy is the first place to look when thinking about aerospace construction. Epoxy's ability to bond to a wide variety of materials including unusual ones like carbon fiber and fiberglass is unparalleled. The variability in formulation allows it to be tailored to exact applications, whether adhering or edge/void filling. A number of formulations also cure at room temperature, reducing the need for specialized equipment. Epoxy is resistant to both weathering and chemicals and can meet regulations like FAR25.853 - making it a natural choice for many applications.