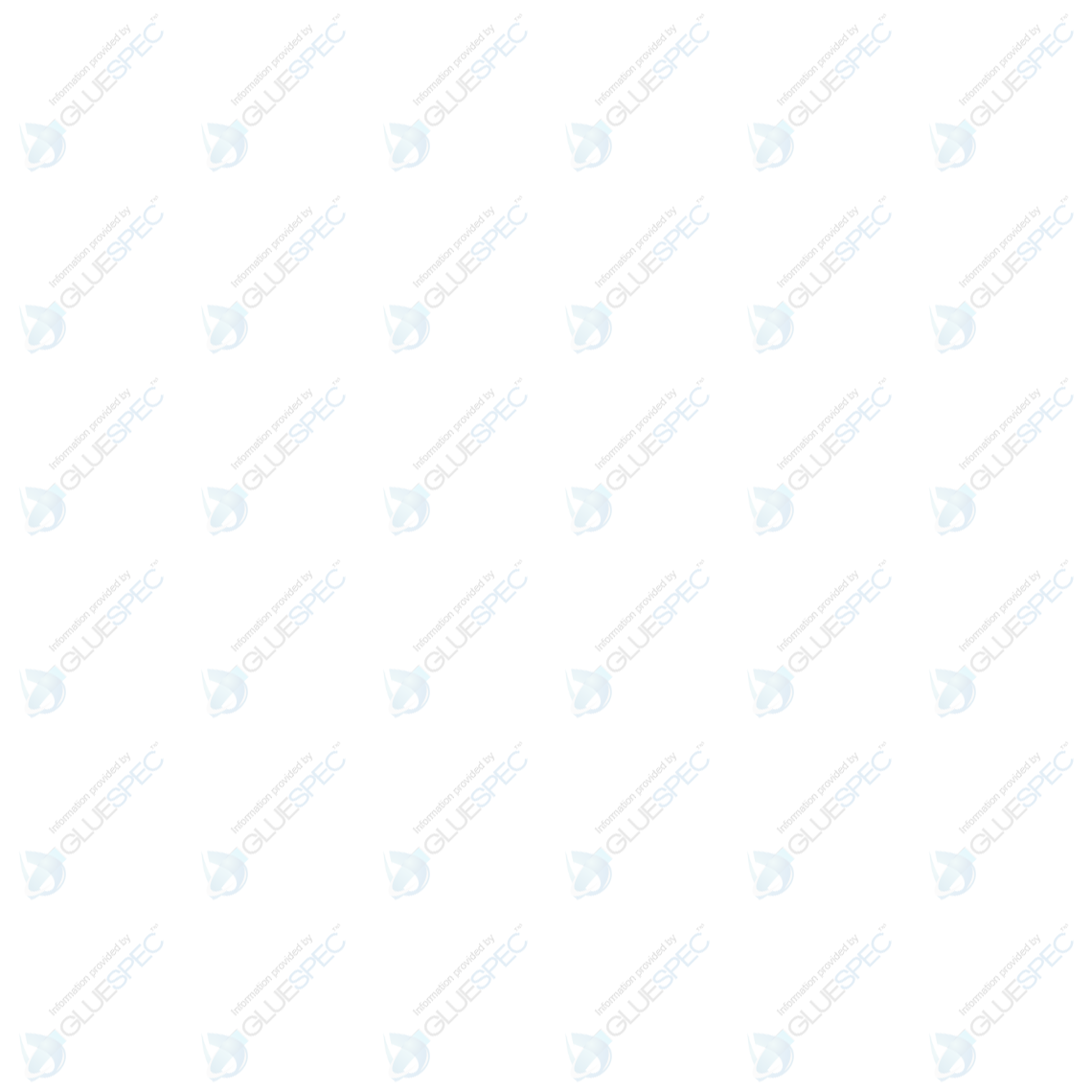
- Contributions by industrial experts with engineers in mind
- Focused on specialty-chemical material applications and selection
Knowledge Center
Hot Melt Adhesives in the Packaging Industry
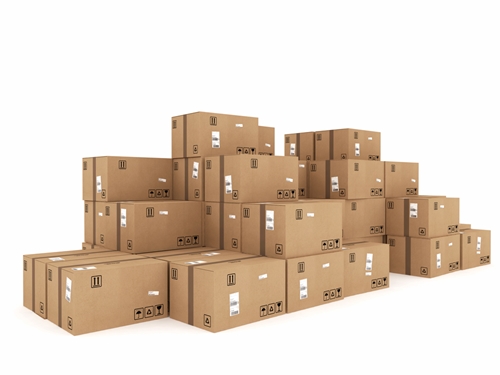
Hot Melt Adhesives for the Packaging Industry
Hot melt adhesives for the packaging industry are used in carton and case sealing, paper goods, plastic container bonding, and labeling applications.
The packaging industry covers a wide range of products and methods of production - from case sealing and construction of all types of paper products, to structural strengthening of pallets and working with modern materials like polypropylene. All of these applications can be handled and improved with the use of adhesives. Hot melt adhesives in particular are a perfect fit for packaging, being simple and economical to apply, withstanding expected stresses and offering excellent bonding on the types of materials used.
What are Hot Melt Adhesives?
Hot melts are so called because they are sold in a solid form, melted in dispensing equipment, and applied hot to the surface or surfaces they will join. They have a good initial tack/green strength, allowing quick processing. HMAs form bonds as they cool into a thermoplastic resin. This final cured thermoplastic can have variety of properties depending on the unique formulation, but is generally flexible, somewhat resistant to water and chemicals, and stable in temperatures below the original melting temperature. There are two classes of HMAs: reactive and nonreactive. Nonreactive HMAs cure only through cooling, but reactive HMAs also cure through chemical reactivity to form crosslinked bonds that can increase adhesion (particularly to low surface-energy materials) and improve resistances. Ethyl-vinyl- acetate (EVA) is the most common form of nonreactive hotmelt. Reactive hotmelts can be based on a number of polyolefins, but the most common is polyurethane (HMPUR).
"Carton and case sealing is a major application area for HMAs."
HMAs are ideal for integration into assembly line manufacture. They are sold in a variety of sizes, from individual application to bulk quantities of solid pellets or sticks. They have an excellent shelf-life and can be simply loaded into melting apparatus when needed.
Traditional EVA Hot Melts vs. New PSA Formulations
New formulations have advanced beyond the traditional Ethylene Vinyl-Acetate (EVA) compositions that formed the basis of early HMAs. EVA hot-melts have also been improved by the addition of tackifiers, waxes and other additives that alter and improve open times, adhesion and cured properties. Flexibility and heat resistance can all be altered with modern HMA technology. Recent research into high-performance HMAs with the use of pure monomer resins (PMR) has allowed hot melts to be used in an even wider array of environments, with increased aesthetics and quicker assembly.
Different base compounds can provide other advantages. Polyolefin (PO) HMAs in particular can provide excellent adhesion for polypropylene, and offer better resistance to moisture and chemicals. Reactive urethane hot-melts are another new area that allows for application at lower temperatures (around 250F) for heat-sensitive surfaces that wouldn't ordinarily be able to withstand the 400F temperatures needed for other hot-melts. All types of HMA can be formulated to meet the requirements of CFR 175.105 for indirect food contact.
How are holt melt adhesives used in the packaging industry?
Hot Melt Adhesives cover the gambit in terms of packaging applications.
- Carton and Case Sealing - Carton and case sealing is a major application area for HMAs. EVA is frequently used for this application because of its excellent adhesion on paper and cardboard, ease of application and low cost. Additives can alter the properties of EVA for use in extreme cold temperatures sometimes needed for beverage cases (down to -40F), as well as for higher temperature ranges (up to 150F).
- Paper-goods - Everything from paper cups to bags to spiral wound tubing, can be adhered with HMA adhesives. EVAs are also a common choice due to ease of use in high throughput assembly lines. Specialty formulations for products expected to reach high temperatures may be needed.
- Plastic container bonding - HMAs can also be used in plastic containers. Polyolefin-based HMAs like HMPUR and polyester offer improved bonding to these low-energy surfaces. Care must be taken that the application temperature is low enough not to affect the substrate, so low-temperature HMAs are often used.
- Labeling - Labeling on all types of containers can be achieved quickly and economically with HMAs. Depending on the substrate (glass, metal plastic, etc.) and environmental conditions, different types of HMA may be used.
Dispensing of HMAs is as varied as the types of HMA available. Manual application is an option for smaller throughput operations. In these cases, glue sticks and guns that melt solid HMA on demand are available. Larger apparatus can be used that have a reservoir which will accept bulk adhesive in the form of pellets or draws from a larger, external tank. All sorts of automated equipment are available as well, which can melt large, bulk quantities of adhesive in various forms and dispense through precision nozzles, sprayer, rollers or with printing methods.