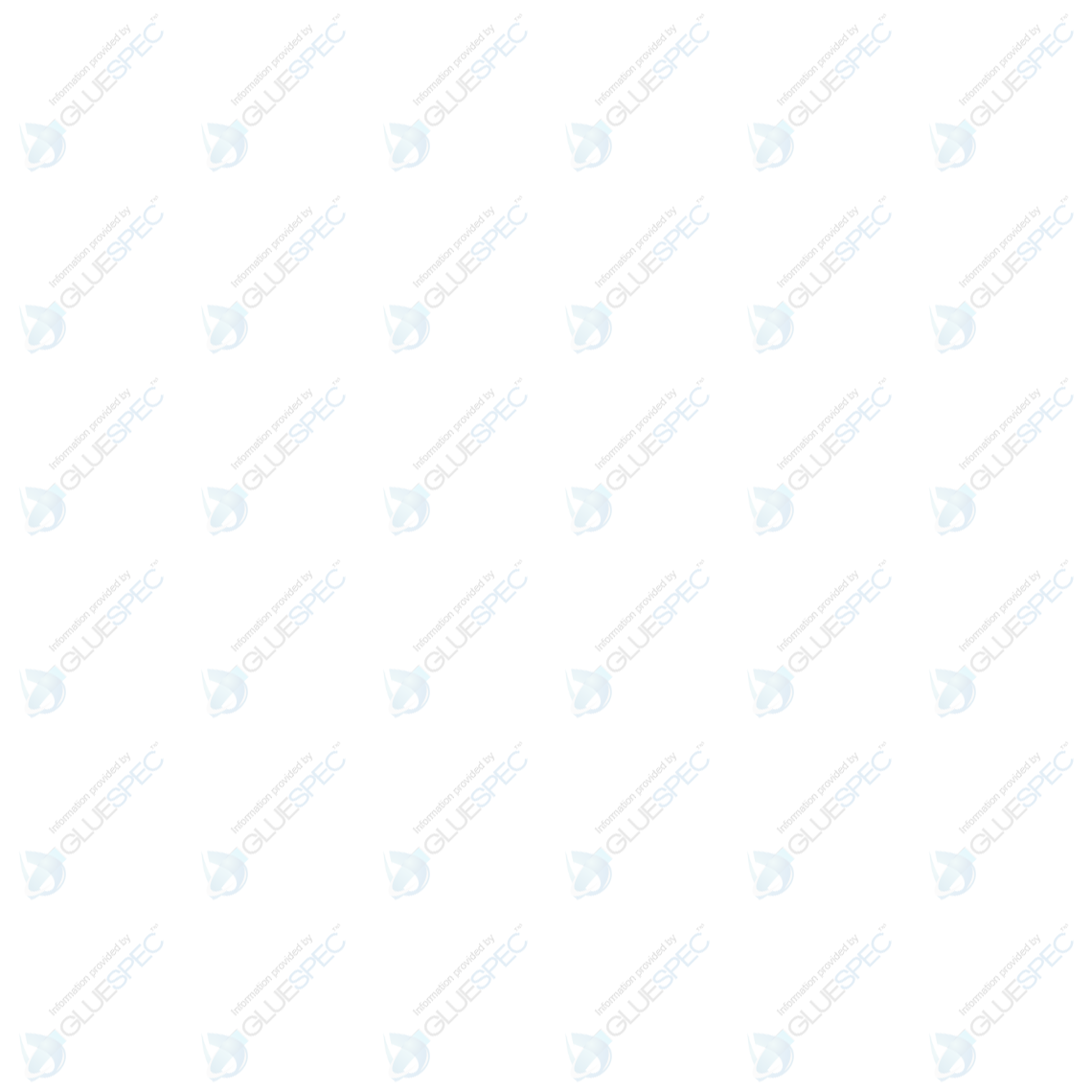
- Contributions by industrial experts with engineers in mind
- Focused on specialty-chemical material applications and selection
Knowledge Center
Epoxies in Loudspeaker Assembly
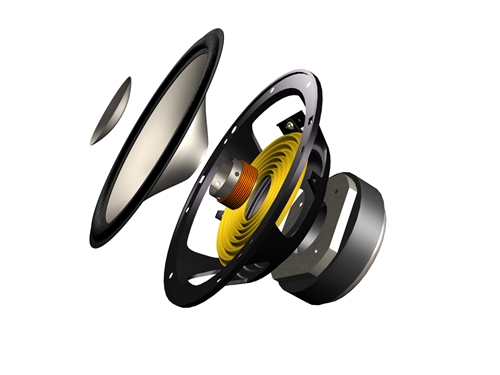
Epoxy Adhesives for Loudspeaker Assembly
Epoxy adhesives for loudspeaker assembly play an important role in high-powered devices because they can handle the high temperatures created by the voice coil and magnet.
Loudspeaker and microphone manufacturing are a large and growing industry - modern venues require advanced and powerful sound systems, and the explosion of portable electronic devices means speakers are now ubiquitous. Adhesives have always played a role in the construction of various loudspeaker components, allowing quick, simple and strong assembly. While cyanoacrylate glues are used more widely, epoxies play an important role, particularly in high-powered loud speakers due their ability to handle the high temperatures created by the voice coil and magnet.
What are epoxy adhesives?
Epoxies are one or two-part adhesives that cure via chemical reaction rather than solvent evaporation or moisture curing. This process usually takes longer than other types of adhesive and can require extended clamping, but the bonds formed are exceptionally strong and resistant to both chemical and physical forces. Fixture times are on the order of hours, and full cures can be achieved in 24 hours. Another advantage of epoxies is their gap-filling potential, which allows for larger tolerances. There are also no VOC concerns with epoxies, making them an environmentally friendly alternative. Epoxies can also be formulated with different mixing ratios and additives to provide properties tailored to individual applications. One-part formulations usually require heat-treatment to activate curing, whereas two-part formulations cure at room temperature. Proper mixing ratios are critical and can be achieved with the use of automatic meter-mix equipment or mix-nozzle cartridges.
"The extreme stresses experienced in high-powered speakers are handled well by epoxy adhesives."
UV-cured epoxies are another option that combines the exceptional strength and resistance of epoxies with the faster processing potential of UV-curing. With these epoxies, UV light can be used for quick bonding, and the secondary chemical cure completes any uncured areas. Specialized equipment is required and can be integrated into assembly-line processes.
Filled epoxies are another type of epoxy adhesive that contains a high level of conductive material. These can be used to make connections that would typically be soldered, but do not generate or require heat, allowing their use on delicate materials.
How are epoxy adhesives used in loudspeaker assembly?
Epoxies are used mostly for bonding voice coils to spiders and cones. The extreme stresses experienced in high-powered speakers are handled well by epoxy adhesives. Epoxies also make an excellent choice for assemblies expected to experience high temperature or exposure to moisture and liquid or chemical vapors. Two-part formulations are frequently used and applied with automated, semi-automated or manual equipment. Because they need extended times to cure, they are often best suited to batch or custom production, rather than high-volume processing. UV-light cured epoxies can offer a compromise between processing speed, strength and resistance for higher throughput applications. The mass production of ear buds, blue tooth earpieces, head sets, cellphones with mini-speakers and mics create a large demand for many types of epoxies. Hearing aid technology is also a large and growing market. Here silver-filled epoxies are commonly used to make connections on a micro level within the ear piece due to the delicacy of the components being used.