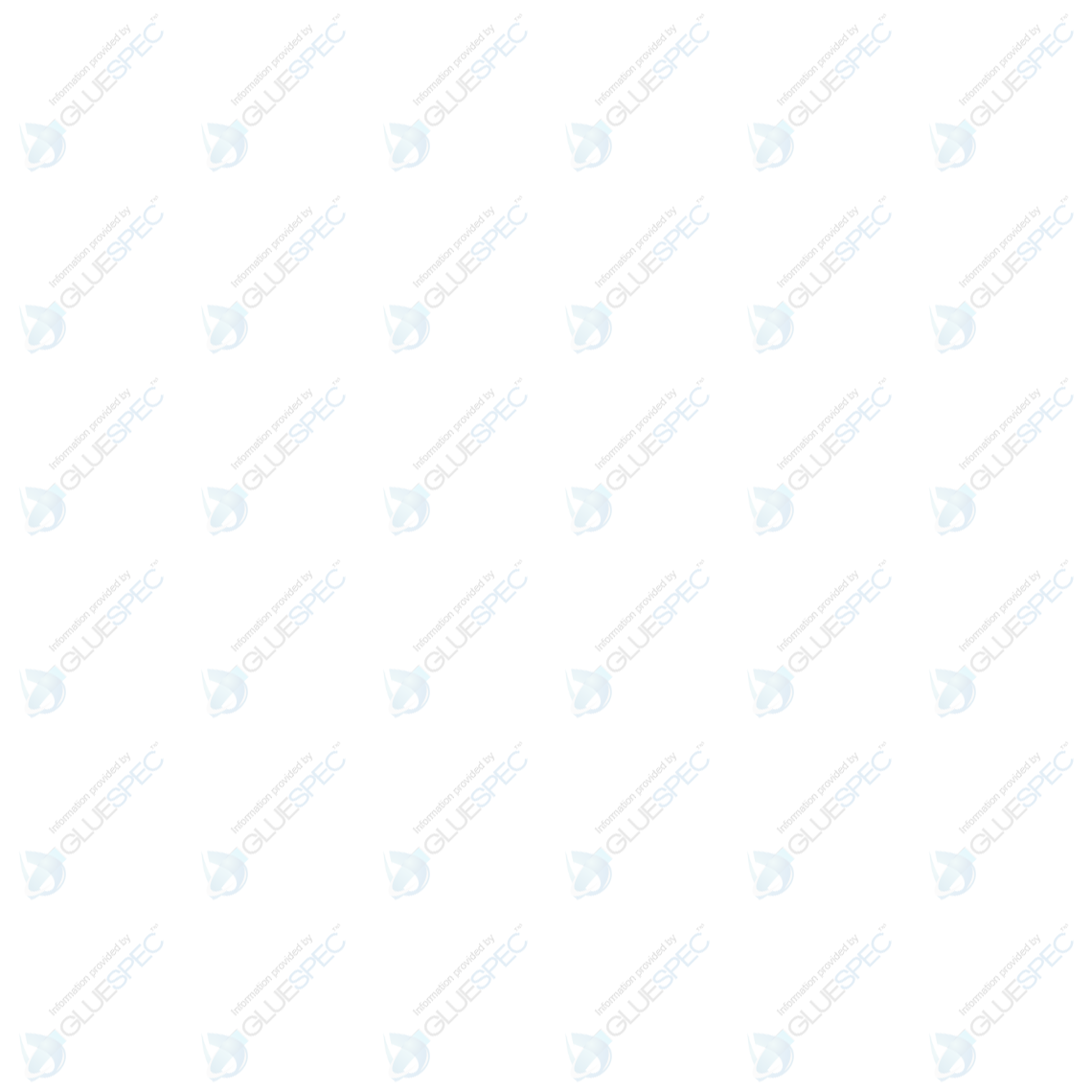
- Contributions by industrial experts with engineers in mind
- Focused on specialty-chemical material applications and selection
Knowledge Center
What to know about Hot Melt Adhesives
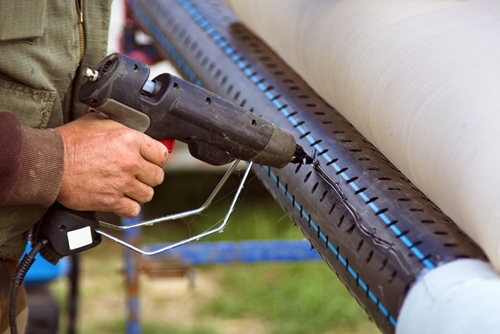
Hot Melt Adhesives
Hot melt adhesives (HMA) cover a broad range of adhesives with diverse applications from packaging to manufacturing to consumer use.
Hot Melt Adhesives (HMAs) cover a broad range of adhesives with diverse applications from packaging to manufacturing to consumer use. Hot melt adhesives are so named because of the way they are used and applied – pellets or sticks of solid adhesive are heated in a dispensing apparatus and then applied to substrates in a molten liquid form. They can be applied directly with handheld guns, automated dispensers or sprays. HMAs are made of a thermoplastic resin that forms bonds as pressure is applied and it cools. They adhere well to a variety of surfaces, including porous and non-porous substrates, and have long shelf-lives.
HMAs offer some advantages over chemically curing and solvent-based adhesives - VOCs are not a concern with HMAs, and cure-times are not a factor in production. Bond strength is not necessarily as strong, but in applications where high bond strength isn't necessary HMAs can provide a cheaper and more versatile alternative. All of these factors lead them to be the industry standard for a number of packaging solutions, including all types of paper and cardboard box construction (case sealing). Because of their quick application and setting they are also perfect for in-line application of labels. HMAs are finding growing use in the assembly of automobiles, appliances and other manufacturing tasks as well.
"Hot melt adhesives can be formulated to be resistant to water and other chemical solvents."
There are a number of other advantages to hot melt adhesives that make them suited for a large range of applications. Bonds formed by HMAs are flexible, a necessity in some packaging and manufacturing applications like bags and disposable hygiene products. They can also be formulated to be resistant to water and other chemical solvents. Because they set by cooling, rather than drying or evaporation, the adhesive doesn't lose any of its thickness when setting. HMAs are also useful in gap-filling applications, which allows greater versatility in their use. Because HMAs need to reach a certain temperature to be applied (175-250 C) they can't be used in temperature-sensitive applications where that level of heat would damage bonded components, though some compositions of HMA are formulated to be applied at under 150C.
Types of Hot Melt Adhesives
HMAs are quite versatile in their composition and there are a number of base-compositions with distinct properties which form the major sub-groups of hot melts.
Ethylene Vinyl-Acetate (EVA) is one of the most common bases for hot melts. Properties can be altered by changing the ratio of vinyl acetate to ethylene in the formulation, with a trade-off between bond strength and flexibility, among other factors. These are frequently used for case and carton sealing as well as product assembly, particularly with paper products.
Polyamide (PA) based hotmelts are useful for high-temperature applications and can maintain bonding strength in applications above 100C in most cases. They are also resistant to oil and gas and can bond PVC, which can be difficult with other HMA formulations. Polyamide hotmelts are also the go-to HMA for bonding metals like aluminum and others.
Polyurethane (PUR) also called reactive urethanes are high-performance HMAs that can be used in high-temperature applications. They can also be formulated to form cross-linked bonds with a secondary cure, making them stronger. Their strength and flexibility has led to their use in bookbinding, automotive, and many other manufacturing uses.
Polyolefin (PO) exhibits excellent adhesion on polypropylene, and can be used for bonding other non-polar substrates, packaging and in automotive applications. They're an excellent choice when an extended open-time is needed for working or repositioning. Amorphous polyolefins (APO or APAO) are a subtype that offers high thermal and UV stability and bonding to many substrates for use in a variety of industries including packaging, product assembly, bookbinding, woodworking and others.
Polyester HMAs also offer excellent heat resistance and adhesion to a number of surfaces. They are resistant to a number of solvents as well, and have found use in demanding applications like automotive assembly, aerospace and footwear.
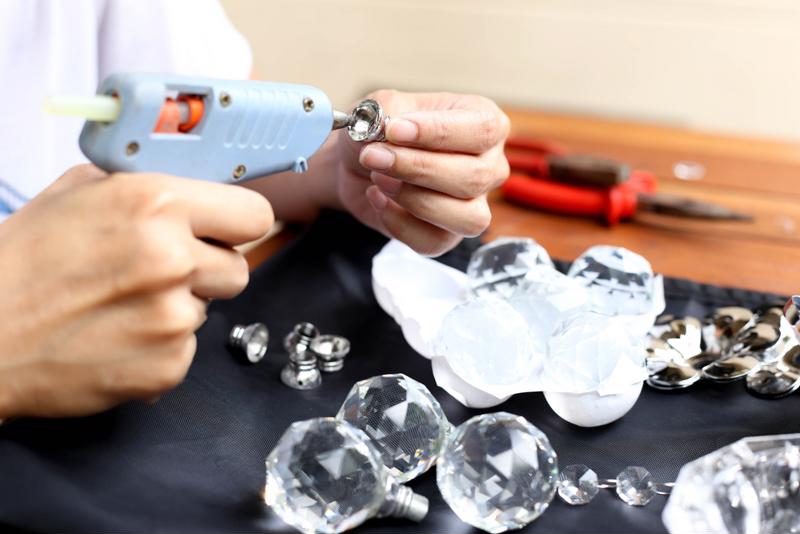
A special subsection of HMAs is referred to as pressure sensitive adhesives. This class of HMAs is used primarily in different types of tapes and labels, either for permanent or temporary bonding. These hot melt PSAs are available in various shapes and thicknesses on different carriers. They are commonly used for attaching cards or promotional item in magazines, case and carton sealing, disposable hygiene products, as well as hundreds of other uses.
HMAs can also be used in low-pressure molding – most thermoplastics can be heated and injected into a mold forming everything from casings for wires to larger housings for components.
Properties of Hot Melt Adhesives
Many of the qualities of HMAs can be altered, even within different compositions, to create an adhesive that is suited to the exact application. Open times and set times are two of the most important aspects to consider when choosing an appropriate HMA. Open time refers to the amount of time after an adhesive has been dispensed that it remains liquid and can adhere or wet surfaces. These times are usually on the order of seconds and can range up to minutes. Set time refers to the time when the adhesive has cooled down to its intermediate or final bond strength.
In addition to the open and set times, which are the major considerations in production, operating temperatures after production need to be considered. If HMAs are brought back up to their application temperature they will remelt, but even at temperatures below that point they can experience "creep" which is the tendency of the adhesive to deform under stress. Depending on the application this can limit the potential operating temperature of components bonded with HMAs. This temperature is usually between 50 and 100C, but high-temperature formulations can be used up to 150C.