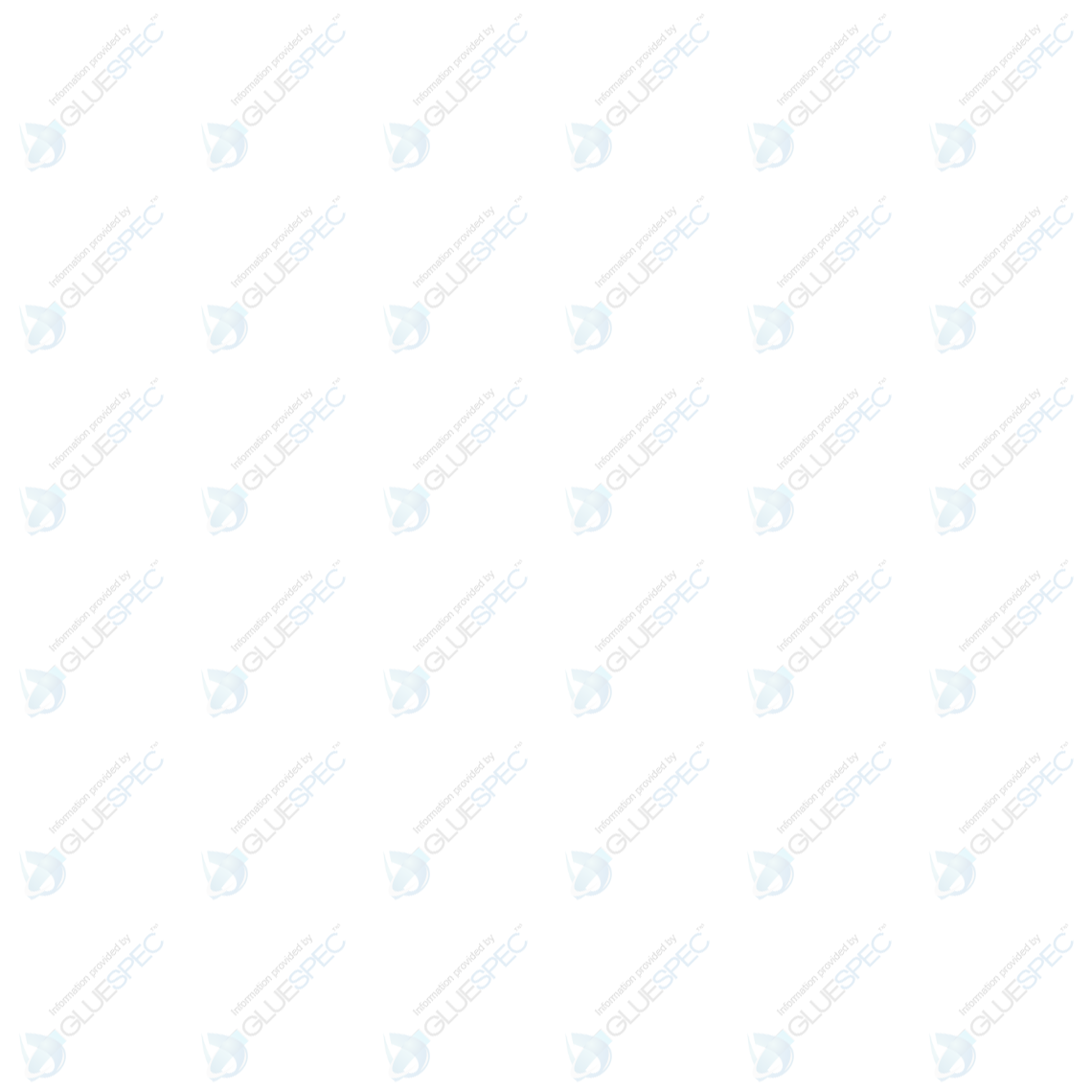
- Contributions by industrial experts with engineers in mind
- Focused on specialty-chemical material applications and selection
Knowledge Center
Cyanoacrylates in the Appliance Industry
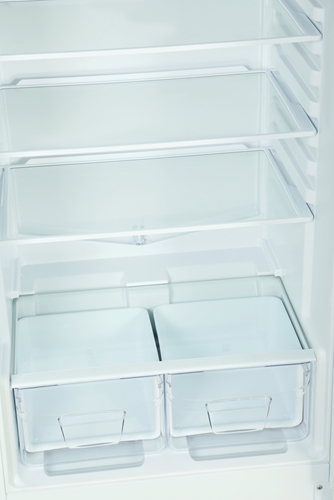
Cyanoacrylate Adhesives in Appliance Manufacturing
Cyanoacrylate adhesives for appliance manufacturing offer extremely quick bonding times and can bond many types of plastic used in the industry.
The appliance market has grown rapidly as demand rises across an increasingly affluent global population. As the market grows, manufacturers are looking to lower costs and increase production speeds. Adhesives offer a simple way to meet these demands.
Replacing mechanical fasteners with glues can allow for faster in-line production and reduce part inventories while allowing improved aesthetic appearance. Adhesives also reduce the weight of assemblies, particularly important in a worldwide shipping market. Increased use of plastics has also led to the need for new bonding solutions. Cyanoacrylate (CA) adhesives offer extremely quick bonding times and the ability to bond many types of plastic used in the industry.
What are cyanoacrylate adhesives?
CA adhesives are often referred to as "instant" or "super" glues, because of their speed of bonding and high strength. CAs polymerize rapidly on contact with moisture - usually moisture in the air or on surfaces is enough to cure the adhesive completely. While original formulations were known for their relatively low resistance to chemicals and shock - modern formulations have overcome these limitations. Rubber-toughened CAs have greater flexibility and strength, allowing for vibration resistance. Other formulations can tailor CAs to the environment they are used in such as high heat or moisture. While cyanoacrylates typically have little to no gap-filling ability, new "gel" CAs can allow for larger tolerances between parts and adhesion to porous surfaces. Large gap bonds (greater than 7 mil) sometimes require the need for an activator for complete curing. Activtors can be applied with brush or pump spray.
"CAs typically cure to fixture strength in just seconds, and full strength is achieved in 12-24 hours."
Cyanoacrylates have a number of properties beneficial to the appliance industry. Quick bonding is an obvious advantage - CAs typically cure to fixture strength in just seconds, and full strength is achieved in 12-24 hours. Bond strengths are extremely high, even between dissimilar substrates, allowing for permanent bonding over the lifetime of parts. Cyanoacrylates bond very well to metal surfaces, but can also bond rubber and low-energy plastics like polyolefins (polyethylene and polypropylene). The use of a primer to prepare low-energy surfaces allows for strong bonds on these surfaces. Activators can also be used before or after application to increase curing speeds. Surface-insensitive formulated CA adhesives can be applied to unprepared substrates, such as wood or high pH materials, making for faster processing. A growing focus on recyclable components give CA adhesives another advantage - because of the small bonding area needed it's easy to reuse most of the bonded plastic.
How are cyanoacrylate adhesives used in appliance manufacturing?
Cyanoacrylates have a number of specific applications within the appliance industry. They are often used in bonding handles and glass shelf assemblies in refrigerators or other appliances. CAs make excellent general purpose adhesives for switches, dials and control panel assemblies on a wide range of white goods - from microwaves to washing machines and air conditioners. Logo and label bonding, as well as some rubber footings, are another area where CAs excel. Cyanoacrylates can be used on internal parts including magnet bonding and fixturing of components.
Application is easy with automated or semi-automated equipment, and because of the bond strength, only small amounts of CA are needed for sufficient bonding. Equipment is available to work with large quantities in barrels, or smaller bottles in pressure reservoirs. Care must be taken to avoid contact with moisture, so dry pressurized air is needed to provide pressure, and polyethylene pins help to keep equipment free of cured adhesive.