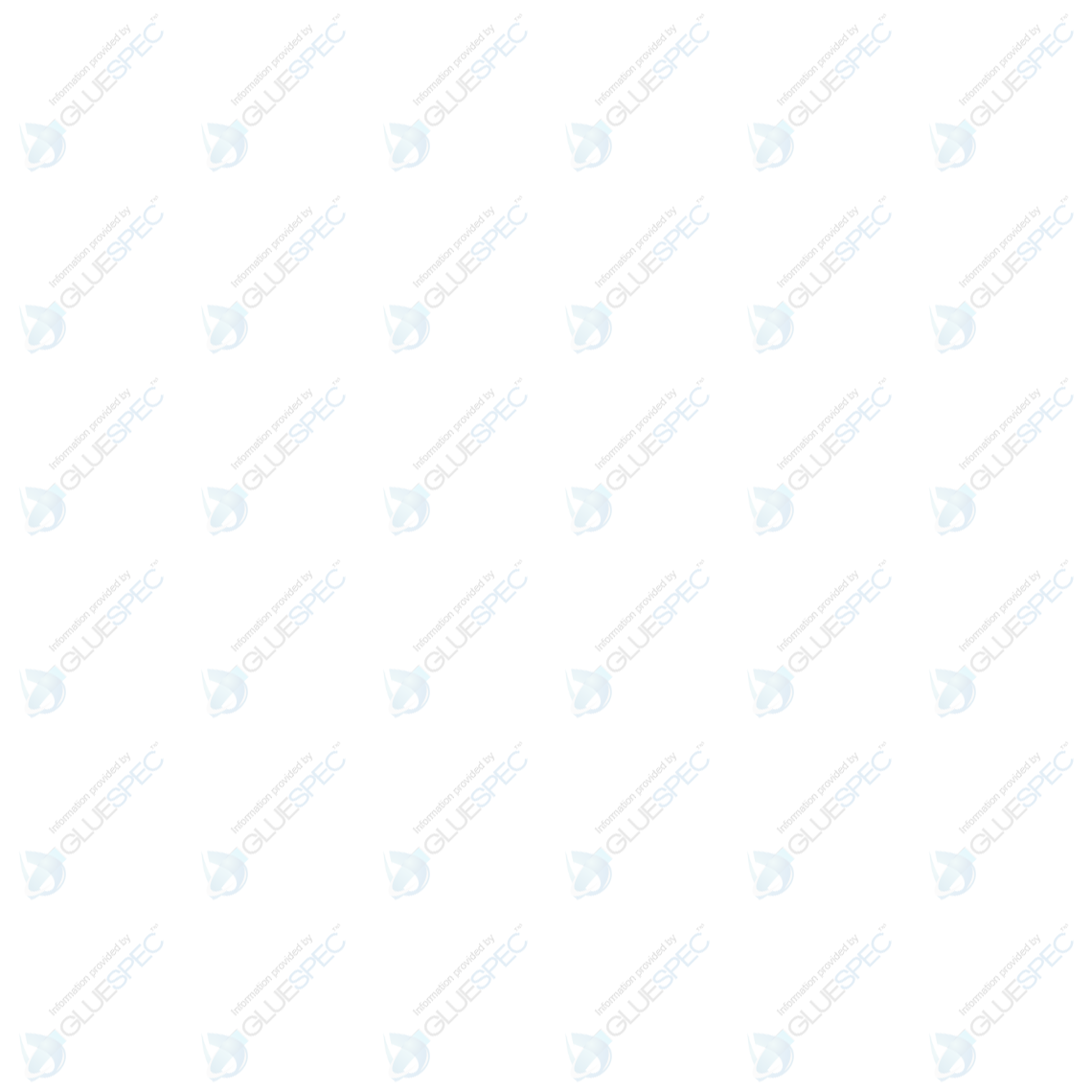
- Contributions by industrial experts with engineers in mind
- Focused on specialty-chemical material applications and selection
Knowledge Center
Designing the proper thermal management system into your high powered electronics / Q&A
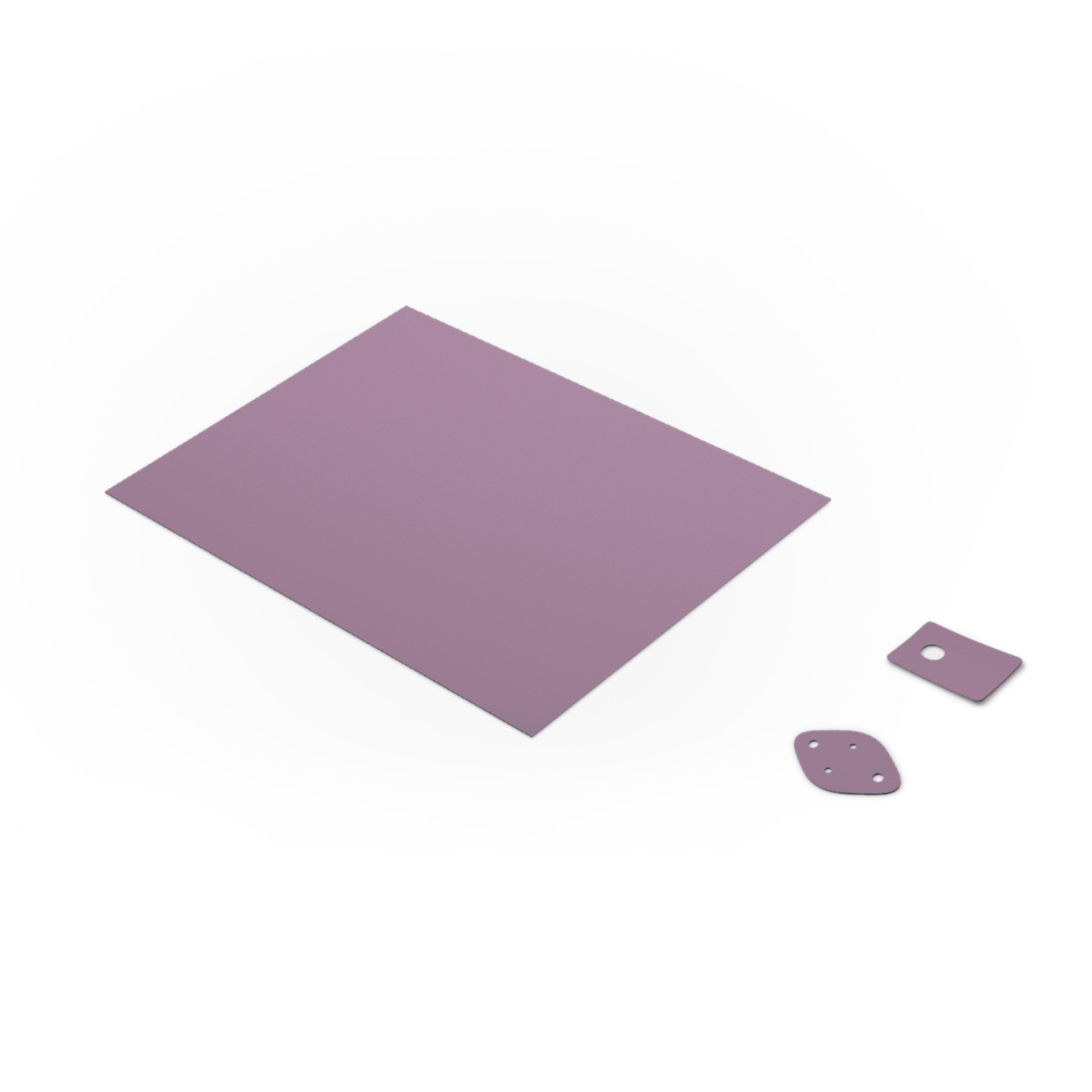
Thermal Management Q&A: Intro
Thermal management in electronics improves reliability and prevents premature failure. All electronic devices generate heat, and this heat must be moved, cooled, or otherwise dissipated. Metal heat sinks and electromechanical fans are a regular part of electronic designs, but many of today’s devices also need thermally conductive materials such as specialized adhesives. For design engineers who are looking for solutions, this Q&A from Gluespec® provides answers to frequently asked questions (FAQs).
Q: Why is heat such a problem with today’s electronics?
Heat has always been the enemy of electronics. What’s changed, however, is that today’s electronics are smaller, more powerful, and have densely-packed circuits. This includes but is not limited to 5G devices such as smartphones. Because power input determines heat output, high-power electronics of any type, such as those used in semiconductors and electric vehicles, require effective thermal management. If heat isn’t dissipated, electronics won’t meet specifications or can fail altogether.
Q: What are some types of thermal management materials?
There are several major categories of materials. Collectively, they are sometimes called thermally conductive materials or thermal interface materials (TIMS).
- Compounds, greases, and lubricants are traditional TIMS that do not cure, or dry, to a hard form.
- Thermally conductive adhesives and potting or encapsulating materials require curing and are usually made of epoxy or silicone.
- Mechanical attachment methods such as metal screws and heat-sink clips are probably the oldest forms of thermal management but they’re still used today.
- Gap pads, films, and gap fillers are used between heat-generating electronic components and heat sinks or other substrates.
Q: How are compounds, greases, and lubricants used – and what are some issues with them?
Compounds, greases, and lubricants create a thermally conductive layer between an electronic component and its thermal path, such as from a transistor to a heat sink. Because these materials lack adhesive properties, the component may require attachment. Mechanical methods are often used but they provide low thermal conductivity. Across many heating and cooling cycles, thermal expansion and contraction can pump-out the compounds, greases, and lubricants between a component and heat sink.
Q: Why would you use thermally conductive adhesives, pottants, or encapsulants?
Thermally conductive adhesives move heat and bond components to a heat sink or thermal path. Some products, such as silver-filled epoxies, also conduct electricity. Thermally conductive pottants and encapsulants dissipate heat and enclose the component for environmental protection against water, dust, and dirt. These materials can also provide intellectual property (IP) protection. In almost all cases, thermally conductive pottants and encapsulants are not electrically conductive.
Q: Is mechanical attachment only used with compounds, greases, and lubricants?
No. Mechanical attachment is also used with some gap pads to improve thermal conductivity. Otherwise, inadequate clamping pressure between two surfaces may cause thermal conductivity to drift. Mechanical attachment methods are also used in electronics applications that don’t need to conduct significant heat.
Q: What is important to know about gap pads, films and gap fillers?
Gap pads, films, and gap fillers conform to component and heat sink surfaces to ensure maximum contact for optimal thermal conductivity. Some are phase-change materials that, at their glass transition temperature, soften and flow into surface discontinuities. Unlike compounds, greases, and lubricants, these materials won’t pump-out and stay in place. Some support screen printing and, in the case of gap fillers, dispensing for very thin bond lines that improve heat transfer.
Q: What is thermal conductivity – and why it is important?
Thermal conductivity describes a material’s ability to conduct heat. Several different units of measure are used, but these are the most common ones:
- Watt/Meter-K
- BTU-Inch/Hour-Square Foot-°F
- BTU/Hour-Foot-°F
Thermal conductivity is the most common way to compare thermal properties during material selection. Because thermal conductivity is a measurement of the material alone and does not account for the thermal interface or other variables, it is a very useful comparison tool.
Q: What is thermal impedance – and how is it different than thermal conductivity?
Thermal impedance is the sum of a material’s resistance to heat and all of its contact resistances, which are specific to where the material meets the electronic component and the heat sink. When thermal impedance is lower, the material is a better thermal conductor. When a thermal resistance is higher, the material is less conductive and more resistant to heat flow. Unlike thermal conductivity, thermal impedance is an in-place measurement that needs to be tested for the specific application. Because it also accounts for material thickness, thermal impedance is sometimes more useful than thermal conductivity.
Q: Is there anything else design engineers need to know about thermal management?
Thermal conductivity and thermal impedance are both important, but they’re not the only specifications that design engineers need to consider during product selection. Surface profiles, roughness, clamping pressure, and the presence of other materials are also factors in thermal management. Thermal management selection can be complex, but the right choice can improve reliable and performance.