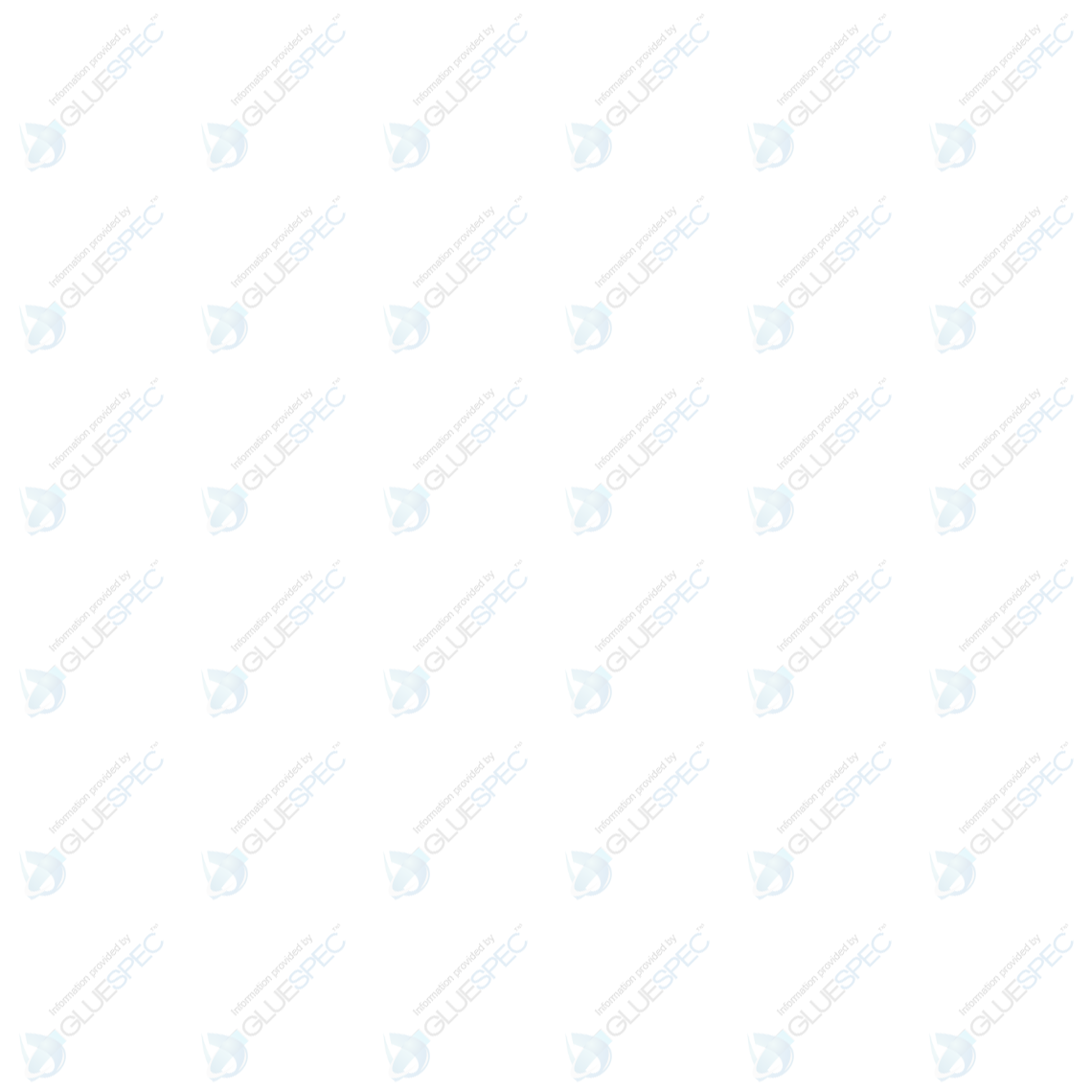
- Contributions by industrial experts with engineers in mind
- Focused on specialty-chemical material applications and selection
Knowledge Center
Polysulfides in the Aerospace Industry
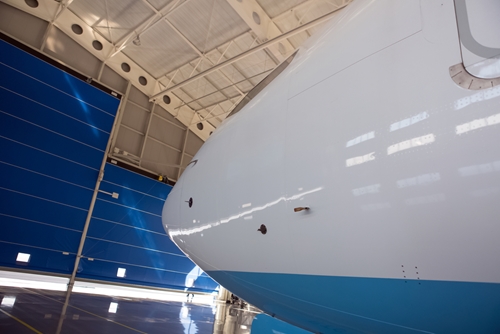
Polysulfide Adhesives and Sealants for Aerospace Assembly
Polysulfide adhesives and sealants for aerospace assembly are used to seal fuel tanks, fuselages, and windshields. They're also used to fill gaps between floor panels. They work well with aluminum, stainless steel, and composites and provide low-temperature and flexural resistance.
Aerospace is a demanding industry for adhesives and sealants. Materials used in aircraft construction must meet stringent regulations and also be able to withstand the rigors of extreme and variable environments. Polysulfide sealants have been a go-to in the aerospace industry for fuel tank, windshield and other sealing applications because of their durability and low temperature flexural resistance. There are both one part moisture cure and two part catalyst cured types, the two parts are commonly used in Techikit or Semkits and also in a pre-mixed frozen format.
Advantages of polysulfide adhesives for aerospace
Polysulfides have a number of properties that make them advantageous for use in aerospace manufacture. Importantly, they are highly resistant to jet and other fuels so they can be used to seal fuel tanks. They are also a good dielectric material, so they can be used for potting or sealing electronic components within tanks as well. Flexibility when cured allows polysulfides to withstand vibration, joint movement and impact experienced in travel. Polysulfide sealants are also resistant to thermal cycling and can withstand temperatures in the -80F to 250F range.
In addition to fuel tank applications, polysulfides find use in general fuselage sealing such as in gap filling between floor panels. They adhere well to materials used in aerospace manufacture including aluminum stainless steel and composites.
Polysulfides are the sealant of choice for many aerospace applications. Other adhesives and sealants usually can't match the combination of fuel resistance, adhesion and flexibility polysulfides offer. Modern formulations are also quite lightweight - allowing them to contribute to overall weight reduction in construction. Application is simple with brushing or troweling - meter-mix and pre-mixed packaging is also available.