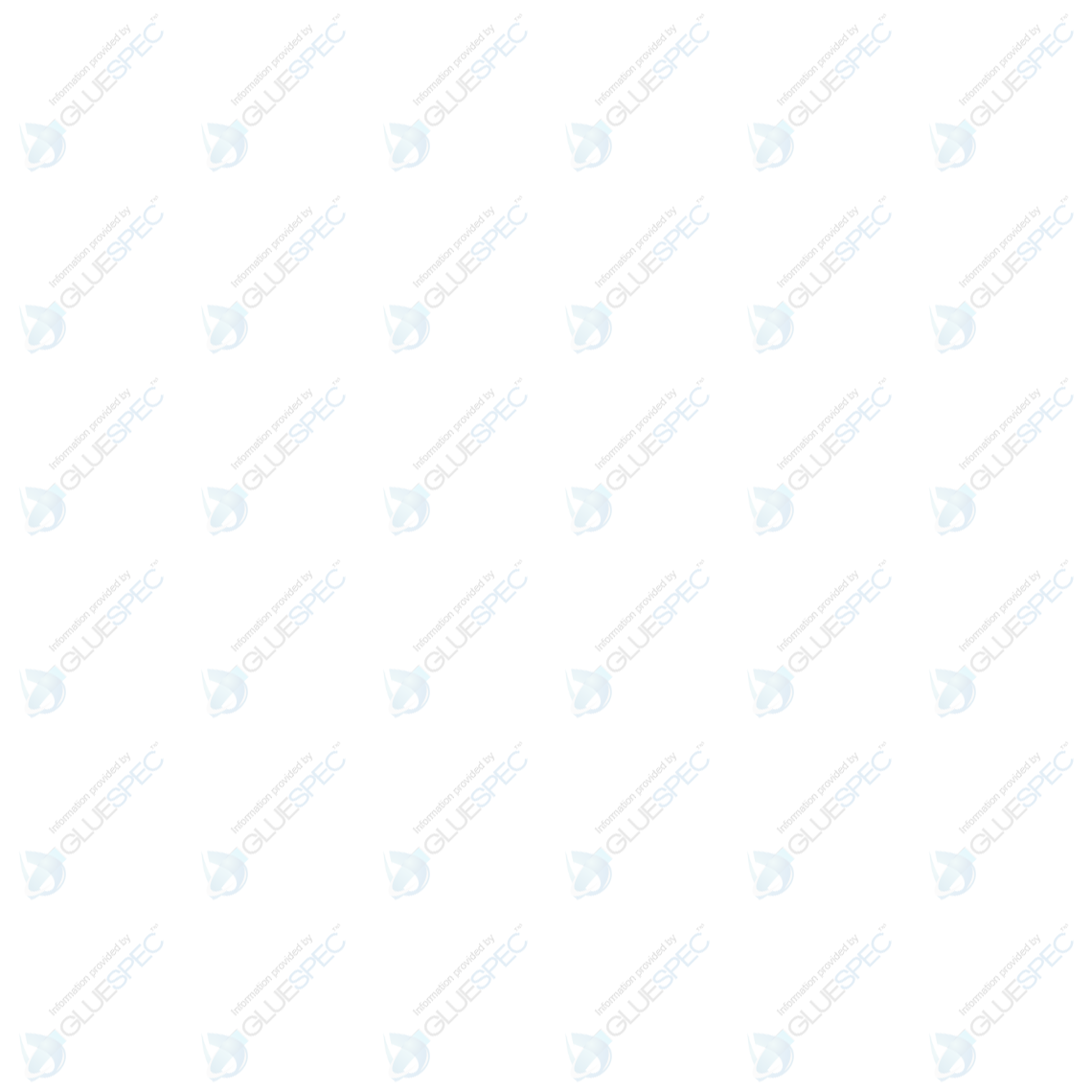
- Contributions by industrial experts with engineers in mind
- Focused on specialty-chemical material applications and selection
Knowledge Center
Hot Melts in the Appliance Industry
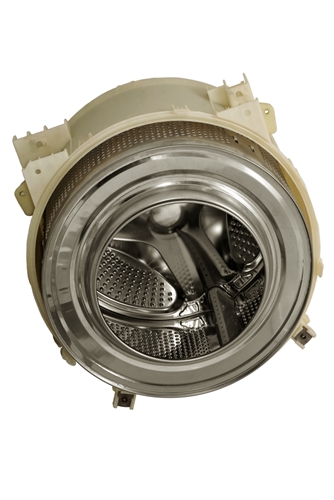
Hot Melt Adhesives for Appliance Manufacturing
Hot melt adhesives for appliance manufacturing are used in the paneling and assembly of washers and dryers, refrigerators, air conditioners, dishwashers, and other white goods.
The use of adhesives in the appliance industry has been rapidly gaining ground as manufacturers look to lower costs and increase production speeds. Replacing mechanical fasteners with glues can allow for faster, in-line production and reduce part inventories while allowing improved aesthetic appearance. Hot-melt adhesives (HMAs) in particular can be an excellent alternative. These adhesives are relatively inexpensive and can be easily integrated. New formulations offer excellent bonding properties and long-term resistance to wear.
Advantages of hot melt adhesives
Hot-melt adhesives, as their name suggests, are heated into liquid form for application, and bond surfaces quickly as they cool. They are made of a thermoplastic resin that adheres well to a number of both porous and nonporous surfaces. Because they don't require solvent evaporation they eliminate concerns over VOCs inherent with other adhesives. Bonds are formed more quickly than traditional chemically curing adhesives, like epoxy, and require minimal pressure and clamping time. HMAs also don't shrink during curing, so they can be used in gap-filling applications, allowing for larger tolerances in part manufacture.
"HMAs offer good resistance to vibration and impact, and specific formulations also offer resistance from moisture and chemicals."
HMAs are ideal for integration into assembly line manufacture. They are sold in a variety of sizes, from individual application, to bulk quantities of solid pellets or sticks. They have an excellent shelf-life and can be simply loaded into melting apparatus when needed. These melters range in size from 15 to 100 liter tanks, and can be attached to multiple hand-held or automated dispensers. Because they don't require clamping, HMAs can be applied in-line.
Advanced properties of HMAs
New formulations have advanced beyond the traditional Ethylene Vinyl-Acetate (EVA) compositions that formed the basis of early HMAs. Even EVA hot-melts have been improved by the addition of tackifiers, waxes and other additives that alter and improve open times, adhesion and cured properties. Flexibility and heat resistance can all be improved with new HMA technology. Other base-compounds can provide further advantages, particularly in the appliance industry. Polyolefin (PO) HMAs in particular can provide excellent adhesion to polypropylene, and offer better resistance to moisture and chemicals. This makes them well-suited to adhesion tasks on washers and dryers, as well as washing machines. Polyamide formulations also offer good adhesion to polypropylene, as well as ABS and polyethylene.
Polyamides have excellent temperature resistance and can withstand temperatures up to 160C. Reactive urethane hot-melts are another new area that allows for application at lower temperatures (around 250F) for heat-sensitive surfaces that wouldn't ordinarily be able to withstand the 400F temperatures needed for other hot-melts.
Applications for hot melt adhesives in appliance manufacturing
In general, HMAs provide an excellent option for all types of appliance manufacture. They can be applied quickly and reliably by a range of manual and automated methods. HMAs offer good resistance to vibration and impact, and specific formulations also offer resistance from moisture and chemicals. Paneling and assembly of washers and dryers, refrigerators, air conditioners, dishwashers and other white goods can be improved with the proper use of hot-melt adhesives which reduces assembly time while increasing aesthetic appearance.