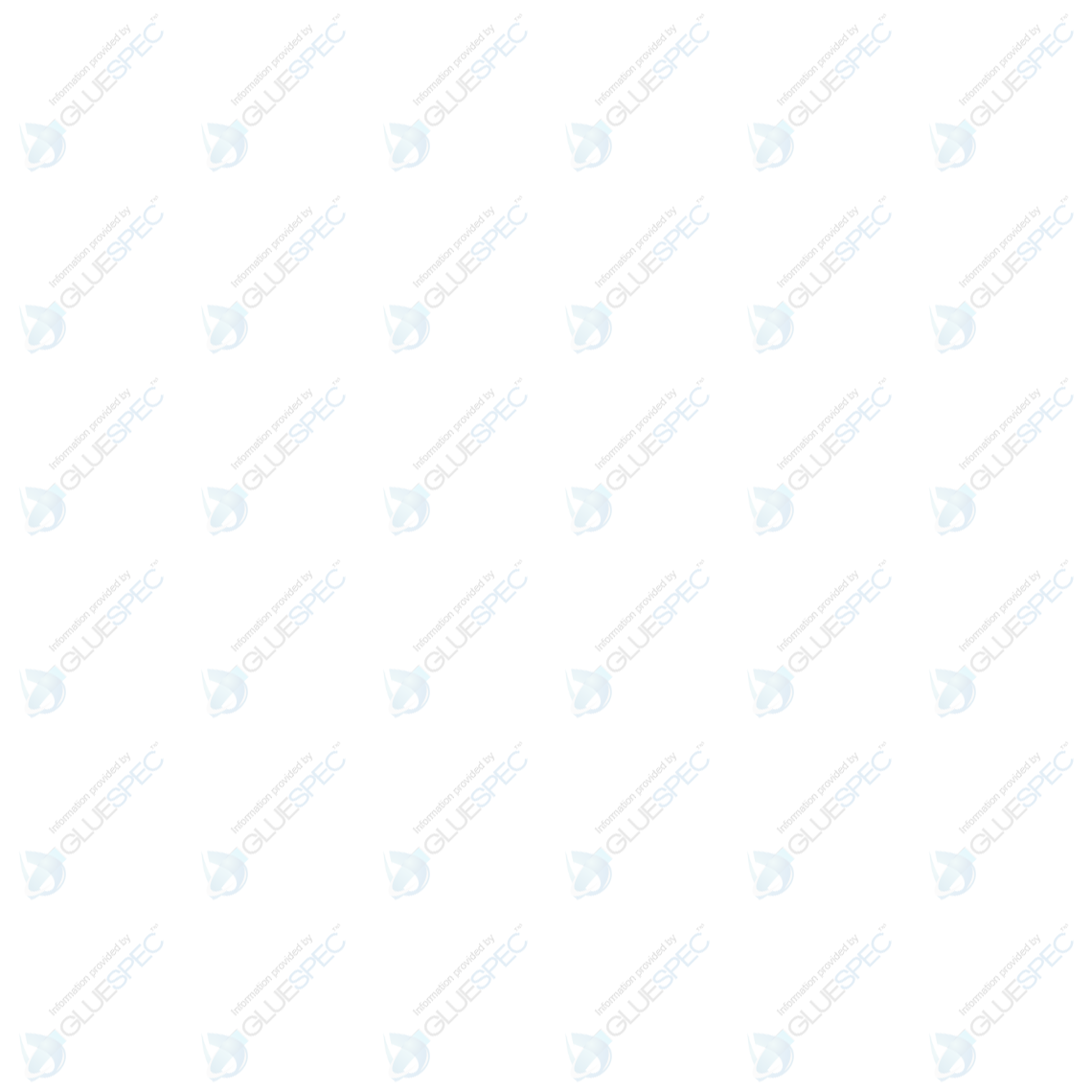
- Contributions by industrial experts with engineers in mind
- Focused on specialty-chemical material applications and selection
Knowledge Center
Urethanes in the Photovoltaic Solar Industry
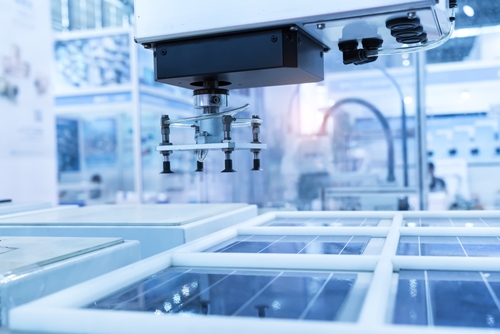
Urethane Adhesives in the Solar Industry
The solar industry has experienced an enormous boom in the past decade, thanks to advances in technology and financial incentives. Reduction in the cost of panels has come from advances in solar cell design, but also modern methods of construction and installation. Adhesives have played a major role in modern photovoltaic (PV) construction because they provide lighter, cheaper, longer-term alternatives to mechanical fasteners and can meet the unique challenges of the solar field. Special classes of urethane adhesives are used across the PV industry for their excellent bonding properties, and resistance to ultraviolet (UV) degradation.
What are urethane adhesives?
Urethane adhesive are either one- or two-part formulations that cure to a tough, flexible bond. One-part systems cure via moisture - usually the ambient moisture in the air and on surfaces is sufficient, and often can be handled after 30 minutes, reaching full strength in 8-24 hours. These one part systems are not UV stable and would only be used in covered areas. Two-part systems cure chemically, and don't require air or surface moisture, though they need to be mixed thoroughly, often in a 1:1 ratio. Urethanes are also used frequently as the adhesive or core in high-strength structural bonding tapes. Urethane adhesives are prized for their flexibility in formulation - altering characteristics of urethanes like open-time, flexibility or rigidity of bonds, bond strength and resistances are all possible. They bond well to a wide range of materials and can bond dissimilar materials, including composites and fiber-reinforced plastics (FRP), as well as most rubbers, plastics, wood and metal.
"Non-yellowing urethanes can last upwards of 10 years without any significant reduction in transparency."
The cured properties of urethanes are also uniquely versatile. They can be either flexible or rigid, and can be used in high-strength foam tapes as well. Urethanes are also resistant to cold temperatures, retaining that flexibility and other cured properties in below-freezing temperatures where some adhesives become brittle. Because of their trademark flexibility, urethanes also offer excellent impact resistance moisture and chemical resistance are another hallmark of urethane adhesives, allowing their use in outdoor applications.
How are urethane adhesives used?
Urethane adhesives are used in a number of areas of PV construction. Because of their excellent resistance to UV radiation, they can be used as top coat over PV cells. Other adhesives and encapsulants, like epoxy, have a tendency to yellow over time, reducing the ability of light to penetrate to the cell, and thus overall efficiency. Non-yellowing urethanes can last upwards of 10 years without any significant reduction in transparency.
Urethanes are also used in PV bonding applications, like attaching and sealing panel frames where their UV and weather resistance makes them an excellent choice. They are also employed frequently as adhesives for mounting and potting junction boxes (J-boxes), where they can withstand both weathering and physical stress. Urethane adhesives are also frequently in backsheet laminating, where their resistant properties, along with the protective sheet, provide protection to the sensitive electronics on the underside of panels.
Because of their excellent bonding strength and resistance to the elements, urethanes are being used for rooftop installations, sometimes directly on existing roofing material. This method reduces cost and weight of large structural supports, as well as making installation easier. Urethane-based structural bonding tapes can be used for this application along with other formulations.