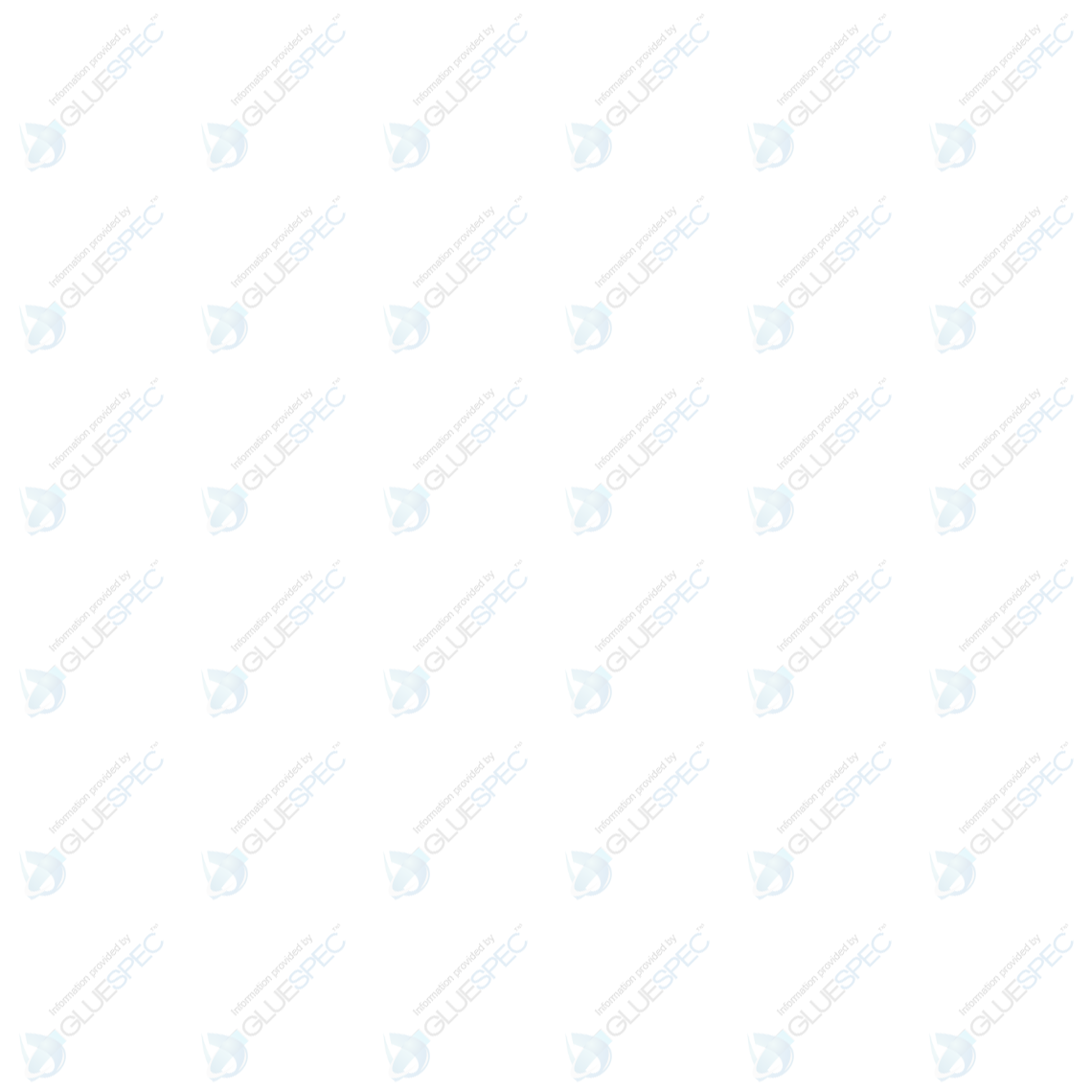
- Contributions by industrial experts with engineers in mind
- Focused on specialty-chemical material applications and selection
Knowledge Center
DC100 MAX High Precision Dispenser Q&A
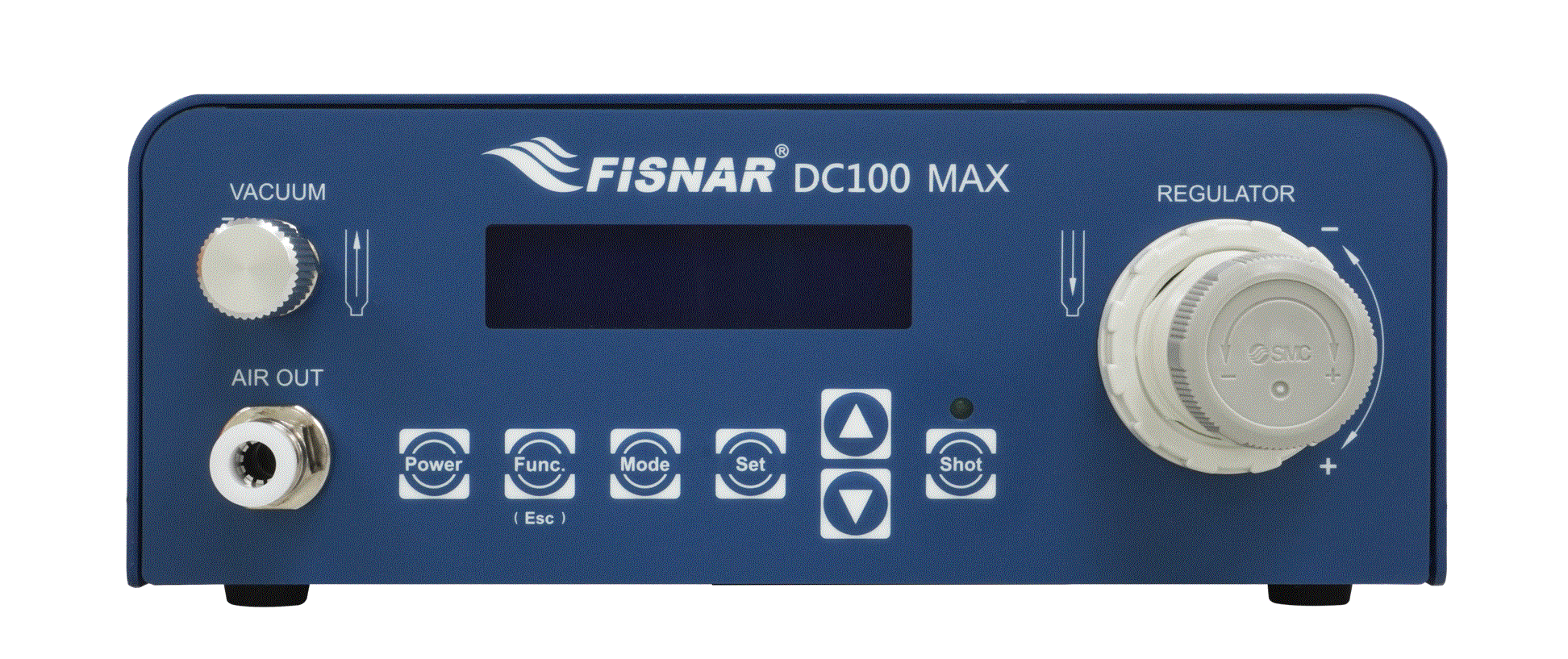
Fisnar’s DC100 MAX High Precision dispenser is designed to achieve high levels of process stability in fluid dispensing applications. Gluespec asked Robert Campbell, Fisnar’s Global Product Manager, about this benchtop unit and how its precision, functionality, and connectivity are helping manufacturers to improve production. Fisnar launched the DC100 MAX in 2023.
Why is high precision important in dispensing liquid adhesives?
Industrial electronics, mobile electronics, and medical wearables keep getting smaller. There are now smartphones that can fit in your pocket and hearing aids so small that they’re barely noticeable. When dispensing liquid adhesives, manufacturers need a way to deposit smaller shot sizes onto substrates like printed circuit boards (PCBs). These microdots require greater precision.
Are reductions in shot size the only thing that’s driving demand for precision?
No. Adhesives are using advanced chemistries and becoming more complex, more expensive, and more difficult to dispense. Manufacturers need to dispense these fluids reliably and consistently while reducing material waste and improving customer yields. Let’s say you want to dispense a volume of 0.1 cubic centimeters (cc) ±3%. In this case, a basic dispenser with shot sizes of ±10% cannot achieve this.
What’s an example of an adhesive you’d like to highlight?
Increasingly, design engineers are specifying conductive adhesives that contain specialized fillers. These adhesives can be electrically conducive, thermally dissipating, or both. The chemistry of an adhesive like silver-loaded epoxy is complex, and precious metals are expensive. With their high viscosity and large filler particles, conductive adhesives like this are also challenging to dispense.
How is the DC100 MAX able to achieve a high degree of precision?
The DC100 MAX uses a high-precision regulator and a fast-acting solenoid. These integrated components provide high accuracy, robust capabilities, and exceptional results. By carefully controlling the flow of compressed air to the syringe barrel, the DC100 MAX can achieve a very accurate deposit size. The stability of the flow rate and the repeatability of this flow are critical.
How do the regulator and solenoid work together?
When external compressed air is supplied to the machine, the regulator ensures that the pressure inside the unit remains constant and doesn’t drift. When the machine is actuated, it opens the valve at the same speed every time. This allows air to flow into the syringe’s barrel, which closes at a rapid rate and with a high degree of repeatability. Using an industry-best regulator and solenoid makes this possible.
In terms of capabilities, what’s especially noteworthy about the DC100 MAX?
The DC100 MAX can adapt and change its dispensing parameters to maintain a consistent shot size over the course of a working shift or a batch of parts. That’s important because of a phenomenon known as “full-to-empty syndrome”, and because the viscosity of a liquid adhesive can change over time. Users also like the control and calibration that the DC100 MAX provides.
What is “full-to-empty syndrome” and how does it affect dispensing?
During dispensing, the syringe that’s used contains liquid adhesive and air. Remember that air is compressible, but that fluids are technically incompressible. As liquid adhesive is dispensed from the syringe, the volume of air increases. In other words, there’s now a larger amount of air to compress for the next shot, which affects the volume of material being dispensed.
How does the DC100 MAX let users control changes in dispensing time?
The DC100 MAX lets users change this parameter incrementally or on the fly, and by either total elapsed time or shot count. Typically, shot count is used. Let’s say there are 100 shots in a syringe. The user could adjust the dispense time as needed, or have the unit automatically adjust this parameter every 10 shots to account for differences caused by “full-to-empty syndrome”.
How does the unit let users account for changes in a liquid adhesive’s viscosity?
Liquid adhesives that undergo changes in viscosity usually thicken over time. Temperature is also a factor, and a manufacturing facility may be considerably warmer or cooler depending on the time of day or the season. By adjusting the dispensing parameters, a user can change the time vs. viscosity curve into a straight line. Mathematically, increasing the dispensing time accounts for the increase in viscosity.
What about calibration?
The machine’s pressure gauge can be calibrated to an atmospheric pressure. This is important if you need to run the same manufacturing process at different geographic locations due to the changes in atmospheric pressure. In turn, this promotes consistency in globally distributed manufacturing while allowing equipment to be moved and then fine-tuned.
Why is connectivity important when dispensing liquid adhesives?
Manufacturers want real-time feedback, machine-to-machine (M2M) communications, and the ability to control dispensers from a human-machine interface (HMI). This requires connectivity and communications. The DC100 MAX has an I/O interface for data exchanges and can be remotely controlled. It uses MODBUS, a client/server protocol, for M2M communications.
Does the DC100 MAX have any other connectivity functions?
An operator can attach a barcode scanner to the DC100 MAX. Then, instead of choosing when to dispense material or which program memory address to use, the operator can simply scan a barcode. This user-friendly feature changes the unit’s parameters while preventing the operator from making a mistake. In turn, eliminating human error reduces part rejects.
What type of production environment is the DC100 MAX designed for?
This machine can be used on either a single-piece-flow production line that’s operator-controlled, or with batch processing. Although the unit is not designed for fully automated production, there is support for automation. Manufacturers can connect the DC100 MAX to an industrial robot or integrate it with an advanced robotics system or other automated machine environment.
What are some additional features and benefits?
The DC100 MAX is largely maintenance-free. It’s also multi-lingual and uses a power supply that’s compatible with the different voltages and currents that are used worldwide. That’s important if you need to move a machine from one country or continent to another. Customers also like how they can quickly transfer machine/program memory parameters from one DC100 MAX to another.
What is the target market, and how can the DC100 MAX help Gluespec users?
Manufacturers of all sizes can use the DC100 MAX. Graduate-level researchers and startups that are building products also need the ability to dispense adhesives with precision. Design engineers who visit Gluespec during a project’s spec-in and prototyping phases will like how this unit uses adhesives that are packaged into small-capacity syringes and cartridges instead of large pails or containers.