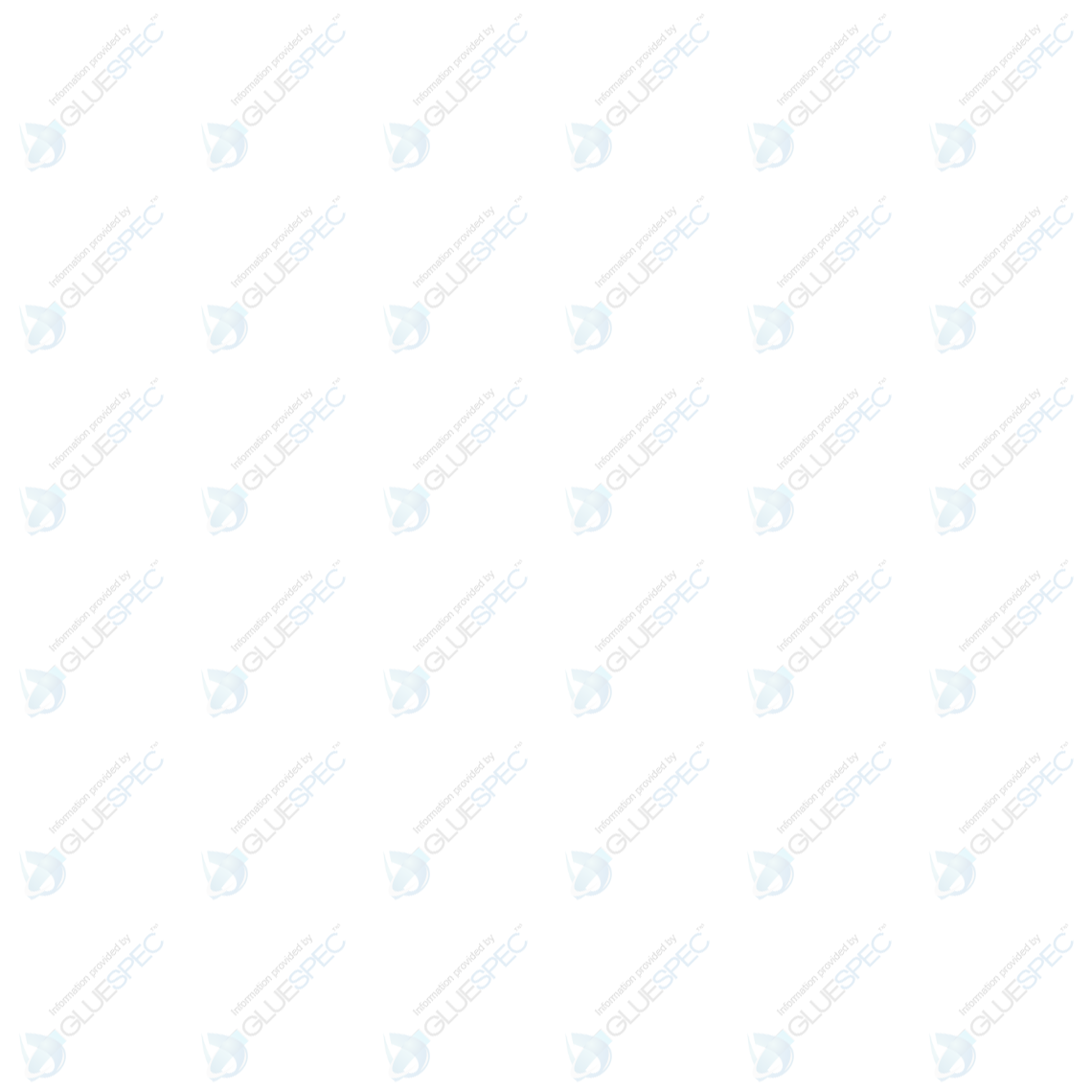
- Contributions by industrial experts with engineers in mind
- Focused on specialty-chemical material applications and selection
Knowledge Center
An Overview of Fluid Dispensing Systems & How They’re Used
Fluid Dispensing Systems
There are copious amounts of fluid dispensing options to choose from, and determining which one is right for your project can reduce waste, as well as guarantee efficiency. Products ranging from manual handheld applicators to dispensing controllers and meter mix systems can assist you with dispensing a range of materials. Whether you’re working with adhesives, lubricants or sealants, there is a dispensing system out there that will provide the ideal end result. What is important is that you have both the flexibility and accuracy to successfully complete the task in the fluid management process.
Fluid Dispensing: What is it Used For?
Typically, fluid dispensing is used to apply adhesives, but it can also be used for dispensing specialty chemicals. There are applications of fluid dispensing in almost every industry, which explains why there is such a wide range of approaches. Which method you use depends on what materials you’re working with, and what you anticipate for the end result. For example, hot-melt handheld dispensers — also known as hot glue guns — are an example of fluid dispensing and can be used at home for craft projects or quick fixes. This method uses a mechanical trigger to push cylindrical sticks of thermoplastic adhesive through the dispenser and is melted by a continuous-duty heating element within the dispenser.
For a more precise application process, there are dispensing tips (otherwise known as dispensing needles). These are varied, coming in different styles, sizes, and materials. Tapered needles promote flow, which makes them useful for thicker fluids. The tapered tips allow for faster deposits of thick fluids as opposed to standard tips. Stainless steel tips are more effective in terms of precision, while flexible tips are also available for hard-to-reach areas.
Fluid dispensing systems can be segmented into industries. The most common consist of electronics assembly, construction, medical devices, and transportation, but it is not limited to these.
For more automated approaches to fluid dispensing, there is machinery available that offers precise and controlled methods of application. Dispensing controllers are valuable for microdot deposits, creating lines, and doing large potting and filling. Valves are used either with automated robots or dispensing controllers and commonplace in dispensing specialty chemicals. While like most dispensing methods, it is dependent on certain variables (like the type of adhesive, and the amount) there is a range of valves available depending on the task. For example, there are diaphragm, needle, pinch tube, poppet, and positive displacement valves available.
If you’re looking to be able to blend materials, like adhesives and specialty chemicals, meter mix systems are necessary to get the job done. Not only are they valuable for precise control but they are also useful for working with single and multiple component materials like epoxies, polyurethanes, silicones and acrylics. Depending on your workspace and needs, these are available in benchtop, cart-mounted or full workstation varieties.
Lastly, there are robots for truly automated dispensing options that can be brought into assembly lines in high production environments.
Mass Flow & Volumetric Flow: Explained
For accurate distribution of materials through fluid dispensing, it is important to understand both mass flow and volumetric flow.
Mass flow measures the number of molecules in a flowing gas. Mass flow rate measures the number of molecules flowing through an instrument, regardless of the space that the molecules take up, says Alicat.
Volumetric flow measures the space that the molecules occupy. It’s important to note that because gasses are compressible, the volumetric flow rates will change with the change of temperature and/or pressure. Volumetric flow rate is a measure of the 3-dimensional space that gas occupies as it goes through the instrument, with specific, measured temperature and pressure conditions (it can also be known as actual flow rate).
If you’re deciding between using mass flow or volumetric flow, you should consider:
- Mass flow measurement is most useful when the number of molecules needs to be measured. Gas mixing applications work best when mass flow is being measured, so that separate gases remain relative to each other.
- Volumetric flow should be measured when monitoring the parts of a gas stream under their actual conditions. If you’re looking to quantify the number of particles within the volume of air, volumetric flow is recommended.
Overall, the choice of what fluid dispenser to use is dependent on your industry and your materials. Making the right decision can determine efficiency and accuracy, however, so it is important to consider all aspects of the production process. The investment in more precise dispensing equipment will be cost-effective in the long-run for your company if they’re willing to upgrade equipment to create a reliable system.