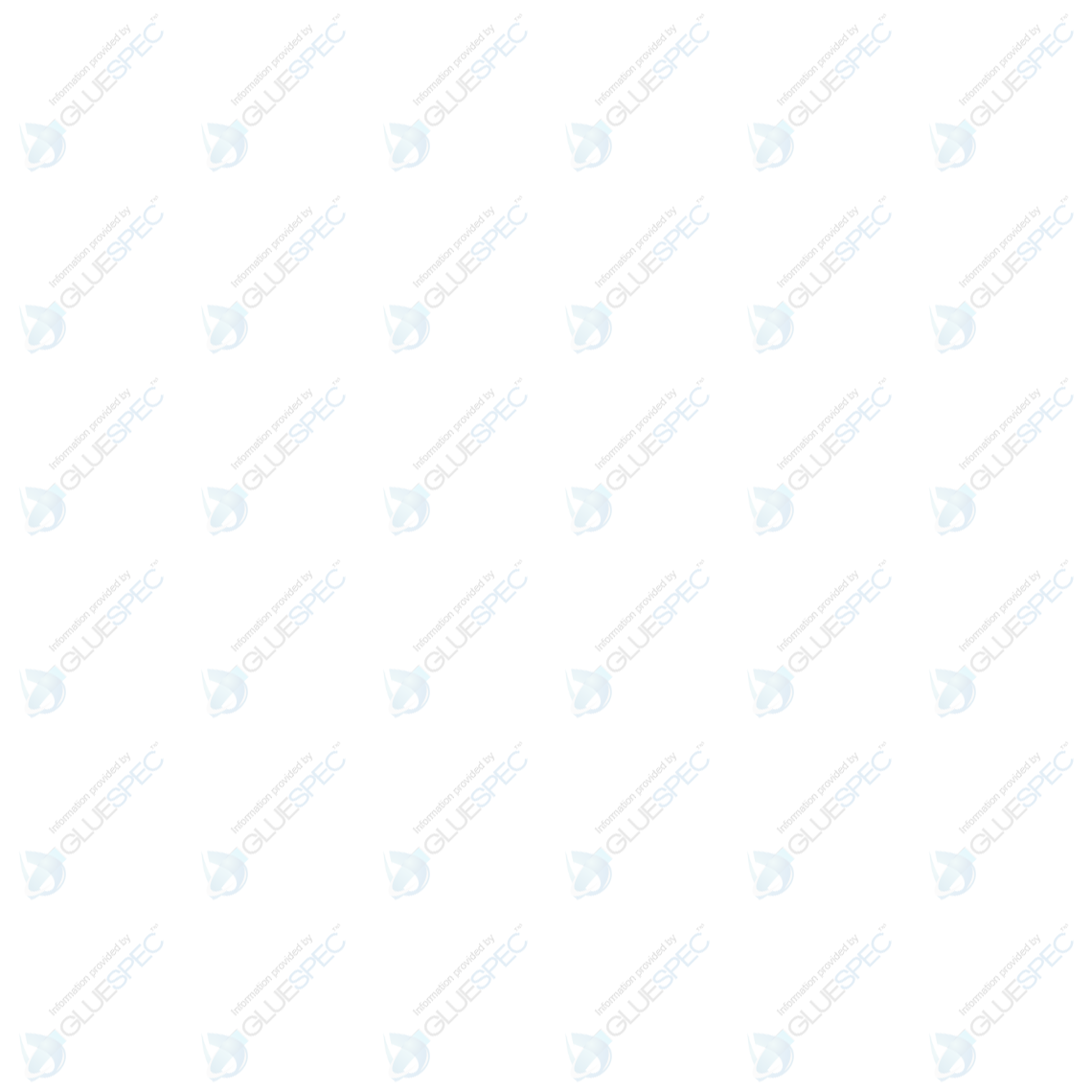
- Contributions by industrial experts with engineers in mind
- Focused on specialty-chemical material applications and selection
Knowledge Center
Plastic Bonding with Adhesives - Considerations Q&A
Plastic bonding uses adhesives instead of fasteners to join plastic substrates together. These substrates can be made of the same type of plastic, or they can be made of different types of plastic. Bonding can also involve joining a plastic substrate to a non-plastic material. For design engineers who are looking for the right solution, this Q&A from Gluespec® provides answers to frequently asked questions (FAQs).
Q: What do designers need to consider when choosing an adhesive for plastic bonding?
Designers need to ask and answer the following questions:
- --Which material or materials do you want to bond?
- --What is the surface energy of the substrate?
- --What is the end-use application?
- --What is the application environment, including stresses on the joint?
- --How is the adhesive applied and the product assembled?
- --Are there appearance-related requirements?
- --Is there sufficient bond area to assure an adequate bond for the application?
The following sections examine these questions in detail. This Q&A also considers how some common types of plastics are bonded, and which types of adhesives are used.
Q: Which material or materials do you want to join with plastic bonding adhesives?
There are many different types of plastics, and each one has different material properties. During adhesive selection, engineers need to select a product that will adhere to the specific type of plastic or, in the case of dissimilar materials, two different plastics or the plastic and the non-plastic material. The surface energy of the substrate is a key material property, but the application is also important to consider.
Q: What is the surface energy of the substrate?
Surface energy affects how an adhesive is attracted to the substrate, and how the adhesive will spread out, or wet out, after it is applied. As a rule, adhesives stick more readily to plastics that have a higher surface energy. Conversely, materials with a lower surface energy are more difficult to bond. Surface energy is measured in dynes, and dyne levels are usually tested with dyne pens. Materials with a surface energy below 36 dynes may require special treatments to increase their surface energy.
Q: What is the end-use application for the plastic bonding adhesives?
Plastic bonding adhesives are used in electronics, mechanical systems, medical devices and equipment, optics and electro-optics, transportation, and in structural applications. For example, electronics manufacturers need adhesives for printed circuit boards (PCBs) and integrated circuit (IC) packaging. Medical manufacturers need solutions for wearables and surgical instruments. Electric vehicle (EV) manufacturers need plastic bonding adhesives for assembling EV batteries.
Q: What is the application environment, including stresses on the joint?
Plastic bonding applications vary considerably, even within the same industry. For example, in the transportation industry, the adhesives used with aerospace nose cones need to withstand different stresses than the sunroofs on cars. Adhesives for EV battery compartments need to withstand higher temperatures than the products used with automotive interiors. EV adhesives may also need to support plastic-to-metal bonding and have flexible joints that won’t crack because of temperature-related stresses.
Q: How is the plastic bonding adhesive applied and the product assembled?
Manufacturing processes play a role in adhesive selection. Specifically, design engineers need to consider the time that’s required to apply a plastic bonding adhesive and the time it takes to assemble the product. This determines the open time, which is the time an adhesive can be used after it’s mixed and/or applied. Cure time, cure method, and temperature also are also important to consider because they affect cycle times, equipment requirements such as UV lights or ovens, and energy usage.
Q: Are there appearance-related requirements?
Some plastic bonding applications satisfy requirements for color or clarity. For example, the optically clear adhesives that are used with displays cure so that they are transparent. These adhesives also have high haze resistance and less yellowing. Plastic bonding adhesives are also available in colors such as black, red, and white so that they match a larger product or are easier to identify during assembly.
Q: How do you bond ABS or acrylic?
ABS and acrylic support the use of many adhesives, so the application specifics are especially important to consider. Epoxy adhesives provide superior chemical resistance, but acrylics and light-cure acrylics combine good chemical resistance with durability. Cyanoacrylate adhesives form strong bonds but have poor resistance to chemicals and water. With their lower peel strength, cyanoacrylates may not be able to withstand the peel stress that can occur on one edge of a bond area.
Q: How do you bond acetal?
Acetal, a type of plastic that includes Delrin®, can use structural acrylic adhesives to form strong, water-resistant bonds. Epoxy adhesives provide the best chemical resistance, however, and they also offer higher temperature resistance. Cyanoacrylate adhesives with a primer may be an option with acetals if water resistance is not required.
Q: How do you bond polyimide?
Epoxy adhesives work well with polyimides such as Kapton®. These plastic bonding adhesives provide durable bonds and can withstand the high heat and exposure to chemicals that are common to applications involving polyimides. Cyanoacrylate, light-cure acrylic, and urethane adhesives are also used to bond these materials.
Q: How do you bond polypropylene and polyethylene?
These plastics are difficult to bond because they both have low surface energy. However, there are two-part specialty acrylic adhesives that provide strong, fast, and durable bonds with temperature resistance up to 150° C. These adhesives also offer good chemical resistance and can eliminate the need for using primers or applying flame, corona, or plasma treatments to the substrate. For lower temperature applications without chemical or water exposure, cyanoacrylate adhesives with a primer can be used.
Q: How do you bond polyurethane?
Cyanoacrylate, acrylic, light-cure acrylic, and urethane adhesives are all used to bond polyurethane. Epoxies are a good choice for applications where there is chemical exposure, however. With flexible grades of polyurethane, bond flexibility is important to avoid joint cracking. Newer cyanoacrylate grades that are more flexible may be the best choice here.
Q: How do you bond PVC?
PVC plastic supports the use of many different types of adhesives. In applications without water or chemical exposure, cyanoacrylates can be used. Acrylics, light-cure acrylics, and epoxies can also provide strong, robust bonds with PVC. As this Q&A from Gluespec demonstrates, design engineers need to consider both the type of material and the application specifics to select the optimal adhesive.