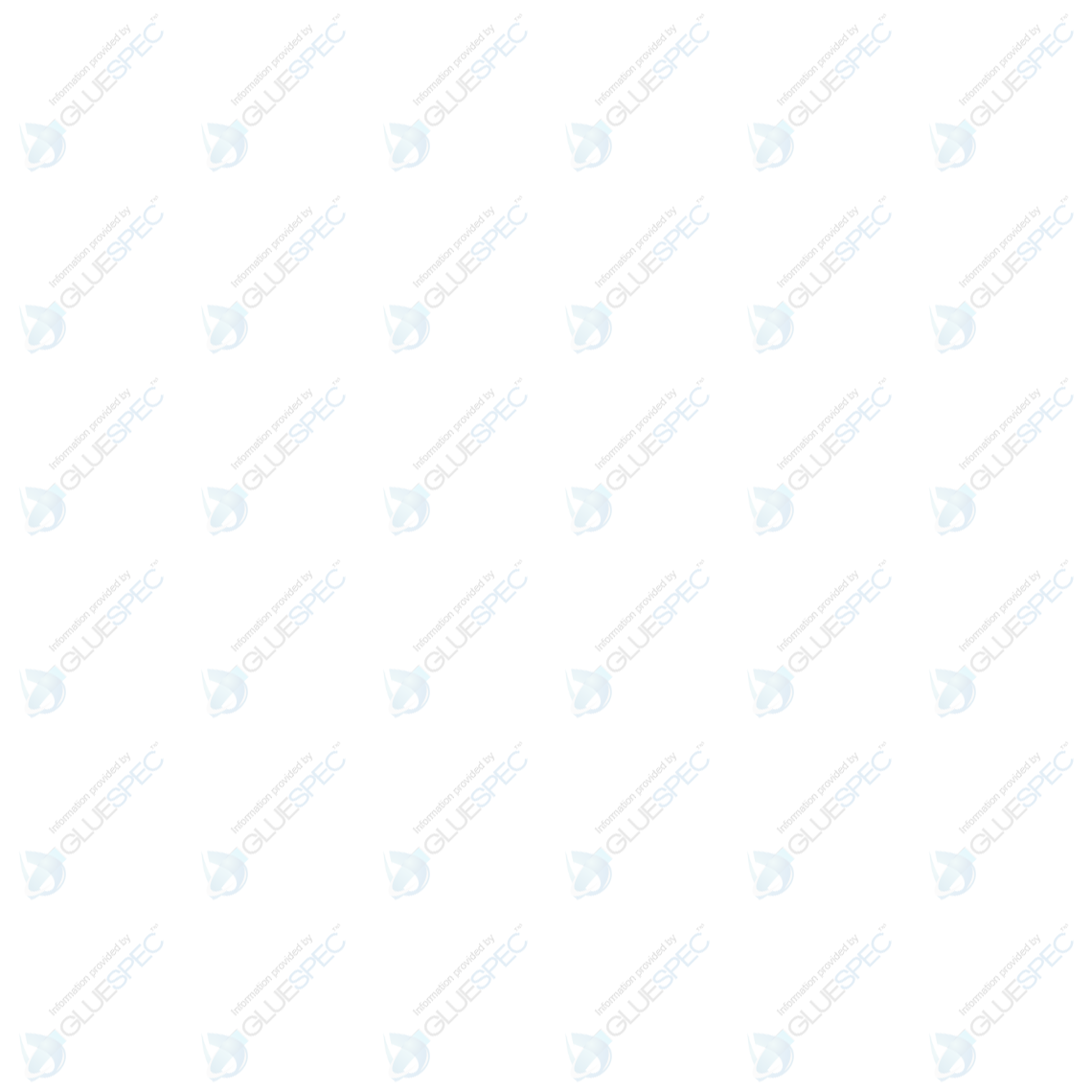
- Contributions by industrial experts with engineers in mind
- Focused on specialty-chemical material applications and selection
Knowledge Center
In Depth Questions and Answers on UV/Light Cure Adhesives
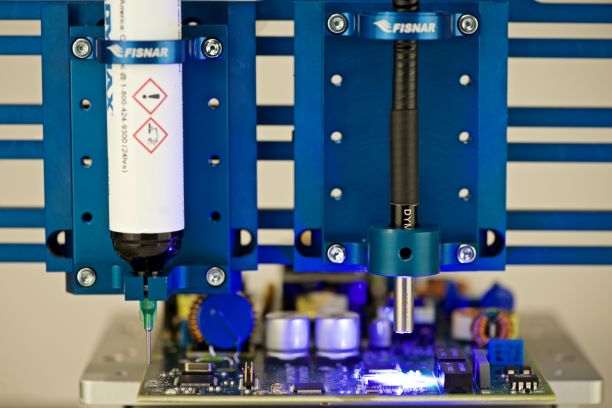
UV/Light Cure Adhesives Q&A
Industrial adhesives that cure with visible or ultraviolet (UV) light form fast, strong chemical bonds between substrates. Visible light curing adhesives are becoming increasingly popular, and demand for UV cure adhesives is projected to grow steadily. For design engineers who are considering these products, this Q&A from GlueSpec® provides answers to frequently asked questions (FAQs).
Q: How do UV/light cure products compare to other industrial adhesives?
A: Unlike heat cure adhesives, UV/light cure adhesives do not require ovens for curing, the chemical process by which an adhesive attains its final properties, including strength. Instead, lamps that produce specific wavelengths of light are used. UV/light cure adhesives are also free of solvents and available in one-part formulations that do not require time-consuming mixing. Some UV-curing adhesives are formulated with a secondary moisture-curing mechanism for “shadowed” areas that aren’t reachable by the UV lamp. In this sense, they have some similarities with moisture-cure adhesives.
Q: What are some advantages of UV/light cure adhesives?
A: The main advantages are reduced energy consumption, faster assembly times, low levels of volatile organic compounds (VOCs) for fewer environmental health and safety (EH&S) concerns, and the ability to form flexible, stress-absorbing bonds between similar or dissimilar substrates. UV/light cure adhesives also allow for the proper alignment of components before bonding, which typically occurs in seconds. In addition, it’s easy to scale-up production by adding more lamps to an assembly line.
Q: What are some common challenges with using these adhesives?
A: Sometimes, manufacturers use lamps that emit the wrong type of light for the specific adhesive formulation. Manufacturing processes can also leave inadequate cure time. If a UV/light cure adhesive is stored improperly, such as in a clear bottle that receives sunlight, premature curing may occur. Like other materials, UV/light cure adhesives also have a shelf life beyond which a product becomes unfit for use. If an adhesive fails to stick, however, it’s often because it was the wrong choice for the substate.
Q: Which substrates can be bonded with UV/light cure adhesives?
A: Glass is one of the most popular substrate materials for UV/light cure adhesives and can form high-strength, load-bearing bonds between glass-and-glass, glass-and-plastic, or glass-and-metal. Optical plastics can be joined as well, but materials with low surface energy may produce joints with insufficient strength. With Teflon, for example, a surface treatment such as chemical etching can increase surface energy and contribute to the formation of non-structural bonds.
Q: Will any UV lamp work for adhesive curing?
A: No. The key is to use a lamp with a spectral output and intensity that matches the requirements of the adhesive. The lamps used for UV/light curing are specified by size or cure area, spectral output or wavelength, and power in W/cm2. Some adhesive formulations are curable with a black light, a relatively inexpensive lamp that emits UV-A; however, the time needed for curing is too long for most production schedules. More powerful lamps can cure adhesives more quickly.
Q: What is the intensity that a UV/light cure adhesive need?
A: UV/light cure adhesives are designed to cure at specific wavelengths that are measured in nanometers (nm). Visible light has colored bands that range from violet (380-435 nm) to red (625-740 nm). UV light is divided into UV-A (315-400 nm), UV-B (280-315 nm), and UV-C (180-280 nm) but covers a region of the electromagnetic spectrum that is as low as 10 nm. Visible light curing adhesives typically cure from 385nm to 415nm, depending on the formulation. Today, many UV cure adhesives use 365 nm light.
Q: What are the advantages and disadvantages of using LED lamps for adhesive curing?
A: Lamps that use light emitting diodes (LEDs) have longer-lasting bulbs, use less energy, and produce less heat. They also create strong bonds because their light output can be tightly focused on the required wavelength for optimum cure. Unlike metal halide lamps, however, LED lamps cannot provide the broad performance that may be needed if manufacturers decide to use various UV/light cure adhesives with different curing requirements.
Q: How do metal halide lamps compare to LEDs?
A: Metal halide lamps use more energy, but some UV/light cure adhesives need them in order to cure quickly and with all of an adhesive’s end-use properties. Plus, a standard 365 nm metal halide lamp covers a broad spectrum ranging from visible light to UV-B. Yet, metal halide lamps have a shorter life than LED lamps. Metal halide curing lamps also degrade with first use and may have power issues even when they light-up. This can contribute to inadequate curing.
Q: What about microwave-powered UV curing lamps?
A: Microwave-powered, or excited, UV curing lamps have a longer life than traditional metal halide lamps but are more expensive. They are available in commonly used wavelengths and feature an electrodeless bulb that has a long lifetime and applies less heat to the substrate. Microwave-powered UV lamps with integrated blowers are sometimes used in laboratories or other facilities where space is limited.
Q: Besides using the wrong lamp, what are some other curing problems and solutions?
A: Because light energy is required for curing, UV or visible light must reach the bond area. This requires an unobstructed path between the light source and at least one substrate. Part designs that lack fillets or similar geometries may experience “shadowing” and require an adhesive with a secondary moisture cure for complete adhesion. For bonding magnets to metals, an activator that initiates the adhesive reaction may be required. To bond silicone, a UV cure adhesive with a silicone chemistry may be needed.
Q: What are some common adhesive chemistries?
A: The most common chemistries for UV/light curing adhesives are acrylated urethanes. These industrial adhesives have good performance properties, can bond to most materials, and are the least expensive. Cyanoacrylate adhesives are used with tubing and to bond some plastics. Epoxies produce strong bonds but tend to be rigid, which can lead to fracture. Silicones are the most expensive type of adhesive and are available in some formulations that cure with visible light.
Q: What are some considerations for production efficiency?
A: Lamps need to be installed at the proper distance and, depending on the application, may need to provide either flood or focused light. For example, if an adhesive is dispensed onto a printed circuit board (PCB) to bond a small electronic component, a high-intensity spot lamp may be a better choice than a UV/visible conveyor or flood lamp.
Adhesive dispensing can be done automatically but is often done manually instead. For higher production volumes, a robotic dispenser can provide a relatively quick return on investment (ROI). Even a simple desktop robot offers advantages in terms of speed, consistency, and reliability. For spot dispensing, a robot equipped with a light wand can be used for curing – if the light is shielded from the dispense tip, to prevent curing in the tip.
Q: Besides light intensity, what are some key product specifications to consider?
A: Strength is especially important. Manufacturers list this information on an adhesive’s data sheet in terms of pounds per square inch (psi) or its metric equivalent. Shear strength, a property that describes an adhesive’s resistance against a shear load before failure, is typically measured with an Instron. Speed of cure and depth of cure are also critical because engineers need adhesives that cure quickly but completely. Viscosity is application-dependent and determines whether an adhesive spreads easily or remains in a bead. Typically, depth of cure and viscosity are more important for pottants and encapsulants than for bonding or conformal coatings.
Q: Do UV/light cure adhesives come in different colors – and what about optical properties?
A: UV/light cure adhesives typically do not come in colors, although some are available in black. Clarity counts because color absorbs light and can affect curing. Consequently, most UV cure adhesives are clear, translucent, or opaque. For glass or plastic surfaces where the coating or bonding layer should not be visible, such as in optical applications, choose an adhesive with the same refractive index as the substrate material itself. Not all data sheets list optical specifications, however.
Q: Is there anything else design engineers should know?
A: Selecting UV/light cure adhesives requires a complete analysis of factors that include substrate materials, part design, surface energy, wavelength, and lamp selection and installation. Typically, these industrial adhesives are supplied in black syringes, black bottles, or opaque pails. When evaluating suppliers, it helps to choose one who can help with product selection and provide technical assistance. Price, availability, and minimum order quantities (MOQs) are also important considerations.