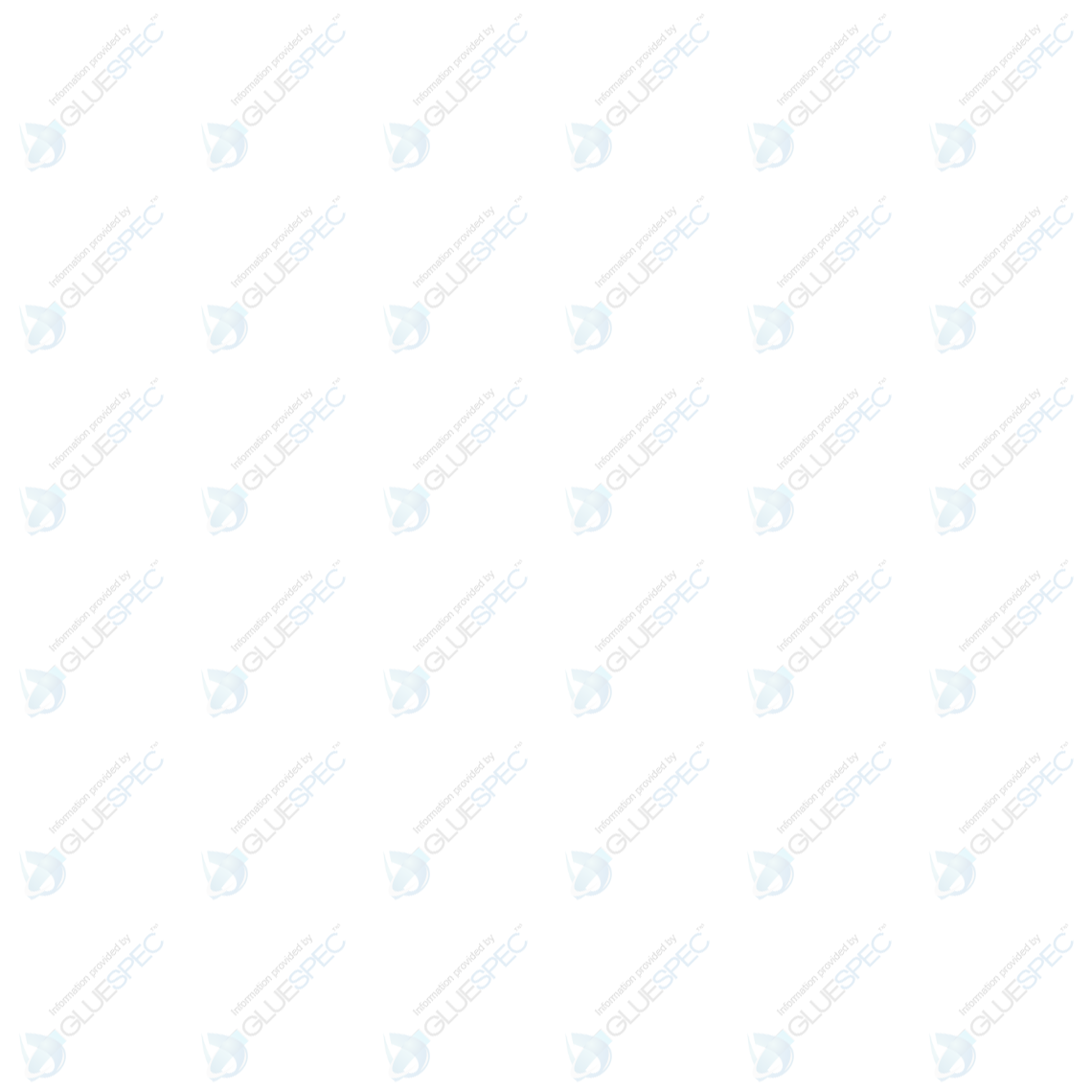
- Contributions by industrial experts with engineers in mind
- Focused on specialty-chemical material applications and selection
Knowledge Center
Potting and Encapsulation in the Electronics Industry
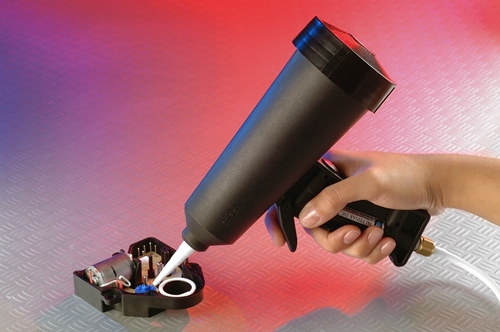
Electronics Potting and Encapsulation
In the electronics industry pottants and encapsulants are used frequently to protect assemblies of all types. The most common uses for potting are protecting against moisture and electrical insulation. Potting can also protect PCBs and other components from thermal and physical shock, chemical attack and act as a physical barrier to deter tampering or intellectual property theft.
The terms "potting" and "encapsulation" are often used interchangeably, but technically, potting refers to a process where the shell or "pot" that is filled with resin becomes a part of the finished component. In encapsulation, the component and hardened resin are then removed from the pot to be placed in an assembly.
When potting electronic assemblies, a number of factors need to be taken into consideration, as different compounds will be used depending on the type of protection desired, expected environmental conditions and layout of components.
Types of Potting Compounds for Electronics Encapsulation
There are three major types of potting compounds – epoxies, urethanes, and silicone. Each has its strengths and drawbacks, and is suitable to particular uses.
Epoxies
Epoxies offer excellent chemical resistance and temperature resistance up to 200C. They provide excellent strength to ruggedize components and high dielectric strength for electrical applications, making them ideal for use in high-voltage applications. They can become brittle in low temperatures, and the heat of reaction and shrinkage during curing can be a problem for sensitive components. Therefore matching the reactivity and exotherm is an important factor in choosing a material. There are some low-stress potting materials on the market designed for potting SMT populated boards where this is a key factor.
"UV Curing compounds can be a good option, particularly when concerns over curing time are paramount."
Urethanes
Urethanes are generally more flexible than epoxies, putting less strain on potted components in general. They offer better performance in applications with thermal cycling and in low-temperature environments (down to -40C or lower). However, these potting compounds are generally less resistant to chemicals and high temperatures (above 130C). Urethanes can sometimes be more difficult to work with than epoxy or silicone as the isocyanate portion is reactive with moisture in the air, and the polyol portion can absorb moisture, causing problems when mixed.
Silicones
Silicones offer excellent flexibility and operate over the widest temperature range. They are also resistant to many chemicals and liquid water, UV light and ozone. However, they are often the most expensive option, and may not be suited to applications where high rigidity is needed. They also have relatively high CTE, which can sometimes cause problems in applications with high thermal cycling. The most common type for electrical potting are platinum cured, since they can cure in any thickness or cross section, but the Pt catalyst is also subject to inhibition by many materials, sulfur, amines, plasticizers, etc. so care must be taken to assure compatibility.
Other types of potting compounds for electronic encapsulation
There are other types of potting compounds that may be applicable in specific situations. These compounds are often described by their end-use or cure method and can be formulated using epoxy, urethane or silicone bases.
UV Curing compounds can be a good option, particularly when concerns over curing time are paramount. UV curing allows compounds to cure in seconds, but may not be able to cure fully especially in thick potting or encapsulations or ones with shadowed areas. Formulations with secondary heat, moisture or chemical cures can allow complete curing in those applications.
Thermally conductive potting compounds are compounds that have a heat-conductive filler added. These compounds can be used when heat-producing components would be too insulated by a regular potting compound. While they provide some thermal dissipation, heat sinks are sometimes needed and can be potted as well. Levels of thermal conductivity up to 1.0 to 1.25 W/mK are common in industrial grade and commodity-focused products, but higher levels are possible if more exotic fillers are used.
Hot melt thermoplastic polyamide polymers can be used for potting as well. These are made from a thermoplastic that is heated and molded around components. This can be an excellent option for creating a watertight enclosure that sets quickly, and can also be UL rated.
Avoiding damage during potting
There are two main dangers to components when potting. The first is that heat from the curing reaction will cause damage to delicate components. If the components being potted are sensitive to heat, it will be important to choose a compound that either gives off a low amount of heat during curing, or that dissipates heat more easily, like a thermally conductive potting compound. The second danger is that shrinkage of the potting compound during curing may damage sensitive components or solder bonds. This can be avoided by choosing a potting compound that shrinks less or is more flexible.